EU-Funded Research on Automatic Guided Vehicles for Automating Logistics in Factories
Mass production and packaging in factories is already highly automated these days, but the same cannot be said for logistics. Movements of raw materials and finished products still depend heavily on manual labour. However, EU-funded research on Automatic Guided Vehicles means this is about to change over the next decade – and could create thousands of new jobs.
Moving raw materials and final products around factories and warehouses is a labour-intensive process, mainly using forklift trucks. It is traditionally error-prone, costly, inefficient (from both a planning and energy consumption perspective) and the cause of many accidents. Bottlenecks are a common occurrence at even the most automated factories, which complicates Just-In-Time delivery and inventory management.
The PAN-ROBOTS project, comprising six partners in five EU countries and supported by EU funding of EUR 3.33 million, was charged with providing innovative technologies for automating logistics operations in the so-called ‘Factory-of-the-Future (FoF).
‘Automatic Guided Vehicles (AGVs) used in factories today are still at an early stage of development. The companies using them get their Return of Investment quite soon, but these systems can be improved immeasurably by using on-board cameras, laser scanners and 3D mapping of facilities, explained Dr Kay Fürstenberg, of German sensor company SICK AG, coordinating the project.
A robot that can see round corners
PAN-ROBOTS focuses on four main work areas: exploration systems for 3D-mapping of the plant; advanced perception systems on-board the AGVs; a modern control centre for monitoring them, and cooperative infrastructure laser scanners distributed about the facility.
The most innovative technology in the project is a stereo camera with ‘fish-eye lenses, mounted on top of the AGV. It uses 3D images to constantly look out for obstacles.
The cameras 360-degree field of view (‘3D perception) and safety laser scanners (‘2D safety) ensure the robot has no blind spots and guarantee safety for the people that still work in the factory or warehouse. The vehicle can reverse with full vision and stops before, and navigates around, obstacles in its path. The perception system can even ‘see round corners by interacting with laser scanners at intersections.
PAN-ROBOTS underwent early tests at Coca-Colas bottling plant in Madrid. Now the team is preparing the soft drink makers Bilbao factory for real-world validation and a final demonstration as the project ends in October this year.
‘The results are very exciting, said Dr Fürstenberg, ‘and by trying it out at two plants, we are proving that the technology adapts to different facilities. Results include an innovative contour-based self-localisation technology, which relies on the identification of natural landmarks in the warehouse rather than installed reflectors, saving 90% on the installation costs of a reflector-based landmarking system.
The advanced AGVs developed also use 50% less energy compared to manual forklifts and they are many seconds faster per operation than current AGVs, meaning that in future fewer vehicles can do the same job. Additionally, the PAN-ROBOTS system can be installed in two instead of six months, saving on factory outage time.
First products being readied for market
Now the partners are discussing several products with existing customers. These have a chance of being launched on the market within the next few years. Because other systems will need more effort for industrialisation, the partners are looking to launch the camera and other systems within a medium-term perspective.
There is a good chance, that half of all European factories will be operating with AGV fleets by 2030, Dr Fürstenberg believes, potentially creating thousands of new jobs at robot manufacturers and their suppliers over the next decade.
http://cordis.europa.eu/
Featured Product
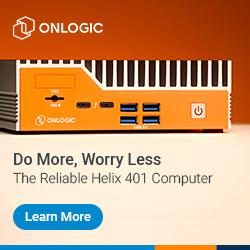