Predictive Maintenance in Manufacturing with AI and IoT Integration
The power of AI and IoT to minimize downtime, optimize equipment performance, and enhance operational efficiency. By analyzing real-time data, these technologies predict potential failures, enabling proactive maintenance and reducing costs
The manufacturing industry is an important factor in terms of the production of products or other daily necessities. There is a lot of machinery that makes manufacturing easy and fast to maintain the balance between demand and output. While the manufacturing industry established a strong global place, modern machinery as value added in the manufacturing market is projected to amount to US$13.6tn in 2024 with a compound annual growth rate of 1.43% expected (CAGR 2024-2029).
Types of machinery are in large amounts and big that need proper maintenance at the right time. However, maintenance is one of the major problems for the manufacturing industry, as conventional maintenance methods cannot help too much. This is not possible for early detection of faults that could avoid large damages and downtime for the manufacturing industry. Many powerful tools and technologies can be implemented or have been implemented by companies to enable predictive maintenance features for the manufacturing industry. AI and IoT solutions are the most capable technologies, and their integration can be a deadly combo to get predictive maintenance for the manufacturing industry.
Overview
AI can analyze data, patterns, decision-making ability, etc., whereas, on the other hand, IoT can gather data, real-time monitoring, detection, data exchanging, etc. These two technologies prove that they are the two sides of one coin. AI and IoT integration can enable predictive maintenance in manufacturing as they enable monitoring, data collection, analysis of error patterns, analysis of past history of faults, instant decision-making for maintenance, etc., which are definitely going to prove an incredible aspect for the manufacturing industry.
AI has been integrated into IoT for a very long time, as the AI in the IoT market is projected to reach a value of USD 201.3 billion by the year 2033, growing at a compound annual growth rate (CAGR) of 19.72% from 2024 to 2033. In 2023, the market was valued at USD 33.2 billion. These numbers are going to grow bigger in the upcoming years as these two technologies have the potential to provide a lot of benefits.
We have gone through the introductory part of the article and have an initial idea of what we are going to discuss in the upcoming part. In the end, we will sign off with a concluding paragraph that will give us a better idea from our perspective.
What is Predictive Maintenance in Manufacturing?
Predictive maintenance generally refers to an operation or process that can be enabled by monitoring and early detection of faults to provide maintenance as soon as possible. With the implementation of AI and IoT, predictive maintenance in manufacturing examines data from processes and equipment to spot any problems before they happen. Predictive maintenance helps the manufacturing industry to shift from a reactive to a predictive, proactive, and highly aligned attitude with efficiency and profitability goals by combining IoT sensors, AI-driven analytics, and big data.
Benefits of AI and IoT Integration while Implementing Predictive Maintenance
Let's see the benefits of AI and IoT integration while implementing predictive maintenance. Some key benefits are mentioned below.
Pattern recognition
To avoid faults and enable predictive maintenance, it is important to detect the pattern that is not easy without any specific solutions. With the integration of IoT and AI, it is possible to gather data with IoT and, on the other hand, possible to analyze patterns of data. This provides the pattern insights, and any unusual activity in the pattern can be detected to establish predictive maintenance.
Maintenance scheduling
Maintaining machinery is just a matter, as it also matters that machinery should be timely maintained. Too early maintenance or too late maintenance of machines could be lost for the manufacturing organizations. With the integration of AI and IoT, it is possible to get a proper schedule for maintenance that avoids unnecessary maintenance. This overall improves cost efficiency for the manufacturing organization.
Real-time feedback mechanism
Feedback always plays a crucial part in making improvements. The integration of AI and IoT not only enables predictive maintenance but also provides a feedback mechanism to the system. AI can analyze IoT sensors, and if any fault reading is detected, then it instantly warns the organization. This enables them to replace the sensors or work on sensors to make accurate predictive maintenance.
Remote monitoring
There are maintenance teams in each manufacturing organization that cannot stay in every place at a time. But if they can get the idea before a fault, then they could have enough time to make maintenance. The integration of AI and IoT can enable remote monitoring, as teams can keep eyes that make them prepare to prevent faults or cure within the time.
Historical data analysis
Real-time data monitoring and analysis are crucial in predictive maintenance, but analysis of past historical data is also important. Past data provides an accurate pattern of past failures. IoT's ability to exchange data and AI's ability to analyze can provide insights related to failure patterns. This also helps to make predictive maintenance and decision-making accurate.
Challenges With The Integration Of AI And IoT
In the last paragraph, we have seen some interesting benefits; now it's time to focus on some challenging parts. Here are a few key challenges mentioned below.
- Data management is a major issue, as IoT generates vast amounts of data that would not be an easy task to analyze.
- There are not too many skilled workers who should have expertise in IoT and AI both, and this could make it difficult to decide where and which devices should be implemented.
- Device interoperability can be one of the major issues, as maybe not every device can be compatible with others.
Final Words
AI and IoT are too capable and powerful individually, and their integration can be the game changer for different operations, especially for predictive maintenance. IoT has the potential to work on different operations related to data, like gathering, exchanging, and monitoring, that could be implemented for machinery. Where AI potential to analyze data can analyze data gathered with IoT to make insights and decision-making on timely and accurate maintenance.
There are a few challenges too, like interoperability issues, skill gaps, cost, data overload, lack of standards, etc., but it is definitely a worthy combination of technology once implemented. Overall, the integration of IoT and AI can result in evolution for predictive maintenance in the manufacturing industry.
Featured Product
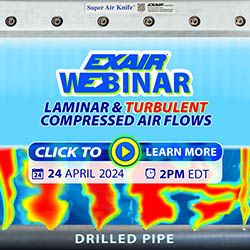