Markforged Launches High-Strength, High-Temperature Fiberglass
Markforged customers working in high temperature environments can now take advantage of same day, strong parts.
CAMBRIDGE, Mass., March 18, 2016 /PRNewswire/ -- Today Markforged announces their newest material which allows aerospace and automotive customers to leverage Mark Two parts for use in "under hood" applications. This new fiberglass is twice as strong as Markforged's standard fiberglass material and has a 30% higher heat deflection point (140°C).
Markforged empowers engineers with industrial strength 3D printing. By reinforcing nylon parts with continuous strands of carbon fiber, fiberglass, Kevlar®, and now high-strength high-temperature (HSHT) Fiberglass, the Mark Two prints parts as strong as aluminum for everything from functional prototyping, tooling and fixtures, to customized end-use parts.
"2016 is the year of materials at Markforged," says CEO Greg Mark. "Throughout the year you'll see the release of stronger, more advanced materials that expand the range of parts that can be 3D printed."
In addition to the launch of the HSHT fiberglass, Markforged is officially shipping the Mark Two industrial strength 3D printer. Announced at SolidWorks World 2016 in the beginning of February, the first Mark Twos started shipping to customers before the end of February.
High-Strength, High-Temperature fiberglass is available with the Mark Two Enterprise Kit.
About Markforged
Markforged's mission is to bring high strength 3D printing to everyday engineering. Offering the world's only 3D printing systems capable of automatically reinforcing engineering plastics to aluminum levels of performance and beyond, Markforged enables every business to easily manufacture parts with structural strength right on the desktop. The Mark Two Industrial Strength 3D Printer empowers professional users to affordably create workhorse 3D parts that solve real problems, as well as realize reinforced structures never before possible. Markforged technologies are delivered with thoughtful, powerful software designed for collaboration, sharing, and scaling. For more information, visit https://www.Markforged.com.
Featured Product
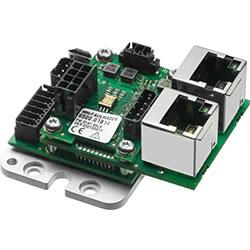
MOTION CONTROLLERS FOR MINIATURE DRIVES AND MICRODRIVES
FAULHABER has added another extremely compact Motion Controller without housing to its product range. The new Motion Controller is ideal for integration in equipment manufacturing and medical technology applications. With 36 V and 3 A (peak current 9 A), it covers the power range up to approx. 100 W and is suitable for DC-motors with encoder, brushless drives or linear motors.