Gulf Wind Technology Leverages Stratasys 3D Printing to Accelerate Innovation in Wind Turbine Design
Additive Manufacturing Enables Faster Prototyping and Unique Design Capabilities for Wind Tunnel Models
Stratasys Ltd. (NASDAQ: SSYS) today announced that Gulf Wind Technology, a company dedicated to advancing rotor design for wind turbines, is using Stratasys additive manufacturing solutions to enhance their ability to test and improve wind turbine models. Gulf Wind Technology's implementation of Stratasys technologies showcases the unique advantages of additive manufacturing alongside traditional methods, offering significant improvements in design iteration turnaround time and flexibility.
By adopting Stratasys Neo® stereolithography (SLA) technology, Gulf Wind Technology has dramatically reduced the design and fabrication cycle for wind tunnel models. What previously took 30 to 40 days to iterate and finalize a design can now be completed in just 3 to 4 days. The technology also allows for specialized features such as pressure taps for real-time airflow data, which are difficult or impossible to execute with conventional manufacturing methods.
"By leveraging the Stratasys Neo® SLA system we can generate far more data in a shorter time. This has enabled us to run our design process with more rigor, become more efficient, and take on business that we previously had to turn away," said James Martin, CEO of Gulf Wind Technology. "Additive manufacturing allows our engineers to design internal structures, and pressure taps directly into our test models, which we couldn't achieve with traditional methods."
Rich Garrity, Chief Business Unit Officer at Stratasys, added, "Our work with Gulf Wind Technology demonstrates how manufacturers are adopting additive manufacturing where it makes the most sense for their business. By leveraging its unique advantages, Gulf Wind Technology can rapidly prototype and test complex designs, greatly improving their efficiency and ability to innovate. This is a perfect example of how 3D printing is expanding its place on the manufacturing floor alongside traditional methods."
The technical capabilities of 3D printing have been essential to Gulf Wind Technology's rotor design process. Using Stratasys Neo® SLA technology, Gulf Wind Technology can produce models with Somos® PerFORM Reflect™ material, which offers high strength, stiffness, and temperature resistance - critical attributes for wind tunnel testing. Due to the superior attributes of the resin, the printed parts post process and handling is simple and straight forward - from removal of support materials, to cleaning resin from internal channels to placement in a wind tunnel.
Inspired by the use of 3D printing in Formula 1 racing, Gulf Wind Technology's engineers recognized the potential for rapid iteration and optimization in wind turbine design. With Stratasys' solutions, Gulf Wind Technology can test airfoil shapes and rotor designs faster than ever, allowing them to maximize wind energy efficiency for applications in the Gulf of Mexico.
About Stratasys
Stratasys is leading the global shift to additive manufacturing with innovative 3D printing solutions for industries such as aerospace, automotive, consumer products, and healthcare. Through smart and connected 3D printers, polymer materials, a software ecosystem, and parts on demand, Stratasys solutions deliver competitive advantages at every stage in the product value chain. The world's leading organizations turn to Stratasys to transform product design, bring agility to manufacturing and supply chains, and improve patient care.
To learn more about Stratasys, visit www.stratasys.com, the Stratasys blog, X/Twitter, LinkedIn, or Facebook. Stratasys reserves the right to utilize any of the foregoing social media platforms, including Stratasys' websites, to share material, non-public information pursuant to the SEC's Regulation FD. To the extent necessary and mandated by applicable law, Stratasys will also include such information in its public disclosure filings.
Featured Product
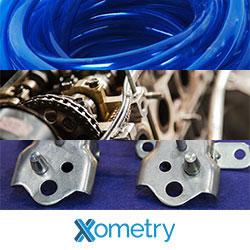