Makino Reveals New a120nx Horizontal Machining Center Built for Large, Heavy Part Production
Largest nx-series machining platform to date delivers speed and accuracy to massive part sizes
MASON, Ohio - January 5, 2016 - Makino announces its newest addition to the nx-series, the a120nx horizontal machining center. As the largest machining platform within the nx-series to date, this machine is built to take on oversized structural components for industrial equipment, diesel engines and semiconductor manufacturing, while delivering high levels of speed and accuracy.
"You cant approach big parts the same way you would any other part, and thats why everything about the a120nx is sized for heavy-duty manufacturing," said John Einberger, product line manager at Makino. "We wanted to employ the proven designs of our other nx-series machines, such as three-point leveling and tiered column design, while ensuring that the machine could mechanically handle the unique challenges of large workpiece machining processes."
The a120nx features vast X-, Y- and Z-axis travels of 74.8 inches, 63 inches and 66.9 inches (1,900 mm, 1,600 mm and 1,700 mm, respectively), and the machines standard large pallet size of 39.4 inches by 39.4 inches provides capacity for parts weighing up to 11,000 pounds. The machines automatic pallet changer switches from one pallet to the next in 38 seconds, minimizing non-cut times for the highest levels of productivity. Capable of storing up to 204 tools of wide-ranging sizes and designs, the a120nx accommodates tools up to 35.4 inches long, 14.0 inches in diameter, and weighing up to 77 pounds. Tools are loaded into the automatic tool changer (ATC) from an easily accessible, ergonomically friendly exterior loading station to prevent operator fatigue.
Built for Rigidity During Continuous Production
At the foundation of the machine is a three-point supported bed casting to ensure all points are stable and contacting the floor. Developed to maintain the machine geometry and alignments, this design characteristic of the nx-series machines simplifies installation and enables easy relocation of the machine. Building on the rigidity of the bed casting, the a120nx uses a unique tiered column design that delivers greater resistance to Z-axis cutting forces throughout the work envelope. Robust cross roller-style B-axis table bearings work in concert with a high force rotary clamping system to ensure stable cutting throughout the machines expansive work zone.
The a120nx is equipped with Makinos four cone pallet location and clamping system that delivers a secure 46,500 pounds of force on the pallet. This superior clamping capability, combined with all pallets built to a master pallet, eliminates deflection. An engineered precision air-blow system provides locating surfaces cleaning, as well as pallet clamp confirmation as standard features.
Larger parts typically mean larger features, too. Tool length, diameter and weight capacities of the a120nx support processes that feature the use of large face mills, boring bars and line-bar tooling.
To further ensure ideal geometry and accuracy, the a120nx has a number of systems in place to manage the heat generated by rapid traverse of 2,126 inches per minute. For one, the ballscrews are core-cooled in all axes to give consistent accuracy during continuous production. Moreover, the ballscrews are all dual supported and pre-tensioned to ensure unparalleled dynamic positioning repeatability. Feature-to-feature movement distances on large parts are typically much greater, so rapid traverse rates were increased for the a120nx in order to cover these expansive distances quickly.
Powerful Spindle, Pallet Clamping for Speed and Accuracy
Beyond its proven speed and accuracy, the a120nx also improves productivity in cutting and non-cutting performance. The standard high torque 8,000-rpm spindle boosts continuous power levels by 19 percent over levels typical to machines of this class. With 50 continuous (74 peak) horsepower available, this spindle is ideally suited for heavy roughing of iron castings and hard-metal applications. In addition, the spindle features significant improvements in acceleration and deceleration due to its high duty rated performance characteristics that reduce rigid tapping times by up to 30 percent. Also available is an optional 18,000-rpm high power spindle, ideally suited to high metal removal rate machining of light alloy structural components.
Chip and coolant management features are often overlooked and result in interrupted operations, increased labor costs, machine damage, part-quality issues and reduced tool life. The a120nx enables shop owners to avoid these challenges with supplementary management features, including a sloped surface to remove obstacles between the workpiece and an external chip conveyor, letting chips fall freely. The trough design facilitates rapid chip and coolant evacuation and reduces maintenance needs with a solid panel Z-axis cover design. A standard cyclonic filter provides ultra clean coolant to the through spindle coolant pump and acts as a secondary coolant filter, polishing coolant in the main tank.
The a120nx comes to the market ‘automation ready, being fully compatible with Makinos versitile multi-machine, multi-pallet MMC2 flexible manufacturing system, complete with Makinos highly capable MAS-A5 cell controller.
Machining massive parts poses multiple challenges. However, speed, accuracy and durability remain crucial when working with large parts and meeting customers delivery demands. To learn more about Makinos a120nx horizontal machining center, visit https://www.makino.com/horizontal-machining-4-axis/a120nx/.
About Makino
A world leader in advanced CNC machining centers, Makino is committed to providing high-performance, leading-edge machining technologies and innovative engineered process solutions that enable manufacturers to focus on making what matters. Makino offers a wide range of high-precision metal-cutting and EDM machinery, including horizontal machining centers, vertical machining centers, 5-axis machining centers, graphite machining centers, and wire and sinker EDMs.
Makinos flexible automation solutions provide reduced labor costs and increased throughput in a variety of production volumes and designs. Makinos engineering services offers industry-leading expertise for even the most challenging applications across all industries. For more information, call 1-800-552-3288 or visit makino.com.
Featured Product
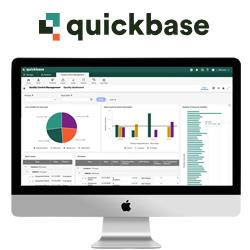
Quickbase: The first application platform built for dynamic work
By connecting everything through a single source of truth, the Quickbase platform helps businesses mitigate risk, reduce waste, and cut down on unexpected costs. With automated workflows and granular permissions, the right people will have access to the right information.