Jamco America Partners with Airtech for 3DP Tool Recycling
Leading aerospace manufacturer joins forces with composite materials expert to pioneer sustainable manufacturing practices
Everett, WA - Jamco America, Inc., one of the most experienced interior products suppliers and turnkey aircraft interiors integrators in the aerospace industry, is pleased to announce its partnership with Airtech Advanced Materials Group, a global leader in composite manufacturing consumables and supporting materials, to revolutionize aerospace manufacturing through 3D printing (3DP) tool recycling. The partnership enables faster production of finished goods with reduced risk and cost and a lower total carbon footprint. By embracing sustainable products and practices, Jamco and Airtech are pioneering a new era of environmentally conscious aerospace manufacturing.
The partnership between Jamco and Airtech began in 2006, with Airtech supplying composite manufacturing consumables and supporting materials to Jamco. In 2021, the collaboration expanded into large-format additive manufacturing (LFAM) tooling. Jamco's goal is to explore LFAM technology for high-temperature applications, aiming to overcome the limitations of traditional composite layup tooling. This promises to significantly reduce lead times and supply chain delays while enhancing performance and reducing the risk of defects in finished parts.
The LFAM molds produced by Airtech utilize Airtech's Dahltram I350CF thermoplastic resin, a fully recyclable polymer. Depending on the application's requirements, Airtech can grind up and compound this resin into a blended or 100% recycled formulation. Ongoing testing at Airtech aims to validate the best blended formulations for high-performance applications such as aerospace tooling and molds.
Through this innovative partnership, Jamco and Airtech aim to revolutionize aerospace manufacturing and enhance product quality, reduce lead times, lower production costs, and minimize environmental impact, thus ensuring greater sustainability, cost-effectiveness, and safety across the industry.
About Jamco America
Jamco America, a subsidiary of Jamco Corporation in Japan, was established in 1982 as a commercial aircraft interior products and services provider. Located in Everett, WA, Jamco is considered one of the most experienced interior products suppliers and turnkey aircraft interiors integrators in the industry and holds 70+% of all Supplemental Type Certificates issued for 777. Jamco has developed premium class seating for commercial aircraft, providing oblique facing business class seating such as the Venture™ reverse herring-bone business class seat that is currently in service on 787 and 777 aircraft. For more information, visit https://www.jamco-america.com/.
About Airtech
Airtech Advanced Materials Group is the largest privately-owned manufacturer of vacuum bagging and composite tooling materials for prepreg/autoclave, resin infusion, and wet lay-up processes up to 799°F (426°C). Established in 1973, Airtech is a family-owned and operated business, committed to preserving its core values and leading industry innovations for over 50 years. Airtech serves a diverse range of sectors, including aerospace, wind energy, solar, marine, automotive, and general composites. The company's latest advancements in large-scale additive manufacturing, advanced Dahltram® tooling, and multi-purpose thermoplastic resins demonstrate Airtech's commitment to innovation and sustainable practices. The Airtech Advanced Materials Group encompasses Airtech International Inc. in the USA (Huntington Beach, CA; Chino, CA; Springfield, TN), Airtech Europe Sarl (Differdange, Luxembourg), Airtech Advanced Materials UK (Chadderton, England), Airtech Asia (Tianjin, China), and Airtech India (Goa, India). Airtech's global footprint provides access to resources and markets worldwide, while the company maintains a strong commitment to a community-focused approach in each region it operates.
Featured Product
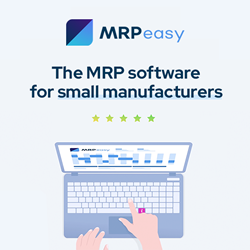