SAKOR TECHNOLOGIES ANNOUNCES MOVE TO LARGER, UPDATED FACILITY
COMPANY'S ACCELERATING SALES GROWTH HAS CREATED A NEED FOR EXPANDED FACILITIES
SAKOR Technologies, Inc., a recognized leader in the area of high-performance dynamometer systems, announces that it has moved from its previous facility in Okemos, Michigan to a much larger facility in Owosso, Michigan. The company has grown rapidly in the past several years, and the new building better supports SAKORs current and future growth.
The new facility, which will house the companys administrative, engineering, and manufacturing operations all together, formerly housed Baker Colleges Auto/Diesel Institute of Michigan. As such, the buildings design and facilities are ideal for SAKORs needs: it currently measures 20,000 sq. ft., has ample high-voltage electrical power, and is laid out in a way that is exceptionally convenient for SAKORs manufacturing needs.
"We look forward to the opportunity to work with Baker College that the move to this new facility will allow, and hope that our proximity will foster a sustained, mutually beneficial relationship," said Randal Beattie, President of SAKOR. "Taking over their facility, which was already set up in way that is highly conducive to our companys manufacturing needs, was truly an ideal solution."
The new facilitys production bays are large enough to accommodate manufacturing more products at one time and manufacturing much larger, more sophisticated projects on-site than were previously possible. These building features will play a part in sustaining the companys accelerating growth curve into the future.
"Weve been growing for quite some time, and since our growth rate has been accelerating dramatically in recent years, we felt that it was time to find a new facility that is better suited to both our current and future production needs. Fortunately, this building was available and is a prime location for the next phase of SAKORs growth," Beattie added. "Our team is excited for this next stage, and was motivated to move into the new building quickly in order to continue manufacturing without delays."
While SAKOR will likely undertake renovations to the new building in the near future, the company was able to move into the new space quickly, thereby allowing them to keep up with a busy production schedule and meet all promised delivery dates.
####
About SAKOR Technologies, Inc.
SAKOR Technologies, Inc. is a recognized leader in the manufacture and development of reliable and cost-effective automated test instrumentation systems for a wide range of applications. For over 29 years, the company has been providing quality products and superior customer service to a variety of markets including automotive, military, aerospace, marine, heavy equipment, performance racing, electric motor, consumer appliance and more.
For more information, contact us at 989-720-2700, via e-mail at: info@SAKOR.com, or visit SAKORs website at www.sakor.com.
Product or service trademarks mentioned herein are the trademarks of their respective owners
Featured Product
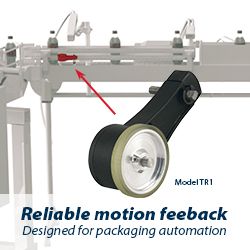
Model TR1 Tru-Trac
The Model TR1 Tru-Trac® linear measurement solution is a versatile option for tracking velocity, position, or distance over a wide variety of surfaces. An integrated encoder, measuring wheel, and spring-loaded torsion arm in one, compact unit, the Model TR1 is easy to install. The spring-loaded torsion arm offers adjustable torsion load, allowing the Model TR1 to be mounted in almost any orientation - even upside-down. The threaded shaft on the pivot axis is field reversible, providing mounting access from either side. With operating speeds up to 3000 feet per minute, a wide variety of configuration options - including multiple wheel material options - and a housing made from a durable, conductive composite material that minimizes static buildup, the Model TR1 Tru-Trac® is the ideal solution for countless applications.