SABIC Launches New THERMOCOMP™ AM Materials for Large Format Additive Manufacturing at RAPID + TCT
SABIC Launches New THERMOCOMP™ AM Materials for Large Format Additive Manufacturing at RAPID + TCT
SABIC, a global leader in thermoplastic technology, introduced here today at RAPID + TCT 2017, a new family of high-performance THERMOCOMP™ AM compounds that addresses the unique requirements of large format additive manufacturing (LFAM). Print parameters and mechanical properties for the materials -developed by SABIC using test specimens printed on the companys in-house big area additive manufacturing (BAAM®) machine - can significantly aid customers in expediting material selection and optimizing processing conditions. Reinforced with carbon or glass fibers for added strength, the new compounds can be used for applications in the tooling, aerospace, automotive and defense industries.
"Delivering leading-edge solutions for large format additive manufacturing is an important part of our overall strategy to drive this technologys growth," said Lori Louthan, director, Mass Transportation, SABIC. "Beyond our material development expertise, SABIC has the resources to integrate processing, design and testing capabilities at our Center of Excellence for Additive Manufacturing, allowing us to help customers accelerate their application development for large printed parts."
New THERMOCOMP™ AM Compounds Introduced for Use in Large Format Equipment
SABICs first eight reinforced THERMOCOMP™ AM compounds for large format additive manufacturing are based on four of the companys amorphous resins: acrylonitrile-butadiene-styrene (ABS), polyphenylene ether (PPE), polycarbonate (PC) and polyetherimide (PEI). These resins exhibit good creep behavior versus semi-crystalline resins, and reduced deformation under constant pressure. Further, lower shrinkage during cooling means these materials demonstrate greater dimensional stability and less thermal expansion during part use.
• ABS-based compounds provide easy processing, low warpage and good print surface quality, making them good candidate materials for a broad range of applications and tooling, including thermoforming and vacuum forming.
• PPE-based compounds offer lower thermal expansion, outstanding hydrolytic stability, a higher strength-to-weight ratio and higher temperature performance compared to ABS.
• PC-based compounds deliver higher stiffness, higher temperature performance and higher throughput compared to ABS and PPE, as well as excellent ductility and a smooth surface finish.
• PEI-based compounds, developed from SABICs inherently flame-retardant ULTEM™ resins, provide low thermal expansion, high temperature performance, an excellent strength-to-weight ratio, high modulus and low creep.
Each of the THERMOCOMP™ AM materials is reinforced with carbon or glass fiber, depending on the degree of stiffness and dimensional stability required.
An Expanding Materials Portfolio Enabling Growth for Large Format Additive Manufacturing
"With access to more than 25 thermoplastic resins and a wide range of fillers and reinforcements, SABIC plans to expand the THERMOCOMP™ AM portfolio to address our customers application requirements as the adoption of this printing technology continues to grow," noted Amanda Roble, director, Specialties Business, SABIC. "For example, we are currently developing new compounds based on semi-crystalline resins such as PBT, PA, PPS and PEEK to address the printing industrys needs for large format materials with improved chemical resistance and stiffness."
SABIC is also showcasing at RAPID + TCT 2017 in booth #2537, a section of a boat hull from Livrea Yacht that was printed on SABICs BAAM machine. The hull is a result of a collaborative design effort between SABIC, Livrea Yacht and 3D design and engineering software provider, Autodesk. Using Autodesk® Fusion 360® design software and SABICs processing expertise on the BAAM, the three companies selected two materials from the THERMOCOMP™ AM portfolio: a carbon fiber reinforced PPE compound for the hulls outer layer, and a carbon fiber reinforced PEI for the inner lattice support structure.
"The process of using large-format additive manufacturing enabled Livrea Yacht to eliminate the need for molds and prototyping, which can be costly and inefficient," said Mike Geyer, director of Evangelism and Emerging Technology at Autodesk "The 3D printed hull is lighter and stronger, and can be manufactured at a fraction of the cost and in half the time, giving Livrea Yacht a competitive breakthrough that would not be possible with traditional fabrication. We are entering a very exciting time for complex, high-speed additive manufacturing."
For additional information, please visit www.sabic.com.
Featured Product
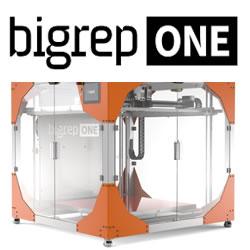