Amada Miyachi Europe announces Hot Crimping Resistance Welding Systems
Amada Miyachi Europe announces the availability of complete hot crimping resistance welding systems, ideal for joining insulated copper wire to cable shoes or terminals. A great option for high intrinsic value products, the hot crimping systems include weld heads, transformer, power supply, and process monitor.
Amada Miyachi Europe announces the availability of complete hot crimping resistance welding systems, ideal for joining insulated copper wire to cable shoes or terminals. A great option for high intrinsic value products, the hot crimping systems include weld heads, transformer, power supply, and process monitor. The systems provide a faster and more cost effective alternative to removal of copper wire coating by lasers or mechanical means before making the electrical connection.
Amada Miyachi Europe specializes in consulting with customers to correctly match hot crimping applications with the right process and equipment. With a full range of resistance welding hot crimping technology, Amada Miyachi Europes solutions range from the highly delicate, fine control required to hot crimp wires as small as 40 microns (µm) to the high power and high force required for very large wires.
The unique systems include a high-force MIYACHI PECO weld head, which mechanically holds the electrodes and feeds the electrical current to the electrodes. An integrated water cooling system actively cools all components to prevent overheating during production. A MIYACHI PECO power supply and transformer accurately emit the programmed electrical power. All electrical parameters can be guarded and stored by a MIYACHI PECO MG3, the ultimate resistance welding process monitor.
With the Amada Miyachi Europe hot crimping system, there is no metal stripping or removal, guaranteeing maximum strength. A unique weld to displacement feature allows the equipment to be programmed to reach the specified compression, after which the current flow and heating is switched off. This compensates for part-to-part variation, and lets users program a parameter that is closely related to joint quality.
Featured Product
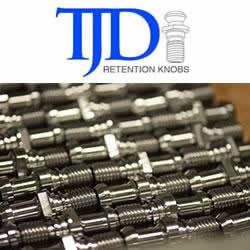