Molding Conference 2016 Announces Complete Technical Program
Plastics Technology announces agenda for 26th annual event on injection molding includes presentations on injection molding, automation, 3D printing, materials and process maintenance
Molding 2016, presented by Plastics Technology, today announced the complete line-up of speakers and technical sessions for its 26th annual conference. The three-day event will offer attendees unique ways to connect with leading suppliers, end-users and researchers of molding technologies.
The full agenda is available at: http://www.moldingconference.com
Taking place in New Orleans, LA, March 29-31, 2016, Molding 2016 includes more than 50 technical sessions examining design, material, machinery and applications technology used in injection molding. Specific topics include materials development, automation, tooling, additive manufacturing, materials drying/handling and the establishment and maintenance of a robust process.
Technical presenters include thought leaders from machinery suppliers Arburg GmbH, Engel, Milacron and more; leading injection molders including Extreme Molding, Makuta Technics Inc. and Noble Plastics; auxiliary suppliers like The Conair Group, Novatec and Universal Dynamics and materials suppliers Eastman Chemical Company, Covestro, Momentive and PolyOne Corp.
"This conference is uniquely focused on injection molding. As a result, our presenters represent the leading OEMs, contract manufacturers, equipment suppliers and researchers developing molding processes and equipment. If a company is involved in any part of the molding business, this is the event for learning about the processes, the products and the people, that are leading injection molding," commented Allison Miller, Event Director.
Registration is open for Molding 2016. Full event details are available at moldingconference.com.
Featured Product
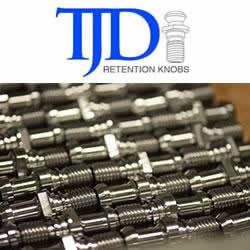
T.J. Davies' Retention Knobs
Our retention knobs are manufactured above international standards or to machine builder specifications. Retention knobs are manufactured utilizing AMS-6274/AISI-8620 alloy steel drawn in the United States. Threads are single-pointed on our lathes while manufacturing all other retention knob features to ensure high concentricity. Our process ensures that our threads are balanced (lead in/lead out at 180 degrees.) Each retention knob is carburized (hardened) to 58-62HRC, and case depth is .020-.030. Core hardness 40HRC. Each retention knob is coated utilizing a hot black oxide coating to military specifications. Our retention knobs are 100% covered in black oxide to prevent rust. All retention knob surfaces (not just mating surfaces) have a precision finish of 32 RMA micro or better: ISO grade 6N. Each retention knob is magnetic particle tested and tested at 2.5 times the pulling force of the drawbar. Certifications are maintained for each step in the manufacturing process for traceability.