Laser-based micro processing on the road to success
Ultrashort pulse laser production systems on the advance / Manufacturers of laser production systems for micro material processing will demonstrate their competence at LASYS 2016
"Micro and fine processing accounts for more than half of the global market for laser material processing systems," said the laser market analyst Dr. Arnold Mayer, CEO of Optech Consulting. The topic of laser-based micro processing will therefore be the focal point of LASYS 2016 along with macro processing.. As the only international trade fair, LASYS clearly focuses on laser material processing and will present the latest laser production systems, laser-specific components and subsystems at the Stuttgart Trade Fair Centre for the fifth time from 31 May to 2 June 2016.
Various applications thanks to ultrashort pulse laser systems
"In the last five years ultrashort pulse laser systems, in particular, have led to new production engineering applications in precision and micro processing," said Dr. Siegfried Pause, Managing Director of the LASYS exhibitor LLT Applikation. Especially in micro processing, it is essential to avoid thermal defects in the peripheral areas of the processing zone and, thus, deformations. Some machine manufacturers are therefore relying here on ultrashort pulse lasers (USP lasers) to an ever increasing extent. Extremely short laser pulses, which have an effect on the material, produce non-linear interaction processes that practically lead to material removal without heat exposure. This is also called ablation or cold processing. Minute and filigree parts can be produced free of burrs and without thermal distortion. "Thanks to the use of USP laser systems, it has become possible for the first time," added Dr. Pause, "to structure thin layers, for example, on optical elements with a laser in very small dimensions without damaging the substrate in any way." A large number of industries are profiting from this, for example the automotive, medical technology, precision engineering, optical, electronics, environmental engineering, measuring technology, jewellery and design industries. Jan Wieduwilt, Industry Manager for Micro Processing at Trumpf, mentioned other advantages: "Ultrashort pulse laser systems process nearly every material gently, precisely and in a highly productive way. They drill super fine holes in metals or printed circuit boards, cut medical stents from small polymer tubes or unbreakable display glass for smartphones, structure surfaces of thin-layer solar cells, separate wafer-thin plastic films and process brittle ceramic parts, even diamonds.". In medical technology lasers cut stents, i.e. free of burrs and in minute tube dimensions under 0.5 mm and wall thicknesses of 0.1 mm. "Conventional wet-cutting processes are not possible here from technical aspects," said the Head of LLT.. He added: "Economical production of stents in medical technology has only actually become possible through micro laser cutting. Implants can become even smaller and can be used in blood vessels in the head or even in the eye." The exhibitor LLT will present advanced laser production systems relating to this topic area at LASYS 2016.
Numerous ways to increase efficiency
Laser production systems for micro processing are also demonstrating their cost-effectiveness through the development of new optical elements called diffractive optical elements (DOE). They allow, for example, multi-beam processes in which the laser beam is split into many partial beams. Dr. Pause explained: "Process efficiency in micro structuring can therefore be increased many times over."
Efficiency can also be increased in traditional laser processing methods, for example laser welding, through special beam shaping optics. In this case the beam profile is ideally adapted to the specific processing task. Another aspect in regard to cost-effectiveness is linking of the laser process with upstream and downstream work steps which can generally make a production process for a special product more economical. "Laser welding can, for example, be perfectly integrated in automated production processes. Car body production in the automotive industry is now almost inconceivable without laser welding. This philosophy is also increasingly making inroads into micro processing," said the Head of LLT. "Corrosion-free marking using USP laser systems, e.g. of medical operating instruments, is another example of applications which have only become possible through lasers," added the Trumpf expert Wieduwilt. According to Wieduwilt, other important factors for the cost-effectiveness of laser-based micro processing include wear-free operation of the laser, the high level of reproducibility and the excellent quality of the results.
Laser-based production of OLED displays
According to Trumpf, a new field for the electronics industry is opening up with the laser lift-off process, for example for OLED displays. Bent rigid displays - and in future freely bendable displays - are becoming more popular, especially for wearables, i.e. smart devices which are worn on the body, e.g. as glasses or a wristwatch. For this purpose, manufacturers are coating glass carrier plates with polyimid which acts as a substrate for the flexible display. Organic light emitting diodes (OLEDs) are affixed to this plastic. Following the coating processes, a laser beam detaches the OLED display from a glass plate which has held it during coating. The LASYS exhibitor Trumpf developed a new method using solid-state lasers for this process. "Unlike the Excimer lasers that have normally been used to date for this application, this beam source requires little maintenance and increases the available operating time, thus reducing production costs. The very short pulses make the process extremely efficient because one single pulse can process a larger area," summarised the Trumpf expert Wieduwilt. In particular, he sees further potential for laser micro processing in the functionalisation of surfaces, tribology and processing of future materials such as carbon fibre reinforced plastic (CFRP), especially for modern lightweight construction.
LASYS 2016 strongly oriented towards users
On the stands of the around 200 LASYS exhibitors users from every industry will encounter the collective expertise in the area of laser-based micro processing. First-rate experts will also answer questions on the technical and economic aspects of the use of laser production systems in material processing. The strong user orientation of this high-tech trade fair will be reflected, for example, in the première of the "Rapid Area", i.e. a joint stand for generative manufacturing, and in the varied accompanying programme which will feature, for instance, the practical technical forum "Lasers in Action" which will enable visitors - from beginners through to laser specialists - to update and extend their level of knowledge.
About LASYS
LASYS is the only international trade fair to clearly focus on system solutions in laser material processing. Since the start of the trade fair in 2008, it has successfully become established as a user platform for the latest laser systems, machines and processes. LASYS covers all industries and materials, and is primarily aimed at decision-makers from international industry. The focal points of the trade fair are all proven, but also innovative manufacturing processes, applications and potential uses of lasers in industrial manufacturing.
Other trade fairs will be held concurrently with LASYS 2016 at the Stuttgart Trade Fair Centre and will produce synergy effects for visitors: the automotive shows with Automotive Testing Expo Europe, Engine Expo, Automotive Interiors Expo, Global Automotive Components and Suppliers Expo, the Autonomous Vehicle Test & Development Symposium, as well as O&S, International Trade Fair for Surface Treatments and Coatings, and parts2clean, Leading International Trade Fair for Industrial Parts and Surface Cleaning. The German Engineering Federation (VDMA) acts as the promotional supporter of LASYS.
LASYS 2016 will take place at the Stuttgart Trade Fair Centre from 31 May to 2 June 2016. For further information, visit: www.lasys-messe.de.
Featured Product
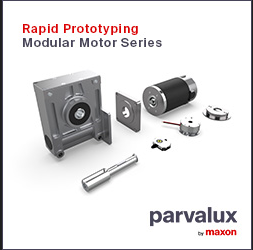