Schneider Packaging Equipment Unveils State-of-the-Art Training Lab for Customers
Lab to feature hands-on training without slowing or stopping production lines
BREWERTON, N.Y. — Schneider Packaging Equipment Co., a leading manufacturer of end-of-line solutions for case packing, sealing and palletizing, has built a state-of-the-art training laboratory at its headquarters in upstate New York. The lab provides customers the opportunity to train on equipment in a controlled environment. Through hands-on training, customers are able to learn specific technical skills without slowing or stopping their production lines, which helps lower the learning curve once the new system is in place.
"Schneider Packaging Equipment now offers training on everything from programmable logic controllers to robotics," said Jim Kent, director of aftermarket services, Schneider. "By training customers in a classroom environment with a training cell and structured labs, we know their experience will directly translate to the equipment they are running in their facilities. Instead of having to learn a piece of equipment after an install, customers and employees will know the machine inside and out prior to delivery."
Training courses include:
Robotic Training Cell
1. Introduction to Schneider robotics
2. General FANUC robotics
3. Unit load creation using Pallet Pro and/or Schneider pallet generation software
4. Robot troubleshooting
Programmable Logic Controllers (PLCs) Training
1. Introduction to PLCs
2. Introduction to Schneider PLC logic
3. Troubleshooting PLCs
4. Product select addition to PLC
5. HMI fundamentals
Servo Motor Training
1. Introduction to servos
2. Servo troubleshooting
In addition to customers, Schneider employees will use the training facility. The company relies on the continued development of its highly trained technicians to serve its customers. With the lab and its miniature robotic palletizing cell, service and maintenance training will occur more frequently with a broader range of training programs increasing the number of Schneider FANUC robot-certified technicians.
"The training facility at Schneider is very impressive," said Jason Markesino, lead technical trainer, Applied Manufacturing Technologies. "The cell provides customers and employees a hands-on experience with a variety of automation hardware and software, such as PLC, VFD (variable-frequency drive), servo and robotics. It replicates real-world applications, preparing employees to troubleshoot potential issues in the field. It is encouraging to see Schneiders investment in its employees, and in providing the complete package for its customers."
Schneider is currently accepting customer requests to use the training lab as part of a new equipment purchase or based on individual needs. Training can be scheduled by contacting Rick Buffham at 315-676-3035 ext. 469 or at rbuffman@schneiderequip.com.
About Schneider Packaging Equipment Co., Inc.:
Schneider manufactures a complete line of robotic palletizing, case packers, tray packers, high performance random case sealers, specialty cartoning systems and integrated packaging solutions. Schneider is fully committed to delivering the most environmentally sustainable, intelligently designed solutions that offer the most efficient use of materials, energy, air and water, and provide real cost savings to end users. Schneider offers a variety of ancillary equipment such as case erectors, cartoners, conveyors, pallet dispensers, shuttle cars, automatic guided carts and elevators that can be easily integrated with coding/labeling equipment, RFID/bar code scanners, weight checking and stretch or shrink wrapping equipment to provide a complete turnkey system solution.
Schneider is the first packaging equipment company to concurrently hold the titles RIA Certified Robot Integrator, FANUC Robotics Certified Servicing Integrator and Authorized Systems Integrator, and Machine Builder partner in the Rockwell Automation PartnerNetwork™ program. For more information, visit www.schneiderpackaging.com.
Featured Product
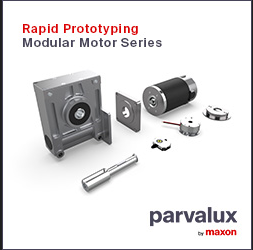