Allied Machine Offers Original T-A® Drill Ideal for a Range of Automotive Applications
Reduces downtime and lowers cost per hole
Allied Machine & Engineering, a leading manufacturer of holemaking and finishing tooling systems, highlights its line of replaceable tip Original T-A® drill systems, which significantly reduce downtime compared to solid tools. The T-A drill system features high performance inserts and holders ideal for automotive holemaking applications used in manufacturing engine blocks, crankshafts, piston, and suspension parts. Cost per hole using T-A drill systems can be 25-50 percent lower - or more - than other options in the marketplace.
Allied offers cast iron (-CI) geometries for its T-A drill that are ideal for automotive applications. Featuring lower rake angles and a tougher cutting edge to make them more resilient, the (-CI) drill tips are a good choice for blocks and heads made out of cast iron. Other application-specific drill tips are also available. Allied develops custom-configured shapes for tools, including a special form end for the end of a crankshaft.
Innovative coating options for the T-A drill include Allieds exclusive AM200® coating, which improves performance and extends tool life. A variety of insert grades are available for automotive applications, including C3 carbide, a wear-resistant carbide offering the best life in gray cast iron and C2 carbide, a good choice for aluminum and other nonferrous applications.
C1 options are available for steel applications using the GEN2 T-A® drill, which fits into the same holder as the Original T-A and provides even better performance and longer tool life for automotive applications.
Featured Product
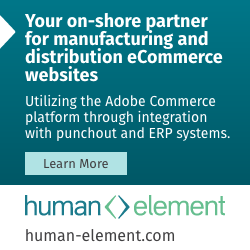