UM Dedicates Game-Changing 3D Lab
New College of Engineering-Johnson & Johnson 3D Printing Center of Excellence Collaborative Laboratory will be a hub for innovation and collaboration
CORAL GABLES, Fla., Oct. 26, 2017 /PRNewswire-USNewswire/ -- Andres Ruiz had always chalked it up as just part of the game. Broken bones, torn ligaments and other injuries, he knew, occur in every high-impact sport, and baseball was no exception. But when a fractured hip sidelined him from the sport he was passionate about since he was 5, Ruiz made a decision to become a biomedical engineer, choosing the field because of its ability to mitigate injury and disease.
Today, as a senior majoring in biomedical engineering at the University of Miami, Ruiz is excited about a new UM-based lab that has the potential to help revolutionize not only his discipline but other areas of engineering as well.
Dedicated on Monday, Oct. 23, the new UM College of Engineering-Johnson & Johnson 3D Printing Center of Excellence Collaborative Laboratory will support joint research, materials development, and testing of 3D printing technologies and processes.
UM faculty and students will have access to the lab's state-of-the-art three-dimensional printing—or additive manufacturing—equipment, which is housed in a 5,850-square-foot "collaborative laboratory" inside the McArthur Engineering building and includes ten 3D MakerBots that use polymers to create objects, and two 3D metal printers—one that uses titanium powder and the other, stainless steel. Students will work alongside J&J engineers and scientists, gaining invaluable experience.
Jean-Pierre Bardet, dean of UM's College of Engineering, called the new facility a "collaboratory."
"An engineering education has to give students the chance for hands-on creativity and allow their imaginations to soar," he said at Monday's ribbon-cutting. "Thanks to Johnson & Johnson, we have yet another resource to educate tomorrow's technology leaders."
UM President Julio Frenk welcomed the lab as "a hub for innovation" that will foster "constructive change."
Indeed, 3D printing—the process of making three-dimensional objects by adding materials such as plastics or metals in successive layers—has been hailed as a game changer for everything from the medical to automotive and aerospace industries. But 3D printing is not new. The technology has been around for more than 30 years, Joseph Sendra, worldwide vice president of manufacturing engineering and technology at Johnson & Johnson, noted during the dedication ceremony.
"What's different today is the cyber-physical interconnectivity between man and machine. It's the digital coming together with what's real," said Sendra, who graduated from UM's College of Engineering with a degree in industrial engineering in 1993 and is one of three UM alumni who helped bring the new Collaborative Laboratory to UM.
Featured Product
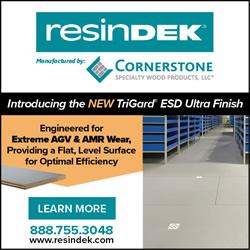