Key Benefits Of CNC Milling In Small Business Manufacturing
CNC milling allows businesses to automate production, reduce waste, and maintain high standards of quality—all of which are critical for small businesses aiming to scale up and compete. Here's a look at the key benefits of using CNC milling in small business manufacturing and why it's a worthwhile investment.
1. Improved Precision and Consistency
With CNC milling, you don't have to worry about inconsistencies between batches. Once a program is set up, the machine can produce hundreds or even thousands of identical parts without deviation. This level of consistency not only improves product quality but also builds customer trust and brand reputation for small businesses.
2. Faster Production Times
Time is a valuable resource for any business, especially for small manufacturers with limited manpower and machinery. CNC milling can significantly speed up the production process by automating tasks that would otherwise require manual intervention. This automation minimizes the time needed to complete each project, allowing for faster turnaround times and enabling small businesses to meet customer deadlines more effectively.
Because CNC milling machines can run continuously with minimal supervision, businesses can maximize production output during off-hours, such as nights and weekends. This capability can be a game changer for small businesses trying to increase capacity without hiring additional staff, effectively increasing productivity without added labor costs.
3. Cost-Effectiveness
While CNC milling machines may represent an upfront investment, they can help small businesses save money in the long run. CNC milling's high precision reduces the likelihood of errors, minimizing the need for rework and material waste. By reducing waste, CNC milling lowers material costs, which can significantly impact profitability for small businesses operating on tight margins.
Moreover, since CNC milling requires fewer hands-on operations, labor costs can also be reduced. CNC operators can set up a machine and monitor multiple machines simultaneously, further reducing the number of employees needed for production. Overall, CNC milling allows small businesses to optimize their resources and allocate their budget more effectively.
4. Versatility and Flexibility
CNC milling machines are highly versatile and can be used to manufacture a wide range of products from various materials, including metals (such as aluminum, steel, and titanium), plastics, wood, and more. This flexibility is especially valuable for small businesses that need to produce a diverse set of parts for different customers or industries.
Additionally, CNC machines can easily switch between different product designs and prototypes. With a quick software adjustment, the machine can be reprogrammed to produce different components, allowing small businesses to pivot quickly to meet changing customer demands. This adaptability helps small manufacturers stay competitive in a rapidly changing market and respond to custom orders with ease.
5. Ease of Prototyping and Innovation
Innovation is crucial for small businesses that need to differentiate themselves from larger competitors. CNC milling is an ideal tool for rapid prototyping, allowing companies to develop and test new designs quickly and efficiently. Engineers and designers can create digital prototypes using CAD (Computer-Aided Design) software, which can then be sent to a CNC mill for a physical prototype within hours.
This rapid prototyping capability enables businesses to iterate on their designs without significant delays, making it easier to perfect products before they reach production. With CNC milling, small businesses can innovate faster, bring products to market more rapidly, and reduce the risk of costly design errors.
6. Scalability and Future Growth Potential
CNC milling supports scalability, which is essential for small businesses with ambitions to grow. As demand for a product increases, businesses can scale up production without compromising quality or requiring significant investments in new machinery. CNC milling's ability to handle both low- and high-volume production runs means that small businesses can serve their current customer base effectively while being ready for future expansion.
Additionally, the skills and technologies associated with CNC milling are widely applicable, which means that as the business grows, it's relatively easy to scale operations with additional machines and more advanced CNC equipment. CNC milling provides a foundation for long-term growth, enabling small businesses to expand their manufacturing capabilities without overhauling their entire production system.
7. Reduced Dependence on Skilled Labor
One of the challenges facing small businesses in manufacturing is finding skilled labor. CNC milling helps address this issue by reducing the dependency on highly skilled machine operators. While CNC operators do require training, the skillset needed to operate CNC milling machines is more accessible compared to the expertise required for traditional machining methods.
Once the machine is programmed, the operator can oversee its functioning and ensure that everything is running smoothly, with minimal intervention. This reduction in labor-intensive processes helps small businesses control labor costs and reduces the risk of production delays due to labor shortages.
8. Enhanced Safety in the Workplace
Safety is a significant concern for any manufacturing environment, and CNC milling contributes to a safer workplace. Since CNC milling machines are automated, there is less direct human involvement in the cutting process, reducing the risk of injury. Operators can set up the machine, input the necessary parameters, and monitor it from a safe distance, minimizing their exposure to sharp tools, heat, and flying debris.
For small businesses that may not have extensive resources for workplace safety programs, CNC milling can provide a safer alternative to manual machining. By investing in CNC milling, businesses can create a safer work environment for their employees, resulting in fewer accidents and a more positive workplace culture.
Conclusion
CNC milling offers numerous advantages for small business manufacturing, including precision, speed, cost savings, flexibility, and scalability. For small businesses aiming to improve their production capabilities and stay competitive, CNC milling provides a reliable solution that boosts efficiency and opens up new opportunities for growth.
By adopting CNC milling, small businesses can not only improve product quality but also position themselves to take on more complex and diverse projects, ultimately driving success in today's dynamic market. Whether for prototyping, small batch production, or high-volume runs, CNC milling can be a transformative investment, allowing small manufacturers to deliver high-quality products, streamline operations, and enhance customer satisfaction.
Featured Product
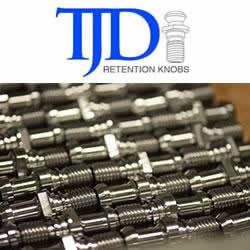
T.J. Davies' Retention Knobs
Our retention knobs are manufactured above international standards or to machine builder specifications. Retention knobs are manufactured utilizing AMS-6274/AISI-8620 alloy steel drawn in the United States. Threads are single-pointed on our lathes while manufacturing all other retention knob features to ensure high concentricity. Our process ensures that our threads are balanced (lead in/lead out at 180 degrees.) Each retention knob is carburized (hardened) to 58-62HRC, and case depth is .020-.030. Core hardness 40HRC. Each retention knob is coated utilizing a hot black oxide coating to military specifications. Our retention knobs are 100% covered in black oxide to prevent rust. All retention knob surfaces (not just mating surfaces) have a precision finish of 32 RMA micro or better: ISO grade 6N. Each retention knob is magnetic particle tested and tested at 2.5 times the pulling force of the drawbar. Certifications are maintained for each step in the manufacturing process for traceability.