German Switch Manufacturer, Berker, Improves Agility, Reduces Prototype Testing Time by 85% by 3D Printing Injection Molds
Average cost per mold reduced by a whopping 83% with 3D printing Video: Watch how Berker makes a switch more efficiently with 3D printed injection molds
MINNEAPOLIS & REHOVOT, Israel--(BUSINESS WIRE)--Stratasys Ltd. (Nasdaq:SSYS), the 3D printing and additive manufacturing solutions company, today announced that German switch manufacturer, Berker, is significantly reducing its production costs and time for testing electrical component prototypes by using Stratasys 3D printed injection molds.
Injection molding, the process of injecting plastic material into a mold cavity where it cools and hardens to the configuration of the cavity, is one of the worlds most widely used manufacturing processes. Stratasys 3D printed injection molds are used to create prototype parts in order to detect issues in the parts form, fit and function in the actual final material. Video: Watch how Berker makes a switch more efficiently with 3D printed injection molds.
A newly designed Berker electrical component required parts produced using injection molding. Once assembled, the parts had to pass an electrostatic discharge (ESD) test conducted by an independent testing agency which meant that the switch prototype had to use the same materials as the final part. Instead of using metal injection molds to test the designs, which are very costly and time consuming to produce, Berker decided to try 3D printed injection molds produced on a Stratasys Connex multi-material 3D Printer. One of the biggest challenges was that the newly designed parts needed to fit precisely in order to snap fit together with an existing metal mold-produced part.
Berker Makes the Switch
Berker produced a series of 3D printed injection molds using Stratasys PolyJet 3D printing technology with Digital ABS™ material. Each 3D printed mold, with a different geometry, was used to inject a different final part material: ASA, PC and TPE.
"This new flexibility enables us to try out two or three different solutions at the same time to get the best result," said Andreas Krause, Head of Technical Department & Manufacturing, Berker. "The confirmed quality of our products produced using these functional prototypes has accelerated our R&D processes."
The resulting time and cost savings were impressive, with an average 83% reduction in cost per mold and 85% reduction in production time.
"Stratasys 3D printed injection molds have helped Berker save time and reduce costs while making working prototype assemblies in the final material," added Krause. "This technology is now used now all over our company to make sample parts in ‘real materials."
Stratasys enabled Berker to successfully overcome their challenges by 3D printing molds that were used to produce their parts with the proper tolerances and material selection-all at a fraction of the time and cost of the traditional molding process. Today, Berker has the component in full production.
"3D printing injection molds are often an optimal solution for product prototyping and low volume manufacturing," said Nadav Sela, Director, Manufacturing Tools, Stratasys. "For a very low production cost and quick turnaround time, they enable the manufacturer to produce parts with complex geometries in final materials before investing in mass production. And after testing the injected prototype part, if designs need to be adjusted, a new mold can produced in just a few hours, again saving significant time and expenditures."
Berker is a leading German designer and manufacturer of high quality electronic switches and intelligent building management systems. The company has won numerous awards for its designs, which can be found in buildings around the world.
For more than 25 years, Stratasys Ltd. (NASDAQ:SSYS) has been a defining force and dominant player in 3D printing and additive manufacturing - shaping the way things are made. Headquartered in Minneapolis, Minnesota and Rehovot, Israel, the company empowers customers across a broad range of vertical markets by enabling new paradigms for design and manufacturing. The companys solutions provide customers with unmatched design freedom and manufacturing flexibility - reducing time-to-market and lowering development costs, while improving designs and communications. Stratasys subsidiaries include MakerBot and SolidScape, and the Stratasys ecosystem includes 3D printers for prototyping and production; a wide range of 3D printing materials; parts on-demand via Stratasys Direct Manufacturing; strategic consulting and professional services; the GrabCAD platform with over 3 million professional users; and the Thingiverse and GrabCAD communities with over 2 million 3D printable files for free designs. With more than 2,700 employees and 800 granted or pending additive manufacturing patents, Stratasys has received more than 30 technology and leadership awards. Visit us online at: www.stratasys.com or http://blog.stratasys.com/, and follow us on LinkedIn.
Featured Product
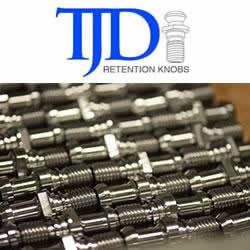
T.J. Davies' Retention Knobs
Our retention knobs are manufactured above international standards or to machine builder specifications. Retention knobs are manufactured utilizing AMS-6274/AISI-8620 alloy steel drawn in the United States. Threads are single-pointed on our lathes while manufacturing all other retention knob features to ensure high concentricity. Our process ensures that our threads are balanced (lead in/lead out at 180 degrees.) Each retention knob is carburized (hardened) to 58-62HRC, and case depth is .020-.030. Core hardness 40HRC. Each retention knob is coated utilizing a hot black oxide coating to military specifications. Our retention knobs are 100% covered in black oxide to prevent rust. All retention knob surfaces (not just mating surfaces) have a precision finish of 32 RMA micro or better: ISO grade 6N. Each retention knob is magnetic particle tested and tested at 2.5 times the pulling force of the drawbar. Certifications are maintained for each step in the manufacturing process for traceability.