Big Time Savings on Small Part: First 3-D-printed Component Flies on U.S. Navy's Trident II D5 Missile
By using entirely digital processes, Lockheed Martin engineers designed and fabricated the new component in half the time of traditional methods.
SUNNYVALE, Calif., March 18, 2016 /PRNewswire/ -- The U.S. Navy's Fleet Ballistic Missile program flew into the future this week with its first 3-D-printed missile component. A part called a connector backshell made its debut as part of the Navy's successful test flights March 14 to 16 of three Trident II D5 Fleet Ballistic Missiles built by Lockheed Martin (NYSE: LMT).
By using entirely digital processes, Lockheed Martin engineers designed and fabricated the new component in half the time of traditional methods. The connector backshell, which protects cable connectors in the missile, is made from an aluminum alloy and measures about an inch across.
The D5 missile, the world's most reliable large ballistic missile, now has achieved a total of 160 successful test flights since design completion in 1989. In the most recent tests, the Navy launched the unarmed missiles in the Atlantic Ocean from a submerged submarine. The missiles were converted into test configurations using kits produced by Lockheed Martin that contain range safety devices and flight telemetry instrumentation. The test flights were part of a Follow-on Commander's Evaluation Test of the Trident Strategic Weapon System conducted under the testing guidelines of the Joint Chiefs of Staff.
"These tests demonstrate the readiness and reliability of this crucial system that protects what matters most for the nation," said Eric Scherff, vice president of Fleet Ballistic Missile programs, Lockheed Martin Space Systems. "The Trident Strategic Weapon System stands guard every minute of every day, thanks to the dedication and forward thinking of the Navy program office, the submarine crews and the industry team."
The 3-D-printed component for the D5 missile is an example of the improved products and processes enabled by Lockheed Martin's Digital Tapestry, a set of advanced manufacturing tools that connect a product's digital life from concept to production to sustainment. Lockheed Martin also has flown additively manufactured parts on planetary probes, satellites and spacecraft for human use.
The Trident II D5 missile is deployed aboard U.S. Navy Ohio-class and U.K. Royal Navy Vanguard-class submarines to deter nuclear aggression. The three-stage ballistic missile can travel a nominal range of 4,000 nautical miles and carry multiple independently targeted reentry bodies.
The D5 is the sixth in a series of missile generations deployed since the sea-based deterrent program began. Lockheed Martin has been the Navy's strategic missile prime contractor since 1955 - one of the longest government and industry partnerships for a major U.S. weapon system. The company also performs program management and engineering services for the Royal Navy under the Polaris Sales Agreement.
For additional information, visit our website: www.lockheedmartin.com/trident
About Lockheed Martin
Headquartered in Bethesda, Maryland, Lockheed Martin is a global security and aerospace company that - with the addition of Sikorsky - employs approximately 126,000 people worldwide and is principally engaged in the research, design, development, manufacture, integration and sustainment of advanced technology systems, products and services.
Featured Product
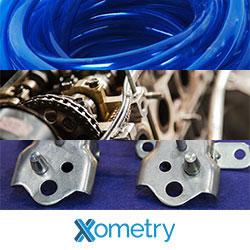
Get RFQs on Die Casting, Stamping, and Extrusion With Xometry, Your Source for Custom Parts
Xometry is your source for custom parts. Now, in addition to getting instant quotes on 3D Printing, CNC Machining, Sheet Metal, and Injection Molding, customers can create and send RFQs for die casting, stamping, and extrusion work to our nationwide network of pre-vetted manufacturers with just a 2D drawing. You will receive and be able to review responses from qualified shops within 7 days on an advanced web-based RFQ management platform. To learn more go directly to our site to issue and RFQ today. Stop wasting time managing RFQs through email and by phone, and start issuing RFQs at scale and in the cloud.