New Innovations in Medical Plastics: Insert Molding/Over Molding
There are new innovations in the medical field every day. From new drugs to new surgical tools, the entire practice looks extremely different than it did even five years ago. One aspect of the healthcare field that has seen significant change over the years is the process by which molded medical devices are created. The techniques have been perfected over the years to be both more efficient and cost effective through innovative manufacturing approaches. There are two methods typically seen in this field: Over Molding and Insert Molding.
There are new innovations in the medical field every day. From new drugs to new surgical tools, the entire practice looks extremely different than it did even five years ago. One aspect of the healthcare field that has seen significant change over the years is the process by which molded medical devices are created. The techniques have been perfected over the years to be both more efficient and cost effective through innovative manufacturing approaches. There are two methods typically seen in this field: Over Molding and Insert Molding.
Over Molding
This form of molding occurs in a two-step process. First, one original part is injection molded. After this, a second injection molding step takes place whereby molding resin is injected over the initial part, forming a hermetically sealed unit. Essentially, you would start with a base molded component and then mold a second plastic layer around the original part, creating a single finished product.
If this process is not executed with the utmost precision, the finished device can have multiple molding defects such as distortions, gaps, and stress cracks.
Insert Molding
Although similar to over molding, this process takes something other than a plastic component and places it into a mold cavity to then be molded into a final product. The result is a single piece encapsulated in the specified plastic. The idea behind this process is that a wide variety of items can be custom manufactured and incorporated into the molding design. Examples of this include needles, tubing or other extrusions, filter membranes, metal instruments, and miniature electrical components.
Benefits of both Over Molding and Insert Molding
Assembly - In terms of medical molding, many are finding insert molding to be an extremely efficient strategy. One reason behind this is the idea of in-line assembly stations that incorporate the insert molding process. Otherwise, often the original device will need to go through entirely separate assembly lines.
Size and Weight - Because there are no connectors, adhesives, or fasteners required in insert molding, the product tends to be significantly lighter or more streamlined than products made from other techniques.
Performance - Because of the nature of insert molded thermoplastics, the performance of the part may be superior to the performance of parts made by other techniques. This is due to the security of the part. There is no risk of malfunctioning if a bonded joint comes loose for instance.
Design Flexibility - Unlike many other techniques, insert molding can provide a freedom in the design and labeling of the product. Designers essentially have unlimited configuration options through insert molding. Designers also have the option of adding identification numbers and logos onto the molded part.
Cost - Insert molding can reduce the final costs of the product by limiting the number of steps needed to create the part. Typically, expensive labor steps could be required in the process, however, insert molding has eliminated the need for this using only one single operation, thus decreasing overall costs
Medical insert molding is a core technology of Aberdeen Technologies. The company has expert designers and process technicians who can assist you with any of your unique medical molding needs. Contact Aberdeen Technologies today to ensure quality and efficiency for your next project.
Featured Product
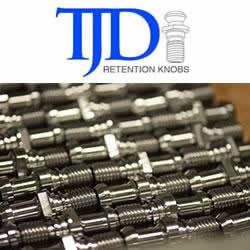