Optimizing Production Lines with SECS/GEM and Advanced Analytics
In today's rapidly evolving manufacturing landscape, efficiency and precision are more critical than ever. Factories are adopting smart technologies to optimize production lines, reduce downtime, and improve yield. One such transformative solution is the implementation of SECS/GEM (SEMI Equipment Communications Standard/Generic Equipment Model) protocols, which enable seamless communication between factory systems and equipment. Combined with advanced analytics, SECS/GEM offers unparalleled benefits for modern production lines.
This blog delves into how SECS/GEM and advanced analytics work together to revolutionize production processes, enhance productivity, and drive operational excellence.
Understanding SECS/GEM and Its Role in Manufacturing
SECS/GEM is a standardized communication protocol widely used in semiconductor and electronics manufacturing. It establishes a common language for equipment and host systems, enabling real-time data exchange and automation. By leveraging SECS/GEM software and interfaces, factories can monitor, control, and optimize equipment performance.
The SECS GEM protocol ensures compatibility across various machines, making it an ideal solution for facilities with diverse equipment. From tracking production metrics to automating repetitive tasks, SECS/GEM communication protocol is the backbone of many smart manufacturing systems. Its ability to facilitate seamless equipment integration aligns perfectly with the GEM300 standards, designed to enhance efficiency in semiconductor fabrication.
The Power of SECS/GEM and Advanced Analytics
While SECS/GEM provides the framework for communication, advanced analytics adds intelligence to the data. Together, they enable manufacturers to make data-driven decisions, predict equipment failures, and optimize workflows. Here's how SECS/GEM integration with analytics enhances production lines:
1. Real-Time Monitoring and Control
SECS/GEM communication protocols allow factories to collect real-time data from equipment. This data is analyzed to identify inefficiencies, monitor performance, and ensure consistent quality. Advanced analytics tools use this data to provide actionable insights, allowing operators to address issues before they escalate.
2. Predictive Maintenance
By combining SECS/GEM communication with analytics, manufacturers can predict equipment failures and schedule maintenance proactively. This reduces unplanned downtime and extends the lifespan of machinery, ensuring smooth production workflows.
3. Workflow Optimization
SECS/GEM interfaces enable automated workflows by executing predefined commands based on real-time data. Advanced analytics further optimize these workflows by analyzing patterns and recommending improvements, resulting in faster production cycles and higher throughput.
4. Enhanced Traceability
The SECS GEM protocol provides detailed logs of production processes. When integrated with analytics, these logs help track materials, monitor equipment usage, and ensure compliance with quality standards.
Overcoming Implementation Challenges
While SECS/GEM offers significant benefits, its implementation requires careful planning. Common challenges include:
Legacy Equipment Compatibility: Many factories have older machines that lack native SECS/GEM interfaces. Retrofitting these machines requires expertise and additional resources.
Data Security: Ensuring secure SECS/GEM communication is vital to protect sensitive production data.
Skill Gaps: Operators and IT teams must be trained in SECS/GEM software and analytics tools to maximize their effectiveness.
To address these challenges, manufacturers should collaborate with experienced solution providers who can deliver customized SECS/GEM integration services tailored to their specific needs.
Case Study: SECS/GEM in Action
A leading semiconductor manufacturer implemented SECS/GEM communication protocols and advanced analytics to optimize their production lines. By integrating SECS/GEM software with their existing systems, they achieved:
A 30% reduction in downtime through predictive maintenance.
Real-time visibility into production metrics, enabling faster decision-making.
Improved workflow efficiency, resulting in a 20% increase in throughput.
These results highlight the transformative potential of combining SECS/GEM integration with analytics.
The Future of SECS/GEM and Advanced Analytics
As manufacturing continues to evolve, the role of SECS/GEM communication protocols and advanced analytics will grow. Emerging technologies like artificial intelligence (AI) and machine learning (ML) will further enhance the capabilities of SECS/GEM systems, enabling smarter automation and more accurate predictions.
Manufacturers who adopt SECS/GEM integration today will be better positioned to embrace these advancements and stay ahead in a competitive landscape.
SECS/GEM, in combination with advanced analytics, is revolutionizing production lines by enabling real-time monitoring, predictive maintenance, and workflow optimization. By addressing implementation challenges and leveraging the power of data, manufacturers can achieve significant gains in efficiency, yield, and scalability.
Incorporating SECS GEM protocol into modern production lines is no longer a choice but a necessity for businesses aiming to lead in Industry 4.0. With the right approach, SECS/GEM communication and analytics will pave the way for smarter, more efficient manufacturing processes.
Featured Product
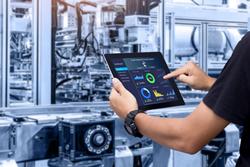