Dorner Introduces Next Generation 2200 Series Modular Belt Conveyors
Dorner's newly redesigned 2200 Series Modular Belt Conveyor features additional belt options, a sleek open frame design, a universal T-slot and is ideal for applications within the metalworking, packaging, assembling and general manufacturing industries.
HARTLAND, Wis., (September 12, 2016) -Dorner's newly redesigned 2200 Series Modular Belt Conveyor features additional belt options, a sleek open frame design, a universal T-slot and is ideal for applications within the metalworking, packaging, assembling and general manufacturing industries.
The product redesign includes a number of improvements. For starters, its ladder-style, open frame design replaces traditional perforated bedplates that allows better airflow through the frame for cooling and water, and chemical drainage applications. Its sleek, narrow profile means it can be positioned under machinery and in other tight spaces where other conveyors wouldn't fit. Another enhancement to the frame is a Universal T-slot that is compatible with industry standard hardware and makes attaching accessories and guiding fast and simple.
The optional high speed nose bar transfer option allows for safe and efficient transfers of small parts at speeds up to 175 feet per minute. The conveyor also comes with two styles of plastic chain belting: micro pitch, general purpose modular belt, or a metalworking modular belt (1" or 2"
cleats are available on the metalworking modular belt). End drive models are compatible with Dorner's new Universal Drive - a universal motor and mounting package that covers all speeds, loads and mounting positions with a single part number.
The 2200 Series Modular Belt is the third of four new platforms being introduced this year as part of Dorner's newly redesigned 2200 Series platform. In April, Dorner re-launched the original 2200 Series to include new features such as a redesigned frame, additional belting and expanded guiding to make the platform stronger, faster and more flexible for handling small to medium size part applications. The 2200 Series LPZ, which comes with one or two pivot points, launched in June as the second conveyor in the newly redesigned series. The fourth and final conveyor in the series is expected to debut later this year.
Features and benefits of the new 2200 Series Modular Belt conveyor include:
. Three available drive options: End Drive, Center Drive, or Dorner's
iDrive, consolidated motor and control offering
. Widths between 3" and 24"; lengths between 18" to 30'
. Load up to 150 pounds and speeds up to 250 feet per minute
. Micro pitch belt option
o Drive with 17 tooth, 1.7" pitch diameter
o 1.125" diameter standard idler
o 0.31" nose bar transfer
. Metalworking belt option
o Drive with 10 toot, 1.88" diameter
o 1.125" diameter standard idler
. 10 year warranty
. Ships in 5 business days
All of Dorner's 2200 Series conveyors can be configured in Dorner's Online Configurator, DTools. Users can engineer a complete conveyor and download a complete 3D CAD assembly model for instant validation of fit.
For more information on Dorner's new 2200 Series Modular Belt conveyor, visit www.dornerconveyors.com.
Connect with Dorner on Facebook at www.facebook.com/dornerconveyors Follow Dorner on Twitter at www.twitter.com/dornerconveyors Subscribe to Dorner on YouTube at https://www.youtube.com/user/DornerConveyors
Follow Dorner on LinkedIn at www.linkedin.com/company/dorner-mfg-corp
###
Hartland, Wisconsin-based Dorner Manufacturing is a world leader in the design, manufacture and distribution of high-quality conveyors and related equipment. Since 1966, companies from around the world have turned to Dorner conveyors for greatly improved efficiency and productivity. For more information about products or company news, visit Dorner's Web site at www.dornerconveyors.com or call 1-800-397-8664.
Featured Product
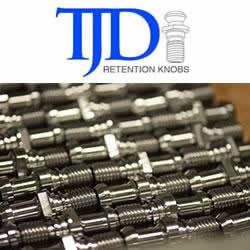
T.J. Davies' Retention Knobs
Our retention knobs are manufactured above international standards or to machine builder specifications. Retention knobs are manufactured utilizing AMS-6274/AISI-8620 alloy steel drawn in the United States. Threads are single-pointed on our lathes while manufacturing all other retention knob features to ensure high concentricity. Our process ensures that our threads are balanced (lead in/lead out at 180 degrees.) Each retention knob is carburized (hardened) to 58-62HRC, and case depth is .020-.030. Core hardness 40HRC. Each retention knob is coated utilizing a hot black oxide coating to military specifications. Our retention knobs are 100% covered in black oxide to prevent rust. All retention knob surfaces (not just mating surfaces) have a precision finish of 32 RMA micro or better: ISO grade 6N. Each retention knob is magnetic particle tested and tested at 2.5 times the pulling force of the drawbar. Certifications are maintained for each step in the manufacturing process for traceability.