Cooperation between SICK and Silicon Software implements VisualApplets in extending application versatility from the SICK AppSpace
SICK AG, manufacturer of sensors and application solutions, and Silicon Software GmbH, manufacturer of frame grabbers and the award winning graphical FPGA development environment VisualApplets, have entered into a partnership to ensure that image processing devices meet current and future market demands for high data throughput, low latency and real-time processing.
Intelligent cameras and sensors integrated into an image processing system place high demands on their flexible use in automation, industry 4.0 as well as in non-industrial environments. SICK AG, manufacturer of sensors and application solutions, and Silicon Software GmbH, manufacturer of frame grabbers and the award winning graphical FPGA development environment VisualApplets, have entered into a partnership to ensure that image processing devices meet current and future market demands for high data throughput, low latency and real-time processing. With VisualApplets providing SICK with a wide range of new possibilities for application solutions, SICK's customer requirements can be adapted to their systems for a wider gamut of image processing applications.
In order to equip the SICK devices with even greater intelligence and minimal programming effort, FPGA programming is significantly simplified by the collaboration of the two companies for use in a variety of new image processing applications in demanding industrial environments. In addition to its own FPGA algorithms, SICK now uses Silicon Softwares VisualApplets to graphically program tailor-made algorithms and applications, for image processing and signal processing directly in the device, which reduces the data load in the CPU and accelerates image processing results.
The programmable cameras, sensors and SIM 4000 (Sensor Integration Machine) of the SICK AppSpace Ecosystem can be further enhanced with VisualApplets. With over 200 graphical operators, users of the SICK products can easily, quickly and flexibly create complex drag-and-drop FPGA algorithms and applications for one product series and easily port them to other product series. Users retain full control over the FPGA resources and function of their VisualApplets applications. Compared to complex HDL programming, VisualApplets‘ graphical programming is accomplished via drag and drop data flow models providing an FPGA development speed increase from 10X to 100X faster than traditional FPGA development. This graphical design process now makes FPGA development accessible to both software developers and application engineers without any FPGA development experience.
Implement Once - Reprogram Forever
In order to enable SICK sensors and image processing devices that are FGPA or SoC based to be programmable with VisualApplets, SICK has created a dynamic IP core (known as an eVA Core) inside their devices FPGA using the VisualApplets Embedder Extension. The SICK device‘s eVA Core can now be re-programmed as often as desired to provide real-time image processing functionalities. The users design can be transferred in a few steps to different hardware designs of other devices. The eVA Core integration process essentially requires the definition of the interfaces for the eVA Core and their integration into the FPGAs overall design.
SICK has prepared its hardware platforms, such as cameras, sensors and the SIM 4000, for VisualApplets programming using the VisualApplets Embedder to create customer-specific image processing applications. The opening of the SICK platforms allows users to optimize their performance by programming their own FPGA-based developments as well as achieving a faster time-to-market of their products and a simpler expansion of the product families. This allows SICK to react more quickly to individual product variations and market changes and to reduce system costs in the projects. With the VisualApplets Expert Extension, SICK users are able to use their existing HDL code libraries in VisualApplets as custom operators. Following the GUI-driven integration process, custom operators work like native VisualApplets operators and take advantage of the VisualApplets workflow, the high-level simulation, the resource estimation and the bandwidth calculations.
"SICK sensors and cameras are being developed to tailor solutions to specific customer requirements, which can be used in adaptive sensor networks for all industries. New applications and markets can be addressed more quickly. Application developers from various industries benefit greatly from the ease of use of VisualApplets", said Detlef Deuil, Head of Product Management for Vertical Integration Products at SICK. The company is also using the extended possibilities of sensor programming internally for its own application development.
"With the flexible programming of SICK image processing devices, we have successfully implemented our vision... the implementation of VisualApplets, our award winning graphical FPGA development environment, in any embedded FPGA hardware platform and SoC. These systems provide the performance of large system solutions that can be repeatedly and flexibly re-configured with new applications", affirms Dr. Klaus-Henning Noffz, CEO of Silicon Software.
Featured Product
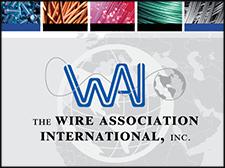