Plastic Injection Molding - What? How? Why?
Plastic injection molding is an advanced and modern manufacturing process, a manufacturing method that has evolved over the years to accelerate the production of many products. Speed and simplicity of production are key considerations in manufacturing, especially in mass production, as this brings many advantages. These advantages include lower development costs, greater forecast accuracy, faster innovation and greater market share.
What is Injection Molding?
Injection molding is a manufacturing process in which molten material is injected into a prepared mould and allowed to cool. As it cools, the material solidifies and takes on the shape of the mould before being expelled. Although the process can be used for one-off production, it is usually used for mass production of identical parts. The most common materials used in injection molding are plastics or elastomers.
Due to its high output rate and consistency in quality, injection molding is used in a wide range of different industries for the manufacture of electrical components, automotive parts, basic consumer plastics, furniture components, etc.
How Does Injection Molding Work?
Injection molding with special injection molding machines. The manufacturing process is divided into the following steps:
Step 1 - Creating the mould
The first step in injection molding is to create a mould. Based on the specifications of the 3D model of the part, a mould for the part to be manufactured is designed using computer-aided design, following several injection moulding guidelines. It is then manufactured in two parts, usually using CNC machining. The moulds are made of metal (mainly steel or aluminium).
Step 2 - Injection
The separate halves of the mould are placed in the clamping unit of the injection moulding machine and held tightly together by means of this clamping unit. In the form of granules or pellets, the raw material is introduced into a drum in which it is heated at high temperature and pressure until it melts. The material, now in a molten state, is immediately injected into the mould cavity, filling the entire space in the mould. It then cools and solidifies, forming the shape of the mould.
Step 3 - Stripping and Fine machining
After the material has completely cooled and cured, the mould is opened by a clamping device and the cured finished part is ejected. Some post-processing operations are performed on the finished part. These operations include removal of excess material and support structures, surface finishing, and, if necessary, painting, plating, heat treating, etc. The finished part is then processed into a mould.
Why Choose Injection Molding?
Injection molding has many advantages as a manufacturing process.
1.High production output
This is one of the most important advantages of the process. The process takes 20-120 seconds to complete a cycle, making it possible to manufacture hundreds of parts per hour.
2.Minimum labour cost
The injection molding process is fully automated and can be operated by one operator alone. As a result, production costs are reduced due to the reduction in the number of labourers.
3.Design flexibility
Injection molding enables manufacturers to create a wide range of designs, regardless of their complexity and sophistication.
4.Quality consistency
This process follows a sequential pattern when creating identical parts. As a result, the quality of the first one will be similar to the quality of the second, third and next one.
5.Less waste
Unlike other production processes such as CNC machining, which cuts away large quantities of parts, injection moulding produces very little debris. These small amounts of unused material can be collected and recycled.
6.Compatible with a wide range of materials
The injection molding process allows the use of a wide range of materials and colours at the same time.Because the finished product is already finished at the top, there is little work to be done afterwards.
Defects in Injection Molding
Despite the many advantages of injection molding, it has several disadvantages.
1.Visible defects in the finished product
Despite the accuracy of the process, the finished product may still contain minor defects left over from injection molding. Please note that such defects do not affect the functionality of the part. Defects include distortion, nozzle drooling, shrink marks, flow marks, weld marks, under-injection, and under-molding.
2.Higher costs
The set-up costs for injection molding are high. The equipment and tools required are very expensive. Mould prototypes also need to be manufactured and tested repeatedly. In addition, experienced skilled workers are required to design the moulds to avoid additional costs in the production process.
3.Not suitable for large parts
Due to the limitations of the mould, it is very difficult to produce large parts of the same density. Large parts can only be manufactured in several small parts and then assembled.
Conclusion
The use of injection molding in different industries allows parts to be produced quickly and accurately in large quantities. The injection molding process is a complex process involving mould design, mould manufacturing, raw material characteristics and raw material pre-treatment methods, molding process, injection molding machine operation and other factors, and is closely related to the processing environmental conditions, cooling time of the product, post-treatment process. Therefore, the quality of the product does not only depend on the injection precision of the injection molding machine, the metering precision, or only by the advantages and disadvantages of the mould design and the precision level of the mould processing, usually, it will also be affected by the influence and constraints of the other factors.
Featured Product
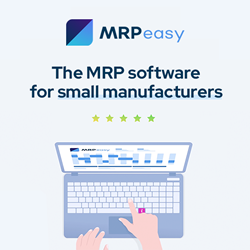
MRPeasy - ERP for Small Manufacturers That Delivers Results
Always know what you have in stock and what you'll need to fulfill orders. Never forget to order parts on time or fail to notice a late delivery from your vendor. Easily create manufacturing orders and schedule them automatically according to resource availability or delivery deadline. Generate accurate cost and lead time estimates and provide customers with quick quotes. Receive notifications when orders are late or inventory levels reach a critical point. Ensure seamless communication between sales, production, warehousing, procurement, administration, and finance. Integrate with popular accounting, CRM, and e-commerce apps. MRPeasy is an ERP software for small manufacturers that gives you all that and more. Our users report a 54% average improvement in the overall performance of their business and a 42% increase in on-time deliveries. Try for free, no credit card needed.