ABB Robotics and US start-up Molg tackle data center e-waste with robotic micro-factories
● ABB Robotics and Molg will create robotic micro factories for data center server disassembly and component recovery ● Collaboration tackles electronic waste (e-waste) production, projected to rise to 75 million tons by 20301 ● Automated disassembly and recovery addresses environmental and regulatory demands as well as worker welfare
ABB Robotics is collaborating with US start-up Molg to create robotic micro-factories to recover and recycle data center operators' disused electronic equipment, commonly known as e-waste. With global e-waste projected to rise to 75 million tons by 2030[1], the micro-factories will play a vital role in reducing the electronic waste, helping the data center sector operate more efficiently and sustainably.
Advances in computing such as AI, machine learning and the cloud necessitate the need for data centers to upgrade and expand their facilities more frequently. Today, data centers are major contributors to the 2.6 million tonnes of e-waste generated worldwide each year.2
ABB Robotics continues to support innovation ecosystems through collaboration and venture capital investments. ABB Robotics & Automation Ventures (ABB RA Ventures) participated with an investment in Molg's seed round led by Closed Loop Partners' Ventures Group, alongside Amazon's Climate Pledge Fund, Overture, Elemental Impact and Techstars Ventures.
Molg was recognized as a winner by ABB's Motion drive business in its ABB Accelerating Circularity Startup Challenge 2023, Molg's robotic micro-factory can autonomously assemble and disassemble complex electronic products including laptop PCs, servers, and industrial electronics.
As an alternative to manual disassembly, or sending equipment to landfill or incineration, the micro-factory solves many of the challenges associated with the disposal of electronic waste. With end users facing increasing regulations regarding the responsible handling of de-commissioned equipment[3], automated disassembly reduces the risks associated with handling toxic elements that can damage the environment and human health, and releases workers from handling arduous and potentially dangerous tasks.
With many components also containing rare earth elements (REEs), the ability to maximize their recovery through automation also provides an economic opportunity to reuse them in the production of new electronic equipment.
The micro- factory solution is aimed at hyperscalers operating large networks of data centers and IT Asset Disposition (ITAD) companies.
"We are excited to have the support of ABB, a global leader in robotics and automation, as we continue pushing the boundaries of what is possible in circularity and automation," said Rob Lawson-Shanks, CEO & Co-Founder of Molg. "With this investment from ABB, we can accelerate our work to create more sustainable, circular manufacturing processes for electronics that ensure valuable materials are kept in circulation and enhance supply chain resilience."
The solution is part of Molg's wider portfolio that includes design-for-circularity and component traceability software tools enabling manufacturers to create products that can be easily de-manufactured and recycled at the end of their life.
ABB is a technology leader in electrification and automation, enabling a more sustainable and resource efficient future. The company's solutions connect engineering know-how and software to optimize how
things are manufactured, moved, powered and operated. Building on over 140 years of excellence, ABB's
more than 105,000 employees are committed to driving innovations that accelerate industrial
transformation. www.abb.com
ABB Robotics & Automation Ventures (ABB RA Ventures) is the business-led strategic venture capital unit of ABB Robotics & Discrete Automation, part of ABB's corporate venture capital framework: ABB Ventures. Since its formation in 2009, ABB Ventures has invested around $500 million in startups with a close fit to its electrification, robotics, automation, and motion businesses. For more information, visit www.abb.com/ventures
Molg
Molg tackles the growing e-waste problem by making manufacturing circular. The company's robotic microfactory can autonomously disassemble complex electronic products like laptops and servers, helping keep valuable components and materials within supply chains and out of landfills. Molg partners with leading electronics manufacturers to design the next generation of products with reuse in mind, ensuring that one product's end is another's beginning. To learn more, visit molg.ai.
Featured Product
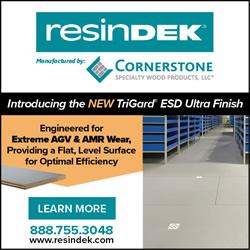