3D Currax Makes a Splash at RAPID + TCT's Kickoff
Keynote Speaker Todd Grimm IDs the pioneering 3D Manufacturer as a “Cant Miss” Company
Attendees at RAPID + TCT, North Americas leading conference for 3D manufacturers and researchers, will want to mark down April 23, 2018 as the date they first heard about 3D Currax Solutions. Three years from now when the additive manufacturing R & D company is turning the industry on its head, theyll remember where they were when it became mainstream.
Todd Grimm, President of T. A. Grimm & Associates and a 25-year veteran of the additive manufacturing/3D printing industry, specifically mentioned 3D Currax in his keynote presentation at the conferences kickoff on Monday at the Fort Worth Convention Center. In his "Cant Miss" roundup of the latest products in 3D printing and scanning he said, "3D Currax has been privately developing technology that will advance production of mainstream products with a key focus on a process that can make optimal parts for their intended use...(it) took the combination of advanced additive manufacturing, custom robotics, AI, machine learning and development of key proprietary technology. In the end, they have designed an end-to-end system that makes finished 3D printed parts with no human interaction needed."
3D Currax was founded in 2015 by CEO Barry Mills, who has been developing advanced 3D printing systems capable per-part production speeds that are less than those found in injection molding. This allows industries reliant on mass production and rapidly-changing technologies, such as automotive, toy and healthcare, to make better designed parts faster and with more versatility, efficiency, and customizability.
"Just like Henry Ford revolutionized the production process for cars and changed the way people traveled forever, were saying the status quo isnt good enough anymore and want to transform how manufacturers produce and bring their products to market," said Mills.
Mills says the company is poised to grow exponentially pending investment to build its MRK III and MRK X machines, which are designed for dental/educational and manufacturing enterprises. Having them readily available puts 3D Currax in direct competition with global plastics manufacturing, an industry worth approximately $462 billion.
"The market were targeting is as-yet untouched for the additive manufacturing industry," said Mills. "Were going up against this behemoth but with the ability to produce parts faster and more efficiently, plus the added bonus of producing extremely complex parts. It truly is a David and Goliath type of scenario."
3D Currax currently houses a team of 26 employees and subcontractors out of its headquarters in British Columbia, Canada, and is looking for expansion into a larger U.S. facility. For more information about its technology and machines, go to http://www.3dcurrax.com.
Featured Product
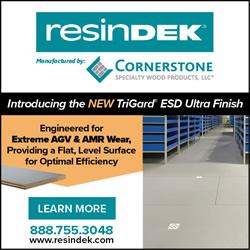
ResinDek® TRIGARD® ESD ULTRA FOR HIGH-TRAFFIC ROBOTIC APPLICATIONS
To maximize the productivity of an autonomous mobile robot (AMR) or automatic guided vehicle (AGV) deployment, it's critical to create the optimal environment that allows the vehicles to perform at their peak. For that reason, Cornerstone Specialty Wood Products, LLC® (www.resindek.com) created the TriGard® ESD Ultra finish for its ResinDek® engineered flooring panels. The TriGard ESD Ultra finish is ideal for high-traffic robotic applications characterized by highly repetitive movement patterns and defined travel paths.