Choosing the Right Manufacturing Technology for Your Product
There is a wide access to manufacturing technologies today for people looking to bring their innovative product idea to the market.
There is a wide access to manufacturing technologies today for people looking to bring their innovative product idea to the market. Right from CNC machining, molding, casting, machining to additive manufacturing, innovator can choose from variety of manufacturing options. But does this diversity present an opportunity for greater flexibility or paralyzes the innovator to choose from too many options? How exactly should entrepreneurs choose the manufacturing technology to ensure that his idea would not turn into a costly failure? While there isnt any straightforward answer to this, there are factors that can help the innovator to choose the manufacturing technique that meets the design needs.
Here are some of the critical factors that should be considered while selecting the right manufacturing technology for your product.
Geometry, Materials, Development Time and Cost, best addresses the needs of your design
Cost always matters when comparing manufacturing methods, but this comparison can be often misleading. The cheapest method might not be the best, and it might not be even suitable for your project. Moreover, determining cost isnt always easy. There are different methods to determine the actual cost. The use of injection molding for simple parts like bracket or a hinge might be cheaper as compared to additive manufacturing for high volume manufacturing. But the same method can turn out expensive when dealing with complicated geometries even for higher volumes. Additive manufacturing in such cases can turn out more profitable.
Product development time is also critical when choosing the manufacturing technology. While CNC machining or subtractive manufacturing have the ability to produce units faster as compared to additive manufacturing, choosing either of them still depends on the design specifics. But what brings you closer to choosing the right technology is determining the type of material to be used, the geometry and components required for the product design.
Additive Manufacturing
The rapidly growing additive manufacturing technique is increasingly replacing traditional methods. Although there are different types of additive manufacturing technologies, the commonality is that each method involves the same process of printing material layer by layer. Depending on the application and machine capability, the thickness of these layers vary and it can be as this as 16 microns. However, each additive manufacturing or 3D printing has its own strengths and weaknesses. The significant advantage of this technology is the ability to develop complex geometries and hollow spaces, which otherwise cannot be manufactured using traditional techniques.
Since the 3D printing technique does not rely on subtracting the material from the block, as in case of CNC machining or molding; complex internal and external shapes can be easily generated without wasting extra material. The additive manufacturing technology is rapidly advancing and is becoming robust to print different varieties of materials with good surface finish. Its use is gradually transforming from merely producing prototype to actual usable part or product. As a matter of fact, aerospace companies like Boeing uses 30 parts developed through additive manufacturing in their Dreamliner 787 model. This is possible due to 3D printing techniques like Fused Deposition Modeling (FDM) and Direct Metal Laser Sintering (DMLS), which is capable of printing durable thermoplastics and metals that are used in conventional manufacturing techniques.
What are the benefits of Additive Manufacturing?
• Reduction of complex assemblies to one single part, which further helps in improving the structural stability
• There is no need of any extra tools, making it cost effective for smaller volumes
• Possibility to develop complex geometries which are impossible to develop through traditional techniques
• Ability to develop parts from wide range of materials including plastics, rubber, metal, carbon fiber, etc.
• Advanced 3D printing techniques can develop products with good surface finish requiring no further operations
• Most suited for developing prototypes
CNC Machining
CNC (Computerized Numeric Control) machining is generally the most adopted technique to develop products. Contrary to additive manufacturing where the material is added to build the part, CNC machining removes the material from a material block to develop the desired shape. CNC machines make use of 3D CAD models and design data to perform tooling operation on the block and develop accurate and functional parts made up of variety of materials. Although the manufacturing approach is conventional, which is to remove material and form the desired shape, CNC machining itself is an advanced method where the machine has the ability to perform an array of operations such as milling, drilling, machining, shaping etc. on single equipment. All the operations are performed automatically by reading the CAD file, requiring less human intervention and ultimately reducing chances of errors.
What are the benefits of CNC Machining?
• Ability to develop products of any engineering material
• Suitable for developing highly durable and accurate patterns for casting applications
• Accuracy allows the ability to develop products requiring tight tolerances and surface finish
• CNC machines can handle parts of any size from small to large
Injection Molding and Casting
The process of injection molding involves pouring liquefied materials into a mold, cooling it and removing the casted part from the mold or die. This method is applicable to develop products of wide range of materials like plastics, metals, glasses and elastomers. The benefit of this technique is that once a mold is developed, it can be used to produce products in masses. Moreover, the parts developed through this technique are much stronger than 3D printed parts.
However, the problem with injection molding lies in developing the molds that actually helps in producing the desired part. Since it requires first developing molds, there is often a front-end cost involved, which is not the case with the other two techniques mentioned above. As such, this technique is often utilized where the requirement is of higher production volumes. Since, creating a mold for smaller volumes is expensive and can affect the product price significantly.
What are the benefits of Injection Molding?
• Cost effective technique for high volume production
• Provides the ability to produce products in masses with same design specifications
• Applicable for wide range of materials
• Injection molding can produce parts that are highly durable and follow tight tolerances
Although each manufacturing technology has its own benefits and challenges, choosing the right one is purely dependent on the project specifications. There might also be a possibility where you might need multiple technologies for a single product. You can also utilize additive manufacturing to create molds and then utilize that mold for injection molding your part or product.
Featured Product
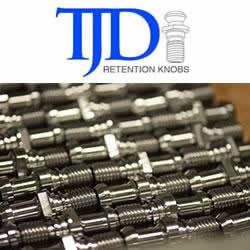