How RpProto Bridges the Gap Between Design and Manufacturing.
Bringing a product to market may be a lengthy process. Even if you have the perfect design on paper, translating it into a practical thing is a significant leap. One cannot just give over a plan to a manufacturer and hope that everything works out perfectly. The gap between design and production is large, and it includes determining exactly how the design should and should be made before putting it in the hands of the manufacturer. Make the plunge too soon and with insufficient planning, and the consequences might be disastrous. If key responsibilities are delegated to a non-expert, the product's prospects of success may suffer.
Bringing a product to market may be a lengthy process. Even if you have the perfect design on paper, translating it into a practical thing is a significant leap. One cannot just give over a plan to a manufacturer and hope that everything works out perfectly.
The gap between design and production is large, and it includes determining exactly how the design should and should be made before putting it in the hands of the manufacturer. Make the plunge too soon and with insufficient planning, and the consequences might be disastrous. If key responsibilities are delegated to a non-expert, the product's prospects of success may suffer.
RpProto, an international prototype firm situated in Xiamen, specializes in bridging the gap between design and manufacturing. RpProto specializes in a wide range of prototype services, from CNC machining to injection molding and everything in between, and knows how to turn a concept into a product that is ready for production.
While RpProto is very adept with its technology, bridging the gap between design and manufacture entails more than merely passing material through a CNC mill. When RpProto gets a design, the business examines how it should be built, investigates material options, and discusses the product's manufacturability in terms of budget, planned numbers, and other aspects.
Only then can the design be translated into a production-ready product, and only then can the gap be closed.
Bridging the gap with prototypes
Prototypes are pre-production models of a product. They may be used for a variety of objectives, including demonstrating a product's feasibility to investors, putting it to the test in a functional capacity, and seeing how it looks. They are regarded a must for almost all physical items.
Prototypes can be used to achieve numerous tasks: First, the prototyping team may determine if the design can be made in the manner originally intended; if not, it can make necessary changes in preparation for the prototype. After this step is completed, the prototype team can examine various production techniques, configurations, and materials for the product. RpProto provides a wide range of prototyping choices.
CNC machining
RpProto's fleet of CNC machining centers, which includes 5-axis, 4-axis, and 3-axis machines, can produce prototypes of any type to the strictest tolerances. CNC milling and turning technologies may be used to manufacture items from scratch or to add features to existing goods, while a variety of material and finishing options enable firms to maximize their product.
CNC machining is a popular production procedure for end-use items, therefore a CNC machined prototype can provide a good indicator of a product's feasibility. Because the procedure is not duplicative, it is perfect for one-off prototypes.
Casting, tooling, and molding
In addition to CNC machining, RpProto provides a variety of casting, tooling, and molding methods that may be used to make prototypes in higher numbers.
Although vacuum casting is an entirely distinct technique, it is quite similar to CNC machining. To generate vacuum casted prototypes, RpPro first develops a master model on one of its CNC machining machines, which is then used to produce a silicon rubber mold. With this rubber mold, precise reproductions of the original model may be created in a variety of casting polymers.
There are different techniques to make molds. For more demanding projects that need high volume manufacturing or the use of caustic or abrasive polymers, RpProto
RpProto also collaborates with chosen partners to offer pressure die casting services, which enable low-volume production runs of aluminum, magnesium, and zinc products, as well as investment casting in brass and steel.
Prototypes created through the casting and molding processes may assist organizations transition to production in a variety of ways. For example, molded copies can be utilized for engineering testing and other technical operations. However, because they are of great aesthetic quality, they may also serve as showcase demonstrations, assisting firms in obtaining financial support that would pave the way for large-scale manufacturing.
Featured Product
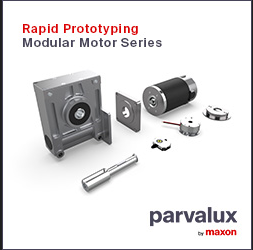