New Mentor FloTHERM XT release simulates complex geometries with ease, speed and accuracy
Key capabilities in this new FloTHERM XT release include simulation of spinning parts in electronic enclosures; temperature-dependent power simulation; enhanced "Design of Experiments" parametric studies functionality to determine best design coverage; and thermal territory simulation when using various component materials. These features are important for electronics devices used in the transportation, aerospace, defense, and consumer electronics markets.
WILSONVILLE, Ore., May 2, 2017 — (PRNewswire) — Mentor, a Siemens business, today announced the latest release of the FloTHERM® XT electronics cooling software product with advanced thermal management capabilities. Based on the electronics cooling DNA of the Mentor market-leading FloTHERM technology and the FloEFD™ CAD-centric philosophy, the award-winning FloTHERM XT product is the industry's first integrated mechanical design automation (MDA) and electronic design automation (EDA) electronics cooling solution. This latest version of the FloTHERM XT product offers new functionalities developed from customer feedback to effectively simulate thermal effects of complex geometries.
Key capabilities in this new FloTHERM XT release include simulation of spinning parts in electronic enclosures; temperature-dependent power simulation; enhanced "Design of Experiments" parametric studies functionality to determine best design coverage; and thermal territory simulation when using various component materials. These features are important for electronics devices used in the transportation, aerospace, defense, and consumer electronics markets.
"When we switched to FloTHERM XT from our previous CFD tool, we cut our analysis time in half. Even with increasingly accelerated development schedules, we have time to perform trade-off studies to optimize the thermal design," said Tim Fleury, manager of thermal analysis and environmental test, Mercury Systems, Inc. "The CAD import and adaptive meshing combination feature in this new FloTHERM XT release is paramount."
The FloTHERM XT product can be used at all stages of the electronic design process, from design concept through manufacturing. Its CAD-centric technology and robust mesher simulates complex geometries with ease, speed, and accuracy for improved product quality and reliability.
Key Features in the FloTHERM XT Release:
Thermal specialists and design engineers can take advantage of key features of the latest release of FloTHERM XT:
Explicit Models for Spinning Parts: The new sliding mesh capability easily meshes the rotation region to accurately simulate the effects of spinning parts such as fans and rotors used in electronics enclosures.
Temperature-Dependent Power Simulation: When attached to an object or planar source, the FloTHERM XT software will use the object's own average temperature goal to adjust the applied power. This feature was developed from customer feedback.
Thermal Territory Simulation: This new feature is critical for detailed copper "under the component" designs, used to draw heat away from that component - proving an accurate simulation methodology.
Enhanced Parametric Study Functionality: The addition of a "Design of Experiments" scenario table allows users to set up a number of studies to ensure the best coverage of the design field. These scenarios can also be sent to remote machines with more capacity. The addition of this key enhancement was based on customer feedback.
Improved User Interface: Enhancements to the user interface make it easier to set model parameters and find mesh controls for improved thermal design predictability.
Design Tool Integration: Two approaches are available for tool interoperability in this release. Files can be directly imported through the FloEDA Bridge module with ease-of-use features such as undo/redo, access to power displayed in tree, and the graphical representation of component types. The second approach uses a neutral file format allowing the user to interact with the setup of a model outside of the standard interface.
"The latest release of FloTHERM XT is based on listening to our customers and delivering the optimum thermal simulation solution to address their thermal design challenges," stated Roland Feldhinkel, general manager of the Mentor Mechanical Analysis Division. "Our continued investment in FloTHERM XT will allow our customers to verify and prototype their designs with greater ease and confidence. These new features are vital for electronics systems designers who are creating innovative, high-performance products for the transportation, mil-aero and automotive industries."
The new FloTHERM XT product with standard functionality is now shipping. The FloTHERM XT Ultra option, with advanced capabilities such as transient analysis, and the FloTHERM FLEXX for users with an existing FloTHERM or FloTHERM XT license are also available today. For more information, visit the product website: http://www.mentor.com/products/mechanical/flotherm/flotherm-xt/
Contact for journalists
Larry Toda
Phone: 503-685-1664; E-mail: Email Contact
Mentor Graphics Corporation, a Siemens business, is a world leader in electronic hardware and software design solutions, providing products, consulting services, and award-winning support for the world's most successful electronic, semiconductor, and systems companies. Corporate headquarters are located at 8005 S.W. Boeckman Road, Wilsonville, Oregon 97070-7777. Web site: http://www.mentor.com.
Mentor Graphics and FloTHERM are registered trademarks and FloEFD is a trademark of Mentor Graphics Corporation. All other company or product names are the registered trademarks or trademarks of their respective owners
Featured Product
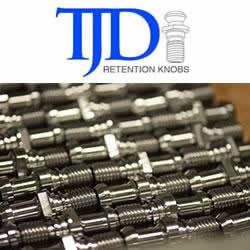