The Future of Industrial Automation: How Software is Revolutionizing Manufacturing Processes
In today's fast-paced manufacturing landscape, industrial automation is no longer a luxury, but a necessity. The future of industrial automation lies in the hands of innovative software solutions that are revolutionizing manufacturing processes. From robotics and artificial intelligence to machine learning and data analytics, these technologies are transforming the way companies operate, boosting productivity, efficiency, and profitability like never before. With the integration of intelligent software systems, manufacturers can streamline their operations, reduce costs, minimize human error, and enhance overall production quality. Real-time data monitoring and analysis allow for proactive maintenance, eliminating costly and unexpected equipment downtime. Moreover, predictive analytics and advanced algorithms enable businesses to optimize inventory levels, identify market trends, and make agile decisions. The future of industrial automation is all about harnessing the power of software to create smarter and more agile manufacturing processes. By leveraging innovative technologies, companies can stay ahead of the competition, respond quickly to market demands, and drive sustainable growth. In this article, we will explore the exciting possibilities that lie ahead and delve into how software is shaping the future of industrial automation.
Evolution of Industrial Automation
The journey of industrial automation began with the advent of mechanization in the late 18th century, driven by the Industrial Revolution. Initially, industries relied on simple machines powered by water or steam to enhance productivity. As time progressed, the introduction of electrical power marked a significant shift, allowing for more complex machinery and processes. This transformation laid the groundwork for early automation, where specific tasks could be performed with higher efficiency and less manual labor. Over the decades, the integration of electronics and computer technology further propelled the industry forward, paving the way for automated systems that could execute repetitive tasks with precision.
In the late 20th century, the rise of programmable logic controllers (PLCs) revolutionized manufacturing processes. These compact devices allowed for the automation of machinery in a more flexible and programmable manner. Factories could now modify their operations without extensive rewiring or mechanical changes. This era marked a significant shift from purely mechanical systems to a more integrated approach, blending hardware and software. As a result, industries began to embrace automation not just for efficiency but also for adaptability, enabling them to respond to changing market demands quickly.
Entering the 21st century, the focus on automation has shifted towards smart manufacturing, driven by advancements in information technology. The Internet of Things (IoT) has emerged as a game-changer, connecting machines and systems to collect and analyze vast amounts of data in real-time. This evolution has led to the development of cyber-physical systems, where physical processes are monitored and controlled by computer-based algorithms. Today, the future of industrial automation is intertwined with software solutions that enable manufacturers to optimize operations, enhance decision-making, and ultimately create a more agile production environment.
Importance of Software in Industrial Automation
Software plays a pivotal role in the realm of industrial automation, serving as the backbone that supports the integration of various technologies and processes. At its core, software facilitates communication between machines, systems, and human operators. This connectivity is essential for achieving seamless operations and ensuring that all components within a manufacturing ecosystem work in harmony. Without robust software solutions, the potential of automation remains largely untapped, as manufacturers would struggle to coordinate complex processes and manage vast amounts of data.
Furthermore, the importance of software in industrial automation extends to data analysis and decision-making. Advanced analytics tools enable manufacturers to gather insights from real-time data, allowing for informed decisions that drive operational efficiency. Predictive maintenance software, for instance, analyzes equipment performance and predicts potential failures before they occur, minimizing downtime and reducing maintenance costs. This proactive approach not only enhances productivity but also fosters a culture of continuous improvement within organizations.
Lastly, software enhances the overall flexibility and scalability of manufacturing processes. As market demands fluctuate, manufacturers can quickly adapt their operations by reprogramming software rather than overhauling physical systems. This agility is crucial in today's fast-paced environment, where the ability to respond rapidly to customer needs can provide a competitive advantage. In essence, software is not just an adjunct to industrial automation; it is a critical enabler that transforms the way manufacturers operate, innovate, and succeed.
Advantages of Software-Driven Manufacturing Processes
One of the most significant advantages of software-driven manufacturing processes is the dramatic increase in efficiency. Automation systems powered by intelligent software can operate continuously, performing tasks at speeds and accuracies that far exceed human capabilities. This efficiency translates to higher production rates, reduced lead times, and improved overall throughput. When manufacturers can produce goods faster and with fewer errors, they not only enhance their bottom line but also improve customer satisfaction by delivering products on time and within specifications.
In addition to enhanced efficiency, software-driven processes contribute to cost savings. By automating routine tasks and optimizing workflows, companies can significantly reduce labor costs and minimize waste. Software solutions can analyze resource usage and identify areas for improvement, enabling manufacturers to make data-driven decisions that lead to more economical operations. Moreover, with predictive analytics in place, organizations can anticipate maintenance needs and avoid costly equipment failures, further enhancing their financial health.
Another key advantage is the improved quality of products manufactured through automated processes. Software systems can implement consistent quality control measures, ensuring that each product meets stringent standards. By utilizing machine learning algorithms, manufacturers can identify defects and anomalies in real-time, allowing for immediate corrective actions. This meticulous attention to quality not only enhances the reputation of the brand but also fosters customer loyalty, as consumers increasingly seek reliable and high-quality products in a competitive marketplace.
Key Technologies Driving the Future of Industrial Automation
Several key technologies are at the forefront of driving the future of industrial automation, each playing a vital role in reshaping manufacturing processes. One of the most influential technologies is artificial intelligence (AI). AI algorithms enable machines to learn from data and make autonomous decisions, enhancing their ability to adapt to changing conditions. For example, AI can optimize production schedules based on real-time demand, ensuring that resources are allocated efficiently. This capability not only boosts productivity but also reduces waste, making manufacturing processes more sustainable.
Another transformative technology is the Internet of Things (IoT), which connects machines, sensors, and systems to the internet, facilitating real-time data exchange. IoT devices can monitor equipment performance, environmental conditions, and production metrics, providing valuable insights that inform decision-making. With IoT-enabled automation, manufacturers can achieve greater visibility into their operations, enabling them to respond quickly to any issues that arise. This interconnectedness creates a more resilient manufacturing ecosystem, reducing the risk of disruptions and enhancing overall efficiency.
Additionally, robotics continues to play a crucial role in the evolution of industrial automation. Advanced robotic systems, equipped with sophisticated sensors and AI capabilities, can perform complex tasks with precision and speed. Collaborative robots, or cobots, are designed to work alongside human operators, augmenting their capabilities and enhancing productivity. This synergy between humans and machines represents a significant shift in manufacturing, allowing for more flexible and adaptive production environments. As these technologies continue to evolve, their integration into manufacturing processes will redefine efficiency and innovation in the industry.
Case Studies Showcasing the Impact of Software in Manufacturing
To illustrate the transformative power of software in industrial automation, several case studies highlight successful implementations across various sectors. One notable example is a leading automotive manufacturer that adopted a comprehensive software solution to streamline its assembly line processes. By integrating real-time data analytics and machine learning, the company was able to identify bottlenecks and optimize workflows, resulting in a 30% increase in production efficiency. This shift not only reduced operational costs but also improved product quality, leading to higher customer satisfaction and increased market share.
Another compelling case involves a food processing company that implemented a software-driven inventory management system. By leveraging predictive analytics, the company optimized its supply chain, ensuring that raw materials were available when needed without overstocking. This proactive approach minimized waste and reduced storage costs, allowing the company to allocate resources more effectively. As a result, the manufacturer reported a significant reduction in operating expenses and improved profit margins, demonstrating the financial benefits of adopting advanced software solutions.
In the electronics manufacturing sector, a global leader utilized advanced robotics and AI-powered software to enhance its production capabilities. The company introduced smart machines capable of self-diagnosing issues and adjusting operations in real-time. By employing these technologies, the manufacturer increased its production speed while maintaining high-quality standards. The successful integration of automation not only improved efficiency but also positioned the company as a leader in innovation, enabling it to stay ahead in a highly competitive market.
Challenges and Risks Associated with Software-Driven Automation
Despite the numerous advantages of software-driven automation, several challenges and risks must be considered by manufacturers. One primary concern is the potential for cybersecurity threats. As manufacturing processes become increasingly reliant on interconnected systems and IoT devices, the risk of cyberattacks grows. A breach could lead to unauthorized access to sensitive data, disruption of operations, or even damage to equipment. Manufacturers must invest in robust cybersecurity measures to protect their systems and ensure the integrity of their operations.
Another challenge lies in the integration of new software solutions with existing systems. Many manufacturers operate on legacy systems that may not be compatible with modern software technologies. This incompatibility can lead to significant hurdles during the implementation phase, resulting in increased costs and extended timelines. It is essential for organizations to carefully assess their current infrastructure and develop a comprehensive integration strategy that minimizes disruptions and maximizes the potential benefits of automation.
Moreover, the rapid pace of technological change presents a risk of obsolescence. As new software solutions and automation technologies emerge, manufacturers may find themselves struggling to keep up with the latest advancements. This constant evolution requires a commitment to ongoing training and development for employees to ensure they possess the necessary skills to operate and maintain new systems. Companies that fail to prioritize workforce development may encounter significant challenges in reaping the full benefits of their automation investments.
How to Integrate Software into Existing Manufacturing Processes
Integrating software into existing manufacturing processes requires a strategic and systematic approach to ensure a seamless transition. The first step is to conduct a thorough assessment of current operations and identify areas that could benefit from automation. This analysis should involve evaluating workflows, equipment performance, and data management practices. By pinpointing specific pain points, manufacturers can develop targeted solutions that address their unique challenges and goals.
Next, it is crucial to select the right software solutions that align with the organization's objectives. Manufacturers must consider factors such as scalability, compatibility with existing systems, and ease of use when evaluating potential software options. Collaborating with technology partners who possess industry expertise can provide valuable insights and guidance during this selection process. A well-chosen software solution can significantly enhance operational efficiency and drive overall productivity.
Once the software solution has been selected, it is essential to develop a comprehensive implementation plan. This plan should outline the necessary steps for integrating the software into existing processes, including timelines, resource allocation, and training requirements. Engaging employees early in the process can foster a culture of collaboration and ensure that team members are equipped with the knowledge and skills to effectively utilize the new system. By prioritizing communication and support throughout the integration process, manufacturers can minimize disruptions and maximize the benefits of software-driven automation.
Training and Education Opportunities for the Future of Industrial Automation
As the landscape of industrial automation evolves, so too does the need for a skilled workforce equipped to navigate new technologies. Manufacturers must prioritize training and education to ensure that employees possess the necessary competencies to operate advanced software systems. This commitment to workforce development not only enhances productivity but also fosters employee engagement and retention, as individuals feel valued and empowered in their roles.
One effective approach to training is the implementation of continuous learning programs that provide employees with opportunities to acquire new skills and knowledge. These programs can encompass a range of formats, including on-the-job training, workshops, online courses, and partnerships with educational institutions. Manufacturers should encourage employees to pursue certifications in relevant technologies, such as IoT, AI, and data analytics, to bolster their expertise and keep pace with industry advancements.
Moreover, fostering a culture of innovation within the organization can significantly enhance the effectiveness of training initiatives. Encouraging employees to experiment with new software solutions and providing platforms for knowledge sharing can lead to valuable insights and improvements in processes. By cultivating an environment that embraces learning and adaptability, manufacturers can position themselves for long-term success in an increasingly automated and technology-driven world.
Conclusion: Embracing the Software Revolution in Manufacturing
The future of industrial automation is undeniably tied to the advancements in software technology that are reshaping manufacturing processes. As companies continue to adopt intelligent solutions, the benefits of increased efficiency, reduced costs, and improved product quality become increasingly apparent. Embracing this software revolution enables manufacturers to stay competitive in a rapidly evolving marketplace, where agility and innovation are paramount.
However, the journey toward successful automation requires careful planning and a commitment to continuous improvement. By addressing the challenges and risks associated with software integration, manufacturers can unlock the full potential of their operations. Investing in training and education ensures that the workforce is equipped to navigate this new landscape, fostering a culture of collaboration and innovation.
Ultimately, the future of industrial automation lies in the harmonious interplay between technology, data, and human expertise. As manufacturers harness the power of software to drive their operations, they will not only enhance productivity and profitability but also pave the way for a more sustainable and resilient manufacturing ecosystem. Embracing this transformation is not just an option; it is a necessity for those seeking to thrive in the dynamic world of manufacturing.
Featured Product
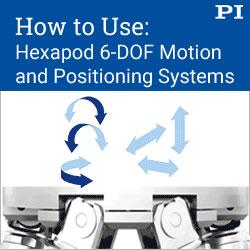