Smart Manufacturing: Revolutionizing Industries Through Cutting-Edge Technologies
Smart manufacturing integrates advanced technologies like MES, PLCs, SCADA, and IoT to optimize operations, improve efficiency, and ensure flexibility. It drives innovation across industries like automotive, pharmaceuticals, and energy, enhancing productivity, quality, and sustainability.
The manufacturing landscape is undergoing a monumental transformation as the era of smart manufacturing takes hold. Powered by advanced technologies like Manufacturing Execution Systems (MES), Programmable Logic Controllers (PLCs), Supervisory Control and Data Acquisition (SCADA), Distributed Control Systems (DCS), Enterprise Resource Planning (ERP), Human-Machine Interfaces (HMI), and Machine Vision, this approach integrates intelligence, automation, and connectivity into industrial processes. Smart manufacturing enables businesses to enhance efficiency, improve quality, and achieve flexibility in ways that were once unimaginable. In this blog, we'll delve into these technologies, their functionalities, and their profound impact on industries such as automotive, food and beverage, pharmaceuticals, aerospace and defense, consumer electronics, and energy.
The global smart manufacturing market is experiencing rapid growth as industries embrace digital transformation to enhance efficiency, productivity, and flexibility. Smart manufacturing leverages advanced technologies like Manufacturing Execution Systems (MES), Programmable Logic Controllers (PLCs), Supervisory Control and Data Acquisition (SCADA), and Machine Vision to optimize operations and drive innovation.
The Technological Pillars of Smart Manufacturing
At the heart of smart manufacturing lies a suite of interconnected technologies that drive its success. The Manufacturing Execution System (MES) is central to this ecosystem, acting as a real-time bridge between enterprise-level systems and the shop floor. MES tracks and optimizes production processes by collecting and analyzing data to ensure operational efficiency. It integrates seamlessly with other systems, such as ERP and shop-floor devices, allowing manufacturers to monitor everything from raw material usage to the final product. With MES, businesses can reduce downtime, improve production schedules, and ensure consistent quality standards.
The Programmable Logic Controller (PLC) is another vital component, providing automation and control for industrial processes. These rugged devices execute pre-programmed logic based on inputs from sensors and actuators, enabling precise control of machinery. PLCs are celebrated for their reliability and versatility, making them indispensable in everything from simple machine operations to complex multi-step processes. When paired with SCADA or HMI systems, PLCs become even more powerful, offering real-time monitoring and seamless control.
Supervisory Control and Data Acquisition (SCADA) systems add another layer of intelligence by offering centralized control and monitoring of industrial processes. SCADA systems gather data from various field devices, analyze it, and present actionable insights through intuitive graphical interfaces. Operators can use SCADA to monitor equipment health, identify potential failures, and optimize performance in real time. The result is enhanced operational reliability and reduced downtime, both critical for modern manufacturing.
For industries that prioritize process control, the Distributed Control System (DCS) is an invaluable tool. DCS uses multiple controllers distributed across a facility to manage different sections of the operation independently. This architecture ensures high fault tolerance and scalability, making it ideal for industries such as energy and chemicals. By integrating control and data management into a unified system, DCS provides seamless coordination across complex processes.
Enterprise Resource Planning (ERP) systems, meanwhile, play a foundational role in the business side of manufacturing. ERP integrates key business functions such as inventory management, procurement, and financial planning, ensuring that every aspect of the operation is aligned with production objectives. When ERP connects with MES and shop-floor systems, manufacturers can achieve complete visibility across their operations, enabling better decision-making and resource optimization.
A critical interface between humans and machines is provided by Human-Machine Interfaces (HMIs). These systems allow operators to interact with equipment through user-friendly dashboards, touchscreen controls, and visualizations of real-time data. HMIs empower operators to respond quickly to anomalies, optimize machine settings, and improve productivity with minimal training.
Finally, Machine Vision systems bring precision and automation to inspection, quality control, and tracking. By using cameras, sensors, and advanced image-processing algorithms, machine vision systems can identify defects, measure dimensions, and recognize patterns with remarkable accuracy. This technology is particularly valuable in industries like pharmaceuticals and electronics, where quality and consistency are paramount.
Applications of Smart Manufacturing Across Industries
Smart manufacturing technologies are reshaping various sectors, each with its unique requirements and challenges. In the automotive industry, the integration of MES, PLCs, and machine vision has revolutionized production lines. Automated systems ensure consistent quality, while machine vision technologies detect defects in components before assembly. SCADA systems monitor equipment performance, minimizing downtime and maximizing throughput. These advancements allow automakers to meet high consumer demands for quality and innovation while reducing costs.
The food and beverage industry has also embraced smart manufacturing to address concerns about hygiene, quality, and traceability. MES ensures compliance with stringent safety regulations by tracking every step of the production process. PLCs and HMIs automate critical tasks like packaging and labeling, while SCADA systems monitor environmental factors such as temperature and humidity. These technologies not only enhance efficiency but also reduce waste, a critical factor in sustainable production.
In the pharmaceutical industry, precision, compliance, and quality assurance are non-negotiable, making smart manufacturing technologies indispensable. MES enables complete traceability of products, from raw materials to distribution, while ensuring adherence to regulatory standards. Machine vision systems inspect packaging for defects and ensure accurate labeling, which is crucial in maintaining patient safety. Distributed Control Systems play a pivotal role in managing complex drug manufacturing processes, ensuring consistency and precision at every stage.
The aerospace and defense industry demands the highest levels of reliability and accuracy, making it a natural fit for smart manufacturing. MES and ERP systems streamline complex production planning, while PLCs and SCADA systems ensure precise control of advanced manufacturing processes. These technologies also facilitate compliance with rigorous safety and quality standards, enabling manufacturers to meet the industry's stringent requirements.
The consumer electronics sector benefits from smart manufacturing through faster production cycles and greater customization capabilities. PLCs and HMIs control high-speed assembly lines, while machine vision ensures precise placement of tiny components. By integrating MES with ERP systems, manufacturers can optimize supply chains and production schedules to meet ever-changing consumer demands.
In the energy sector, SCADA and DCS systems play a central role in monitoring and controlling power generation and distribution. These technologies optimize energy efficiency, reduce emissions, and improve grid reliability. Smart manufacturing also supports the integration of renewable energy sources, paving the way for a more sustainable future.
The Benefits of Smart Manufacturing
Smart manufacturing delivers a host of benefits that extend beyond operational efficiency. One of its most significant advantages is the ability to enhance productivity by automating repetitive tasks and optimizing resource allocation. Technologies like MES and SCADA provide real-time insights, enabling businesses to identify bottlenecks and implement solutions swiftly.
Improved product quality is another hallmark of smart manufacturing. With tools like machine vision and MES, manufacturers can maintain strict quality standards, detect defects early, and reduce rework and waste. This ensures that customers receive high-quality products while minimizing production costs.
Flexibility is a key advantage in today's fast-paced markets. Smart manufacturing technologies allow businesses to adapt to changing demands quickly, whether by enabling mass customization or scaling production up or down as needed. This agility is crucial for staying competitive in dynamic industries.
Moreover, smart manufacturing drives cost savings by reducing downtime, energy consumption, and material waste. Advanced analytics and predictive maintenance capabilities minimize unplanned equipment failures, further enhancing operational efficiency.
Finally, smart manufacturing promotes sustainability by optimizing energy use, reducing waste, and supporting circular economy initiatives. These efforts not only benefit the environment but also improve a company's reputation among increasingly eco-conscious consumers.
Challenges and the Road Ahead
While the benefits of smart manufacturing are immense, challenges remain. High initial investment costs can deter small and medium-sized enterprises, and the need for skilled personnel to operate and maintain advanced systems can be a barrier to adoption. Cybersecurity is another critical concern, as increased connectivity exposes industrial systems to potential threats.
Despite these challenges, the future of smart manufacturing is bright. Emerging technologies such as artificial intelligence, the Industrial Internet of Things (IIoT), and 5G connectivity are set to further enhance its capabilities. These innovations will enable even greater levels of automation, intelligence, and integration, making smart manufacturing more accessible and impactful than ever before.
Featured Product
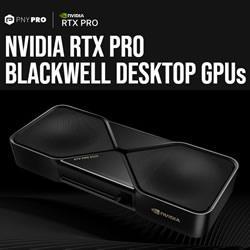