America Makes Announces Project Call Awardees
Award Announcement Coincides with the Start of RAPID + TCT 2018 Exhibits; Seven Teams Awarded; 24 Industry Leading Organizations Teaming to Advance Additive Manufacturing Technologies for Low-Cost Sustainment Program Crucial to U.S. Air Force Strategic Readiness
Youngstown, Ohio — April 24, 2018. To coincide with the opening of exhibits at RAPID + TCT 2018, America Makes proudly announces the awardees of its Project Call for additive manufacturing (AM) projects for Phase 3 of the "Maturation of Advanced Manufacturing for Low-Cost Sustainment (MAMLS)" program, funded by the Air Force Research Laboratory (AFRL), Materials and Manufacturing Directorate, Manufacturing and Industrial Base Technology Division.
With the addition of this Project Call, America Makes will soon have a portfolio of more than $115M in public and private funds invested in advancing the state-of-the-art in AM in the United States.
"We are excited to be announcing the awardees of our latest Project Call at the kick off of exhibits at the additive manufacturing industrys largest event, RAPID + TCT 2018," said America Makes Executive Director Rob Gorham. "These seven awarded applied research and development projects will have a tremendous impact on ensuring the strategic readiness of the U.S. Air Force. The anticipated project outcomes will empower the sustainment community to adopt advanced additive manufacturing technologies, improving rapid part replacement/maintenance for legacy aircraft, enabling on-demand replacement of critically damaged or obsolete components, and reducing the cost and lead time to fabricate replacement components. We congratulate the winning project teams and look forward to getting these projects underway."
The MAMLS program is aimed at improving efficiency of the factory and/or U.S. Air Force (USAF) Air Logistics Complexes for rapid part replacement for legacy and other aircraft. The objective of this Project Call effort is to address key challenges, as well as explore new, less mature processes, impeding the insertion of AM technology for maintenance, sustainment, and logistics operations within the Department of Defense (DoD) that were previously identified throughout MAMLS Phases 1 and 2, and those also identified in the America Makes Technology Roadmap. The focus of the Phase 3 Project Call is of great significance to the AFRL. The previously identified Phases 1 & 2 material, process, and post-processing barriers are not only preventing greater penetration of AM technologies for more challenging, safety critical applications, but also impeding the fulfillment of the extensive breadth of parts required by the USAF sustainment community.
This Project Call, which was released in November 2017, focused on three (3) technical topics that would have the most potential and greatest impact for defense maintenance, sustainment and logistics operations, and the overall strategic readiness of the USAF and the DoD.
Subject to the finalization of all contractual details and requirements, the seven selected America Makes Project Call Awardees, organized by the three (3) technical areas, are as follows:
TOPIC AREA 1 - Feature-based Qualification Using Directed Energy Deposition
"Featured-based Qualification Method for Directed Energy Deposition AM"
-- General Electric (GE)
Led by GE, in collaboration with EWI, Raytheon, and Youngstown State University, this project will develop and demonstrate a process methodology of feature-based build qualifications (FBQs) using a directed energy deposition (DED) process. This FBQ approach is targeted to significantly reduce the time and cost to qualify new DED manufactured parts, particularly in instances where legacy supply chains are no longer available, enabling more rapid adoption and deployment of DED technology. This project will use example components representative of aircraft engine and missile-based applications to develop, build, and test a method of FBQ for additively manufactured components. The AM build process will be focused on laser blown powder deposition modality using Ti-6Al-4V material. A method will also be developed and demonstrated utilizing a hybrid-physics-based process modeling approach that incorporates uncertainty to predict material properties related to geometric features, process parameters, and build method. The build structure, material properties, and geometric features of interest will drive test planning.
TOPIC AREA 2 - Understanding Manufacturing Realities of AM
"Accelerating MAMLS Direct Part Production: Effects of Defects in Laser Powder Bed Fusion AlSi10Mg"
-- Youngstown State University (YSU)
Led by YSU, in collaboration with 3D Systems, Boeing, Case Western Reserve University (CWRU), Lockheed Martin, Oerlikon, Penn State Applied Research Laboratory (ARL), University of Dayton Research Institute (UDRI), and Vibrant, this project will accelerate the transition of laser powder bed fusion (LPBF) produced AlSi10Mg components for USAF aerospace applications, including the MAMLS Phase 2 bell crank family of parts, heat exchangers, tactical fighter drag chute frames, and replacement of castings for out-of-production aircraft. While MAMLS Phase 2 efforts included establishing the performance of parts fabricated with nominal process parameters, this research effort will specifically focus on rogue defects, such as lack of fusion (LoF) defects and powder contamination. Because the strength and fatigue life capability of airframe parts can be significantly degraded by the presence of these rogue flaws from the LPBF process, these flaws will be identified using a variety of detection methods so that the subsequent impact of the these flaws can be addressed and resolved in the design of AM parts in order to satisfy structure requirements.
"Understanding Stochastic Powder Bed Fusion AM Flaw Formation and Impact on Fatigue"
-- Penn State Applied Research Laboratory (ARL)
Led by Penn State ARL, in collaboration with 3D Systems; Moog, Inc.; Oerlikon; United Technologies Research Center (UTRC), this project will strive to minimize the seemingly random and sporadic stochastic flaws that occur in components produced by laser powder bed fusion (LPBF), even when manufactured under optimized processing conditions. These naturally occurring stochastic flaws negatively impact fatigue properties, thereby limiting the ability to define design limits and hampering qualification efforts, and preventing the widespread use of AM in many critical applications of interest to the USAF and the aerospace sustainment community. The goal of this project is to quantify the effect of defects by building a high quantity of fatigue samples to generate statistically significant, pedigreed Ti-6Al-4V fatigue data from numerous stochastic flaws, enabling the project team to define the link between the process, the flaw characteristics, and fatigue performance. All manufacturing and test data will be collected and stored using the Data Management System for Additive Manufacturing (DMSAM) as the primary deliverable of the project. Additionally, a parallel effort will also be undertaken to develop improved understanding of the nature of flaw-formation mechanisms and the factors that lead to stochastic flaws.
"Evaluation of Defects in Metal LPBF AM Using Multiple Lasers"
-- The Ohio State University (OSU) Center for Design & Manufacturing Excellence (CDME)
Led by The OSU CDME, in collaboration with GE Additive and Proto Precision Manufacturing Solutions, this project will aim to understand the metallurgical defects in multiple laser powder bed fusion (LPBF) systems and apply non-destructive examination (NDE) methods in order to identify potential defects in service. Currently, parts that are uneconomical to produce with single-laser LPBF systems can be made cost effectively by the productivity improvement from multiple lasers. While many LPBF machine manufacturers are now offering commercially available equipment with two and four lasers, the industry lacks an understanding of the potential metallurgical defects arising from the use of multiple lasers. Moreover, an openly available library or design guidelines do not exist within the industry. This project will analyze the defects in printed nickel alloy 718 and deliver a test artifact, technical data package, and new standards as the foundation for end users to overcome the existing technical barriers and confidently implement new higher productivity metal AM equipment with multi-laser LPBF systems.
TOPIC AREA 3 - Emerging Process Technology for Low Criticality Part Families
"Demonstration of 3D Composite Based AM (CBAM) Build Process for Low Criticality Part Families"
-- Utah Advanced Materials and Manufacturing Initiative (UAMMI)
Led by the UAMMI, in collaboration with Impossible Objects (IO) and the Utah Composites Lab, this project will demonstrate and evaluate 3D composite-based AM (CBAM) capability as a viable option to generate non-critical, non-structural components that satisfactorily fulfill the required part function for the USAF and the sustainment community. Waiting on parts is a significant driver of maintenance down time in legacy systems and one that the Air Force Sustainment Center has worked to resolve the root causes, which include obsolescence, Diminishing Manufacturing Sources and Material Shortages (DMSMS), and never-before seen failures on parts not originally planned needing replacement. The goal of this project is to prove out and accelerate CBAM technology and to build a body of CBAM knowledge for todays non-critical part replacements and tomorrows implementations throughout the industry and other various DoD sustainment operations. CBAM will also be assessed in how it extends to part families of similar size, shape, criticality, and function.
"AM of Low Criticality Part Families via Continuous Liquid Interface Production"
-- United Technologies Research Center (UTRC)
Led by UTRC, in collaboration with Carbon, UTC Aerospace Systems, and Pratt and Whitney, this project will investigate the capability of Carbons emerging Continuous Liquid Interface Production (CLIP) process and supporting fabrication technologies to advance the Manufacturing Readiness Level (MRL) related to the AM of low-criticality polymer components for aerospace applications with a specific emphasis on masks, enclosures, and ducting. Shot peening masks, electrical enclosures, and ducting are low criticality parts with ubiquitous use in aerospace systems, and the development of additively manufactured surrogates will greatly enhance the ability to be agile to DoD supply chain requests. In addition to exploring the CLIP process in its capabilities to manufacture low criticality components, this project also aims to demonstrate a complete end-to-end digital additive workflow, which encompasses part digitalization, design optimization, print process optimization, materials characterization, and component performance validation.
"Rapid Part Replacement via Digital Light Processing"
-- University of Dayton Research Institute (UDRI)
Led by UDRI, in collaboration with 3D Systems, Lockheed Martin, Orbital ATK, and Northrop Grumman, this project will evaluate the ability of Digital Light Processing (DLP) technology, specifically the Figure 4™ machine being pioneered by 3DSystems, to supply the USAF low criticality components, including electrical connectors, knobs, elastomeric grommets, and spacers for legacy sustainment equipment. With DLP, a photopolymer is drawn out of a resin bath and rapidly cured by an underlying image projector. It cures the entire part slice at once as compared to other toolpath-based AM technologies and enables fine resolution, smooth surfaces, novel material chemistries, and the fast print speeds. This project will identify and overcome technological and materials science barriers associated with DLP through part-family-specific testing, characterization, and post-processing; demonstrate rapid part replacement; and establish a clear technology development, vetting, and USAF transition pathway for Figure 4 technology.
"From a technical perspective, the response to the Project Call was phenomenal in that the approaches outlined in the submitted proposals were very interesting and innovative, showing a solid understanding of the ideal outcomes that we were driving toward in each of the three topic areas," said John Wilczynski, America Makes Technology Director. "Going into this Project Call, we planned for multiple awards. Given the quality of the submissions, we would have liked to make more awards. For the seven award project teams, theres no doubt that the project results will not only transform the sustainment community, but will also have a far-reaching impact beyond, regardless of industry."
The anticipated start date of the projects is June 2018.
For more information on the Project Call or how to become an America Makes member, visit the America Makes Web site at http://americamakes.us and follow the Institute on Twitter @AmericaMakes. Visit America Makes at RAPID + TCT 2018 at booth #2439.
###
About America Makes
America Makes is the National Additive Manufacturing Innovation Institute. As the national accelerator for additive manufacturing (AM), America Makes is the nations leading and collaborative partner in AM and 3DP technology research, discovery, creation, and innovation. Structured as a public-private partnership with member organizations from industry, academia, government, non-government agencies, and workforce and economic development resources, we are working together to innovate and accelerate AM to increase our nations global manufacturing competitiveness. Based in Youngstown, Ohio, America Makes is the first Institute within the Manufacturing USA infrastructure and is driven by the National Center for Defense Manufacturing and Machining (NCDMM). For more information about America Makes, visit http://americamakes.us.
About NCDMM
NCDMM delivers innovative and collaborative manufacturing solutions that enhance our nations workforce and economic competitiveness. NCDMM has extensive knowledge and depth in manufacturing areas—both commercial and defense—to continually innovate, improve, and advance manufacturing technologies and methodologies. Our experienced team specializes in identifying the needs, the players, the technologies, and processes to attain optimal solutions for our customers. We connect the dots. Thats the NCDMM methodology. NCDMM also manages the national accelerator for additive manufacturing (AM) and 3D printing (3DP), America Makes—the National Additive Manufacturing Innovation Institute. For additional information, visit the NCDMM at http://ncdmm.org/.
Youngstown, Ohio — April 24, 2018. To coincide with the opening of exhibits at RAPID + TCT 2018, America Makes proudly announces the awardees of its Project Call for additive manufacturing (AM) projects for Phase 3 of the "Maturation of Advanced Manufacturing for Low-Cost Sustainment (MAMLS)" program, funded by the Air Force Research Laboratory (AFRL), Materials and Manufacturing Directorate, Manufacturing and Industrial Base Technology Division.
Driven by the National Center for Defense Manufacturing and Machining (NCDMM), America Makes and AFRL are targeting to make available approximately $6.5M to fund multiple awards with at least $3.3M in matching funds from the awarded project teams for total funding worth roughly $9.8M.
With the addition of this Project Call, America Makes will soon have a portfolio of more than $115M in public and private funds invested in advancing the state-of-the-art in AM in the United States.
"We are excited to be announcing the awardees of our latest Project Call at the kick off of exhibits at the additive manufacturing industrys largest event, RAPID + TCT 2018," said America Makes Executive Director Rob Gorham. "These seven awarded applied research and development projects will have a tremendous impact on ensuring the strategic readiness of the U.S. Air Force. The anticipated project outcomes will empower the sustainment community to adopt advanced additive manufacturing technologies, improving rapid part replacement/maintenance for legacy aircraft, enabling on-demand replacement of critically damaged or obsolete components, and reducing the cost and lead time to fabricate replacement components. We congratulate the winning project teams and look forward to getting these projects underway."
The MAMLS program is aimed at improving efficiency of the factory and/or U.S. Air Force (USAF) Air Logistics Complexes for rapid part replacement for legacy and other aircraft. The objective of this Project Call effort is to address key challenges, as well as explore new, less mature processes, impeding the insertion of AM technology for maintenance, sustainment, and logistics operations within the Department of Defense (DoD) that were previously identified throughout MAMLS Phases 1 and 2, and those also identified in the America Makes Technology Roadmap. The focus of the Phase 3 Project Call is of great significance to the AFRL. The previously identified Phases 1 & 2 material, process, and post-processing barriers are not only preventing greater penetration of AM technologies for more challenging, safety critical applications, but also impeding the fulfillment of the extensive breadth of parts required by the USAF sustainment community.
This Project Call, which was released in November 2017, focused on three (3) technical topics that would have the most potential and greatest impact for defense maintenance, sustainment and logistics operations, and the overall strategic readiness of the USAF and the DoD.
Subject to the finalization of all contractual details and requirements, the seven selected America Makes Project Call Awardees, organized by the three (3) technical areas, are as follows:
TOPIC AREA 1 - Feature-based Qualification Using Directed Energy Deposition
"Featured-based Qualification Method for Directed Energy Deposition AM"
-- General Electric (GE)
Led by GE, in collaboration with EWI, Raytheon, and Youngstown State University, this project will develop and demonstrate a process methodology of feature-based build qualifications (FBQs) using a directed energy deposition (DED) process. This FBQ approach is targeted to significantly reduce the time and cost to qualify new DED manufactured parts, particularly in instances where legacy supply chains are no longer available, enabling more rapid adoption and deployment of DED technology. This project will use example components representative of aircraft engine and missile-based applications to develop, build, and test a method of FBQ for additively manufactured components. The AM build process will be focused on laser blown powder deposition modality using Ti-6Al-4V material. A method will also be developed and demonstrated utilizing a hybrid-physics-based process modeling approach that incorporates uncertainty to predict material properties related to geometric features, process parameters, and build method. The build structure, material properties, and geometric features of interest will drive test planning.
TOPIC AREA 2 - Understanding Manufacturing Realities of AM
"Accelerating MAMLS Direct Part Production: Effects of Defects in Laser Powder Bed Fusion AlSi10Mg"
-- Youngstown State University (YSU)
Led by YSU, in collaboration with 3D Systems, Boeing, Case Western Reserve University (CWRU), Lockheed Martin, Oerlikon, Penn State Applied Research Laboratory (ARL), University of Dayton Research Institute (UDRI), and Vibrant, this project will accelerate the transition of laser powder bed fusion (LPBF) produced AlSi10Mg components for USAF aerospace applications, including the MAMLS Phase 2 bell crank family of parts, heat exchangers, tactical fighter drag chute frames, and replacement of castings for out-of-production aircraft. While MAMLS Phase 2 efforts included establishing the performance of parts fabricated with nominal process parameters, this research effort will specifically focus on rogue defects, such as lack of fusion (LoF) defects and powder contamination. Because the strength and fatigue life capability of airframe parts can be significantly degraded by the presence of these rogue flaws from the LPBF process, these flaws will be identified using a variety of detection methods so that the subsequent impact of the these flaws can be addressed and resolved in the design of AM parts in order to satisfy structure requirements.
"Understanding Stochastic Powder Bed Fusion AM Flaw Formation and Impact on Fatigue"
-- Penn State Applied Research Laboratory (ARL)
Led by Penn State ARL, in collaboration with 3D Systems; Moog, Inc.; Oerlikon; United Technologies Research Center (UTRC), this project will strive to minimize the seemingly random and sporadic stochastic flaws that occur in components produced by laser powder bed fusion (LPBF), even when manufactured under optimized processing conditions. These naturally occurring stochastic flaws negatively impact fatigue properties, thereby limiting the ability to define design limits and hampering qualification efforts, and preventing the widespread use of AM in many critical applications of interest to the USAF and the aerospace sustainment community. The goal of this project is to quantify the effect of defects by building a high quantity of fatigue samples to generate statistically significant, pedigreed Ti-6Al-4V fatigue data from numerous stochastic flaws, enabling the project team to define the link between the process, the flaw characteristics, and fatigue performance. All manufacturing and test data will be collected and stored using the Data Management System for Additive Manufacturing (DMSAM) as the primary deliverable of the project. Additionally, a parallel effort will also be undertaken to develop improved understanding of the nature of flaw-formation mechanisms and the factors that lead to stochastic flaws.
"Evaluation of Defects in Metal LPBF AM Using Multiple Lasers"
-- The Ohio State University (OSU) Center for Design & Manufacturing Excellence (CDME)
Led by The OSU CDME, in collaboration with GE Additive and Proto Precision Manufacturing Solutions, this project will aim to understand the metallurgical defects in multiple laser powder bed fusion (LPBF) systems and apply non-destructive examination (NDE) methods in order to identify potential defects in service. Currently, parts that are uneconomical to produce with single-laser LPBF systems can be made cost effectively by the productivity improvement from multiple lasers. While many LPBF machine manufacturers are now offering commercially available equipment with two and four lasers, the industry lacks an understanding of the potential metallurgical defects arising from the use of multiple lasers. Moreover, an openly available library or design guidelines do not exist within the industry. This project will analyze the defects in printed nickel alloy 718 and deliver a test artifact, technical data package, and new standards as the foundation for end users to overcome the existing technical barriers and confidently implement new higher productivity metal AM equipment with multi-laser LPBF systems.
TOPIC AREA 3 - Emerging Process Technology for Low Criticality Part Families
"Demonstration of 3D Composite Based AM (CBAM) Build Process for Low Criticality Part Families"
-- Utah Advanced Materials and Manufacturing Initiative (UAMMI)
Led by the UAMMI, in collaboration with Impossible Objects (IO) and the Utah Composites Lab, this project will demonstrate and evaluate 3D composite-based AM (CBAM) capability as a viable option to generate non-critical, non-structural components that satisfactorily fulfill the required part function for the USAF and the sustainment community. Waiting on parts is a significant driver of maintenance down time in legacy systems and one that the Air Force Sustainment Center has worked to resolve the root causes, which include obsolescence, Diminishing Manufacturing Sources and Material Shortages (DMSMS), and never-before seen failures on parts not originally planned needing replacement. The goal of this project is to prove out and accelerate CBAM technology and to build a body of CBAM knowledge for todays non-critical part replacements and tomorrows implementations throughout the industry and other various DoD sustainment operations. CBAM will also be assessed in how it extends to part families of similar size, shape, criticality, and function.
"AM of Low Criticality Part Families via Continuous Liquid Interface Production"
-- United Technologies Research Center (UTRC)
Led by UTRC, in collaboration with Carbon, UTC Aerospace Systems, and Pratt and Whitney, this project will investigate the capability of Carbons emerging Continuous Liquid Interface Production (CLIP) process and supporting fabrication technologies to advance the Manufacturing Readiness Level (MRL) related to the AM of low-criticality polymer components for aerospace applications with a specific emphasis on masks, enclosures, and ducting. Shot peening masks, electrical enclosures, and ducting are low criticality parts with ubiquitous use in aerospace systems, and the development of additively manufactured surrogates will greatly enhance the ability to be agile to DoD supply chain requests. In addition to exploring the CLIP process in its capabilities to manufacture low criticality components, this project also aims to demonstrate a complete end-to-end digital additive workflow, which encompasses part digitalization, design optimization, print process optimization, materials characterization, and component performance validation.
"Rapid Part Replacement via Digital Light Processing"
-- University of Dayton Research Institute (UDRI)
Led by UDRI, in collaboration with 3D Systems, Lockheed Martin, Orbital ATK, and Northrop Grumman, this project will evaluate the ability of Digital Light Processing (DLP) technology, specifically the Figure 4™ machine being pioneered by 3DSystems, to supply the USAF low criticality components, including electrical connectors, knobs, elastomeric grommets, and spacers for legacy sustainment equipment. With DLP, a photopolymer is drawn out of a resin bath and rapidly cured by an underlying image projector. It cures the entire part slice at once as compared to other toolpath-based AM technologies and enables fine resolution, smooth surfaces, novel material chemistries, and the fast print speeds. This project will identify and overcome technological and materials science barriers associated with DLP through part-family-specific testing, characterization, and post-processing; demonstrate rapid part replacement; and establish a clear technology development, vetting, and USAF transition pathway for Figure 4 technology.
"From a technical perspective, the response to the Project Call was phenomenal in that the approaches outlined in the submitted proposals were very interesting and innovative, showing a solid understanding of the ideal outcomes that we were driving toward in each of the three topic areas," said John Wilczynski, America Makes Technology Director. "Going into this Project Call, we planned for multiple awards. Given the quality of the submissions, we would have liked to make more awards. For the seven award project teams, theres no doubt that the project results will not only transform the sustainment community, but will also have a far-reaching impact beyond, regardless of industry."
The anticipated start date of the projects is June 2018.
For more information on the Project Call or how to become an America Makes member, visit the America Makes Web site at http://americamakes.us and follow the Institute on Twitter @AmericaMakes. Visit America Makes at RAPID + TCT 2018 at booth #2439.
###
About America Makes
America Makes is the National Additive Manufacturing Innovation Institute. As the national accelerator for additive manufacturing (AM), America Makes is the nations leading and collaborative partner in AM and 3DP technology research, discovery, creation, and innovation. Structured as a public-private partnership with member organizations from industry, academia, government, non-government agencies, and workforce and economic development resources, we are working together to innovate and accelerate AM to increase our nations global manufacturing competitiveness. Based in Youngstown, Ohio, America Makes is the first Institute within the Manufacturing USA infrastructure and is driven by the National Center for Defense Manufacturing and Machining (NCDMM). For more information about America Makes, visit http://americamakes.us.
About NCDMM
NCDMM delivers innovative and collaborative manufacturing solutions that enhance our nations workforce and economic competitiveness. NCDMM has extensive knowledge and depth in manufacturing areas—both commercial and defense—to continually innovate, improve, and advance manufacturing technologies and methodologies. Our experienced team specializes in identifying the needs, the players, the technologies, and processes to attain optimal solutions for our customers. We connect the dots. Thats the NCDMM methodology. NCDMM also manages the national accelerator for additive manufacturing (AM) and 3D printing (3DP), America Makes—the National Additive Manufacturing Innovation Institute. For additional information, visit the NCDMM at http://ncdmm.org/.
Featured Product
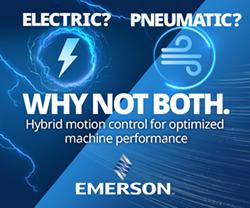