Bosch presents solutions for cup filling at interpack 2017 For enhanced product safety, flexibility and efficiency
• Hygienically designed solutions for improved product safety • From low- to high-speed filling in different hygienic levels to match production needs • Solutions for change-over and cup format flexibility
Düsseldorf, Germany - Bosch Packaging Technology will showcase its latest developments at interpack 2017 for producers of dairy products and other pumpable food looking for improved product safety and efficient production. Two solutions will be on display: the Osgood rotary filling and sealing machine for pre-made cups and the latest Ampack FCL aseptic linear filling and sealing machine for pre-made cups. With over 50 years of experience in clean, ultra-clean and aseptic filling technologies, Bosch developed these new solutions to address the key market requirements for dairy producers, such as hygienic operation, from low to high output, compact spaces, and ease of use.
Filling the world with confidence
At interpack, Bosch will debut Ampacks new FCL 3080 A aseptic linear filling and sealing machine for dairy, baby food and clinical nutrition, which enhances product safety. It features a smaller aseptic chamber, which improves product control, thus minimizing the risk of food contamination. Additionally, the machine chain is kept outside of the aseptic chamber, limiting bacterial build-up and maintenance needs. In terms of flexibility, the eight-lane linear filler handles two different cup formats - ranging from 75 to 95 millimeter in diameter - at speeds of up to 20,000 cups per hour. The machine fills a broad range of products with particles up to 22 millimeter in diameter. Offering two different hygienic executions (ultra-clean or aseptic), it is an ideal solution for products requiring a longer shelf life outside the cooling chain - from 4 to 6 weeks or up to 12 months, the highest level available on the market.
For increased output, the machine is equipped with a new drive-concept increasing the filling speed. The improved product transport system and optional anti-spilling functionality lead to an extended lifetime of components by preventing contamination and shortening cleaning time. Low energy consumption and reduced maintenance costs further enhance production efficiency. An additional benefit of short delivery times stems from its modular and standardized design including the new HMI 4.0, a true gateway to the connected factory.
Alternative hygienic execution for compact spaces
For dairy and other food applications (including hummus or potato salads), Bosch presents an upgraded version of its existing Osgood rotary series. Handling smaller cups at speeds of up to 9,600 products an hour on four lanes, it is a good alternative for producers with limited space with regards to their production capacity. Available in both clean and ultra-clean execution, the machine can fill a range of different pack styles depending on the final application - for example, round and square cups with trays, seals with pre-die cut foils or roll stock film. The rotary filler is also equipped with a new harmonized pump design, developed by experts from Boschs food business unit, which provides higher filling accuracy and easier interchangeability between different machines.
The rotary filler ensures easier and faster changeovers (in less than 15 minutes) thanks to new servo motors, enabling quick and easy adjustments to the set-up. Finally, the Osgood machine is equipped with the latest HMI 4.0, which automatically leads operators through each of the production steps for easy operation. The Osgood rotary filler can be equipped with three different machine controls (Bosch Rexroth, Rockwell or Siemens), allowing customers an easy integration of the machine in their existing production lines.
To learn more about dairy and cup filling solutions, visit Bosch at interpack in Düsseldorf, Germany, from May 4th to 10th, 2017, Hall 6, C58. Click here to learn more about our booth at interpack 2017.
Based in Waiblingen near Stuttgart, Germany, and employing 6,200 associates, the Bosch Packaging Technology division is one of the leading suppliers of process and packaging technology. At over 30 locations in more than 15 countries worldwide, a highly-qualified workforce develops and produces complete solutions for the pharmaceuticals, food, and confectionery industries. These solutions are complemented by a comprehensive after-sales service portfolio. A global service and sales network provides customers with local points of contact. Additional information is available online at www.boschpackaging.com
The Bosch Group is a leading global supplier of technology and services. It employs roughly 375,000 associates worldwide (as of December 31, 2015). The company generated sales of 70.6 billion euros in 2015. Its operations are divided into four business sectors: Mobility Solutions, Industrial Technology, Consumer Goods, and Energy and Building Technology. The Bosch Group comprises Robert Bosch GmbH and its roughly 440 subsidiaries and regional companies in some 60 countries. Including sales and service partners, Boschs global manufacturing and sales network covers some 150 countries. The basis for the companys future growth is its innovative strength. Bosch employs 55,800 associates in research and development at 118 locations across the globe. The Bosch Groups strategic objective is to deliver innovations for a connected life. Bosch improves quality of life worldwide with products and services that are innovative and spark enthusiasm. In short, Bosch creates technology that is "Invented for life."
Additional information is available online at www.bosch.com, www.bosch-press.com, twitter.com/BoschPresse.
Featured Product
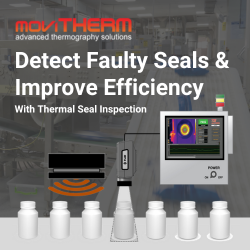