Oberg Industries partners with Pitt's Swanson School of Engineering to advance additive manufacturing problem-solving for industry
To solve some of industry's most difficult additive manufacturing problems, Oberg Industries and the University of Pittsburgh's Swanson School of Engineering have partnered to combine Oberg expertise in manufacturing complex tooling and precision machined or stamped metal components with Pitt's ANSYS Additive Manufacturing Research La
PITTSBURGH, Sept. 8, 2016 /PRNewswire/ -- As additive manufacturing, or 3D printing, continues to advance in industry and academia, knowledge gaps can appear as researchers push the technology to new limits. To solve some of industry's most difficult additive manufacturing problems, Oberg Industries and the University of Pittsburgh's Swanson School of Engineering have partnered to combine Oberg expertise in manufacturing complex tooling and precision machined or stamped metal components with Pitt's ANSYS Additive Manufacturing Research Laboratory (AMRL).
Through the partnership with the Swanson School, for the next two years Oberg will have full-time employees on site to manage technical excellence at the ANSYS AMRL. Dedicated in June 2016 at the Swanson School, the ANSYS AMRL is an additive manufacturing lab equipped with some of the most advanced additive manufacturing devices that utilize metals, alloys, polymers and other materials to print components for nearly every industry. Oberg will promote the partnership to its customer partners to broaden corporate activity at Pitt while maintaining priority industrial access for its education, training, prototyping, testing, design, and production uses.
"This collaboration will link Pitt researchers in engineering, especially biomedical and aerospace, with Oberg's remarkable fabrication expertise in medical, aerospace, energy, and industrial production," said Mark Redfern, Pitt's Vice Provost for Research. "We look forward to wider engagement of faculty experts and students through the collaboration and with Oberg."
The partnership will also support faculty and students conducting collaborative research with Oberg and other industry partners. According to Redfern, lab workers including faculty, students and corporate users will benefit from the consistent facility management and technical expertise provided by Oberg. Pitt and Oberg will regularly interact to pursue student recruitment and employment, as well as joint educational, scholarship, and sponsorship opportunities.
Oberg and Pitt's collaborative work in this area was initiated with funding from the federal government via America Makes (the National Additive Manufacturing Innovation Institute). Pitt's research includes the development and testing of new tools to optimize the design and construction of manufactured parts to improve strength, lower weight, reduce overall costs, and improve sustainability of production.
"The industry is rapidly changing as the technology advances, and customers are increasingly viewing Oberg as a partner to capture the advantages," said David L. Bonvenuto, President and CEO of Oberg. "Through this partnership we're connecting our customers to Pitt's expertise in additive manufacturing and a state-of-the-art additive research facility. Together we ask better questions, we discover and learn more, which ultimately advances Oberg's value to its customers in this new era of additive manufacturing."
"The ANSYS AMRL is strengthened by this partnership with Oberg," noted Albert To, associate professor of mechanical engineering and materials science and one of Pitt's AM researchers. "The value we gain from Oberg who will manage the machines, help students advance their skills, and interact with industry to advance this technology, is phenomenal."
Since 2014, additive manufacturing researchers at the Swanson School have attracted more than $6 million in grants from America Makes, the National Energy Technology Laboratory, the National Science Foundation, and Research for Advanced Manufacturing in Pennsylvania.
Featured Product
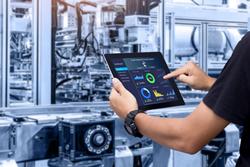