SENIS helps keep permanent magnets at optimum performance
Swiss company SENIS will showcase its innovative magnetic field mapping system for permanent magnet inspection at CWIEME Chicago 2017.
With demand for electricity at its highest in human history, the need for reliable, high-performance magnets is greater than ever. Nowadays, permanent magnets are used in a wide variety of applications, such as sensors and actuators. To achieve optimal performance in their application, the characteristics of permanent magnets must be carefully monitored and controlled.
SENIS AG, based in Switzerland, has developed a novel measurement system that allows for quality control of permanent magnets by combining highly accurate magnetic field mapping and crack detection.
The SENIS Magnetic Field Mapper, or MMS-1A-RS, is a high-end magnetic field scanner that can be applied for mapping of all three components of DC or AC magnetic field. It can be used as a quality assessment tool in production lines for accurate 3D mapping of permanent magnets.
Sasa Spasic, CEO of SENIS, will speak about the benefits of the system at the upcoming CWIEME Chicago exhibition, taking place at the Donald E. Stephens Convention Center in Rosemont, Il between 3-5 October.
3D magnetic field mapper
"Our product is regarded as the best product on the market because we integrate a 3D - or three-axis Hall probe - device, which measures magnetic field performance with pinpoint accuracy," says Spasic. "Our ultrathin Hall probe is positioned very close to the rotor, and measures the magnetic fields at different positions or different points around the rotor. This gives us a ‘map of the magnetic field, allowing the developers or producers to see if the rotor is magnetised correctly. If the rotor is at optimum performance then it can be integrated into the application."
According to Spasic, the dangers of not conducting these tests increases the chances of devices performing badly at the final quality control. "When it gets to this stage, it is too late to do anything; the magnets have already been implemented into the machine," he says.
Magnetic field mapping is becoming increasingly popular in the electric vehicle industry. Customers are becoming more aware of magnetic performance and want their devices to be at optimum performance.
Since 2004, SENIS has developed, manufactured and supplied advanced instruments for magnetic field measurement and electric current measurement, as well as provided the corresponding development and engineering services.
"The demand has increased very rapidly over the last few years," Spasic continues. "At SENIS, we offer a testing service where customers send us their magnets and we conduct the tests and provide them with the reports. But mostly, customers buy our products outright and perform the testing themselves, installing it close to the production line. Often, those that use our service end up buying the product after they see the benefits.
"Customers like our product for two reasons; the first reason is that it can measure with unprecedented accuracy and repeatability very close to the magnet surface and in small gaps. The second reason is that our mapper software is very user-friendly and offers different types of analysis, with different types of data visualisation."
A versatile product
The SENIS Magnetic Field Mapper doesnt just provide magnetic field mapping, however. SENIS provides another type of probe that detects cracks in the magnets, known as eddy-current probes.
"Magnets, like all metals, are susceptible to cracking," says Spasic. "When a crack forms in a magnet, they are usually too small to see with the naked eye."
Eddy-current probes can root out microscopic cracks in conducting materials. Parts can be tested either before or after magnetisation.
"If a magnet breaks once the device is assembled then you have to replace the entire device; this is usually very expensive. Some of our customers say that material crack inspection is a ‘must for their products", Spasic continues. "We also offer a touch stylus that measures the dimensions of the device to ensure product consistency and quality assurance."
CWIEME Chicago 2017
Sasa Spasic will be speaking about the benefits of magnetic field mapping at the upcoming CWIEME Chicago exhibition, taking place in October. There he will highlight the high accuracy and high magnetic field resolution of SENISs 3D magnetic field mapping system. He will also focus on the replaceability and variety of the measuring probes, as well as the accessibility of the mapper software.
"We have been coming to CWIEME events for many years now; its a great place to meet with other companies in the electromotor industry. Im very looking forward to speaking in Chicago; Im confident others in the industry will find it valuable."
Spasics seminar will take place on 4th October between 11:20 and 12:00 local time in the CWIEME Connect Theatre. SENIS, along with its US representative GMW Associates, will also be exhibiting at the event, allowing visitors to come and see the SENIS Magnetic Field Mapper in action. SENIS will be at booth G44.
Featured Product
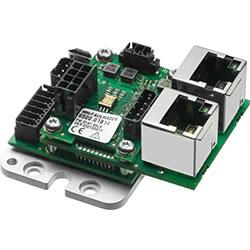
MOTION CONTROLLERS FOR MINIATURE DRIVES AND MICRODRIVES
FAULHABER has added another extremely compact Motion Controller without housing to its product range. The new Motion Controller is ideal for integration in equipment manufacturing and medical technology applications. With 36 V and 3 A (peak current 9 A), it covers the power range up to approx. 100 W and is suitable for DC-motors with encoder, brushless drives or linear motors.