3D Systems and GF Machining Solutions Announce DMP Factory 500 - Integrating the Best of Additive and Subtractive to Transform Manufacturing
- New modular solution is optimized for scalability, repeatable high quality parts, high throughput and low total cost of operation - Combined global distribution network facilitates access to application experts to optimize manufacturing environments, and maximize up-time with timely, local support
3D Systems (NYSE : DDD ) and Georg Fischer AG's Division (FI/N:SIX Swiss Ex) GF Machining Solutions today announced their first joint solution, the DMP Factory 500 a scalable manufacturing system designed to transform metal manufacturing through simplified workflows to build higher quality seamless metal parts up to 500 mm x 500 mm x 500 mm with lower total cost of operation.
The DMP Factory 500 is a customizable solution comprised of five function-specific modules:
Printer Module (PTM): designed to withstand the rigors of 24/7 production cycles enabling maximum printer uptime and output.
Removable Print Module (RPM): sealed module for powder and part transport between printer, powder, and transport modules featuring a vacuum chamber to ensure the lowest O2 content enabling high quality 3D printed metal parts. Powder waste is eliminated, as the vacuum chamber guarantees consistent high material quality, sufficient to be re-used to depletion.
Powder Management Module (PMM): efficiently de-powders parts on build platforms, automatically recycles unused powder materials, and prepares the RPM for the next build.
Transport Module (TRM): enables efficient movement of the RPMs between printer and powder modules - reducing production time.
Parking Module (PAM): provides interim storage of RPMs in an inert environment until ready for further progression in the workflow (e.g., stores a fully prepared RPM for its next print job while the PTM is finishing the previous print job).
The modular design of the DMP Factory 500 enables continuous function of all metal 3D printing and powder management modules to maximize uptime, throughput and operational value. The ability for a manufacturer to create a custom solution - matching the number and type of modules required for their production workflow - helps maximize their investment, while the integrated automation minimizes manual processes to reduce total cost of operation. In addition, the DMP Factory 500 system includes seamless data connectivity with all major ERP systems to facilitate supply chain optimization.
The robust additive manufacturing platform is integrated with GF Machining Solutions' System 3R referencing and clamping system. Zero point clamping enables optimal positioning of the build plate, facilitating a quick transition from the 3D printer to post-processing steps. This integrated feature reduces set-up times and provides enhanced flexibility by quickly transitioning the build plate from the additive process and sending it downstream for post-processing, saving significant time and money.
"This partnership joins two industry leaders in additive and subtractive manufacturing to deliver a solution that will change production manufacturing environments," said Pascal Boillat, president, GF Machining Solutions. "The blending of GF Machining Solutions' precision machining expertise with 3D Systems' standard-setting additive manufacturing technologies will ultimately redefine metal parts production."
Automation of the additive manufacturing process is a top priority of this solution, and the companies are focused on developing solutions to seamlessly integrate additive manufacturing technology into the complete manufacturing process chain. To facilitate this, GF Machining Solutions has filed a patent application for a new carrier concept. This flexible solution allows the user to position and locate build plates on the Removable Print Module and provides links to automated conventional machining processes. This concept will contribute significantly to increased automation possibilities and reduction of build plates costs.
The DMP Factory 500 Solution is complemented by integrated software including 3D Systems' 3DXpert™ to manage the 3D printing workflow from design to manufacture. Additionally, DMP Monitoring facilitates real-time process monitoring to enable informed decisions on product quality.
Combining 3D Systems' and GF Machining Solutions' sales and support networks, DMP Factory 500 customers will have access to a distribution network operating in more than 50 countries. In addition to local technical support, customers will have access to metals manufacturing applications experts at Customer Innovation Centers (CICs) in Leuven, Belgium; Denver, Colorado and Stabio, Switzerland. Customers will be able to collaborate with application engineers in these locations to optimize their DMP Factory 500 system to meet their unique business needs.
"The DMP Factory 500 is transforming and redefining how manufacturing gets done," said Vyomesh Joshi, president and chief executive officer, 3D Systems. "Through our partnership with GF Machining Solutions, manufacturers will have a solution that combines additive and subtractive manufacturing and provides a simplified workflow. As manufacturing continues to advance, customers will start to expect high quality, large part production with significantly reduced total cost of operation, and with the DMP Factory 500, that's exactly what they'll get."
The companies are debuting this first combined solution in conjunction with IMTS 2018 this week in Chicago (3D Systems Booth#431608, GF Machining Solutions Booth #338754).
About 3D Systems
3D Systems is the originator of 3D printing and an innovator of future 3D solutions. It has spent its 30-year history enabling professionals and companies to optimize their designs, transform their workflows, bring groundbreaking products to market and drive new business models. This is achieved with the Company's best of breed digital manufacturing ecosystem. It's comprised of plastic and metal 3D printers, print materials, on demand manufacturing services and end-to-end manufacturing software solutions. Combinations of these products and services address a variety of advanced applications- ranging from Aerospace, Automotive, and Consumer Goods to Medical, Dental, and Jewelry. For example, 3D Systems' precision healthcare capabilities include simulation, Virtual Surgical Planning, and printing of medical and dental devices as well as patient-specific surgical instruments. More information on the company is available at www.3dsystems.com.
About GF Machining Solutions
GF Machining Solutions is the world's leading provider of machines, diverse technical solutions and services not only to the tool and mold making industry but also to manufacturers of precision components. The portfolio ranges from electrical discharge machines, high-speed and high-performance Milling machines—including clamping and palletization systems, 3D Laser surface texturing machines and Spindles—to solutions for Tooling and Automation, services, spare parts, expendable parts, consumables and Digitalization solutions. GF Machining Solutions is a globally acting Division of the Georg Fischer Group (Switzerland) and maintains a presence on 50 sites worldwide within its own organization. Its 3,255 employees generated sales of CHF 992 million in 2017. More information can be found at www.gfms.com.
Featured Product
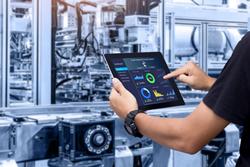