Ergonomic principles play a significant role in enhancing efficiency and reducing the risk of injury. As we move through 2024, these best practices can help you optimize the work environment and foster well-being among your workforce.
How to Implement Best Practice Ergonomics in Manufacturing
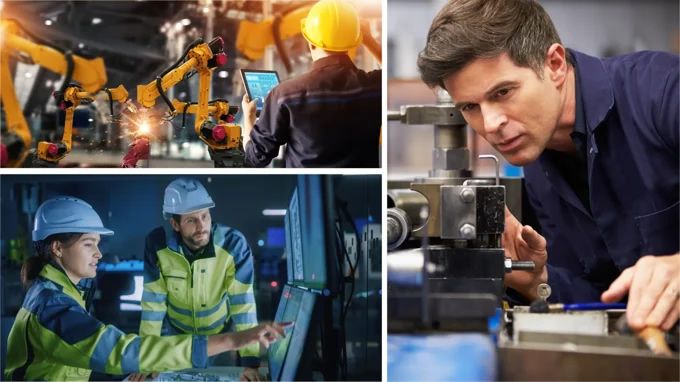
DJ Brown, MBA, MS, ATC, CMMSS, CEAS | Briotix Health
The Role of Ergonomics in Manufacturing
Ergonomics—the scientific discipline that studies human efficiency in work environments—plays a pivotal role in the manufacturing industry. The aim of ergonomics is to design tasks, workspaces, and equipment to fit the employee, thereby reducing risk factors and fostering efficient work postures. This focus on "fitting the job to the worker" can have far-reaching impacts, driving improvements in safety, productivity, and job satisfaction.
The Consequences of Poor Ergonomics in Manufacturing
Poor ergonomics presents a significant challenge in manufacturing environments. It is often characterized by conditions that force workers into awkward postures, mandate heavy lifting, or require extended periods of repetitive motion. These conditions affect worker comfort and can result in musculoskeletal disorders (MSDs). MSDs encompass various inflammatory and degenerative conditions affecting the muscles, ligaments, tendons, and bones. Common MSDs in the manufacturing sector include carpal tunnel syndrome, back pain, and other repetitive strain injuries.
MSDs pose a real and significant threat to productivity and worker health. They can lead to extended absences, diminished productivity, and—in severe cases—permanent disability. Moreover, they contribute to increased healthcare costs and can create a ripple effect, impacting morale and leading to further inefficiencies in the manufacturing environment.
OSHA's Recognition of Ergonomics
The Occupational Safety and Health Administration (OSHA) recognizes the importance of ergonomics in mitigating these risks. As a key component of its mission to ensure safe and healthful working conditions, OSHA promotes implementing ergonomic solutions to prevent workplace injuries. In fact, many of their guidelines directly address ergonomics in manufacturing, emphasizing the need for ergonomic design, regular risk assessments, and appropriate interventions. With recent programs such as the new National Emphasis Program, their commitment to ergonomics has been renewed.
The Impact of Ergonomic Solutions
Implementing ergonomic solutions—such as equipment redesign, workstation modifications, or administrative controls like job rotation—can lead to substantial improvements. These changes not only minimize the risk of injury but also foster a healthier work environment. They can improve workers' comfort, reduce fatigue and strain, and boost job satisfaction. In turn, these improvements often lead to enhanced productivity and a lower incidence of MSDs, creating a win-win situation for employees and employers alike.
In essence, understanding and leveraging the principles of ergonomics is crucial in the manufacturing industry. As we navigate through 2023, it will continue to be an essential factor in maintaining workplace safety, improving manufacturing processes, and enhancing the overall well-being of the workforce.
Emphasizing Ergonomic Workstation Design
The Centrality of Workstations in Manufacturing
Workstations, the hub of activity in any manufacturing process, form the backbone of manufacturing industries. It is here that the workers spend the majority of their time, perform their tasks, and utilize various equipment and tools. Hence, ensuring proper workstation design is an integral part of implementing ergonomics in manufacturing. The criticality of workstation design lies in its potential to directly affect a worker's comfort, safety, and productivity.
The Anatomy of Ideal Workstation Design
The design of an ideal workstation revolves around reducing awkward postures, minimizing heavy loads, and preventing over-exertion. By reducing awkward postures, a well-designed workstation helps alleviate the strain on the worker's body, preventing musculoskeletal disorders and enhancing efficiency. Similarly, reducing heavy loads and overexertion can prevent a range of workplace injuries, including back injuries and other forms of physical strain.
This ideal workstation is adjustable to accommodate a diverse range of body sizes and shapes. It encourages neutral postures and minimizes repetitive motion. All tools and materials should be within easy reach, reducing unnecessary movements, and the workstation should be designed to support both seated and standing postures, depending on the task requirements.
The Influence of Automation on Workstation Design
Automation has been a defining trend in the manufacturing industry in 2023 and continues to reshape the landscape of workstation design. Automation technologies, including robots, conveyors, and lifting aids, can take over tasks that traditionally required heavy lifting or manual material handling, thereby reducing the ergonomic risk for workers.
Robots, for example, can handle repetitive tasks that require precision and speed, thus eliminating the risk of repetitive motion injuries. Conveyors can transport heavy loads across long distances within the factory, reducing the need for manual material handling that could result in overexertion and back injuries. Moreover, the application of lifting aids in the assembly line can help with heavy lifting tasks, thus mitigating the risk of overexertion and back pain.
By leveraging these automation technologies, businesses can significantly reduce the physical demands placed on their workers. In turn, this reduces the risk of ergonomic injuries, improves the overall work environment, and ultimately enhances productivity.
In conclusion, emphasizing ergonomic workstation design in manufacturing processes is a key element in creating safer, more efficient, and more comfortable workplaces. As we move further into 2024, companies that prioritize and effectively implement ergonomic principles in their workstation design will set themselves up for continued success.
Identifying and Reducing Ergonomic Risk
The Inherent Risks in Manufacturing Work
Manufacturing work, by its very nature, often involves tasks that can lead to a range of work-related health issues, including back injuries, cumulative trauma, and musculoskeletal disorders (MSDs). These tasks may involve heavy lifting, handling heavy loads, working in awkward postures, or performing repetitive motions for extended periods.
Recognizing these risk factors is essential in creating an ergonomic work environment. Understanding these risks enables businesses to intervene proactively and design strategies that minimize the possibility of injuries, thus contributing to a safer and more productive work environment.
Role of Self-Assessments in Identifying Ergonomic Risks
Self-assessments play a crucial role in identifying ergonomic risks. With proper training, employees can become more aware of their work postures, interactions with the work environment, and tasks. They can identify risky behaviors that could potentially lead to injuries, such as poor lifting techniques or maintaining awkward postures for extended periods.
For example, an employee might recognize that they often bend their back when lifting heavy objects from the floor, a behavior that could lead to lower back pain or other back injuries. Once they have identified this risky behavior, they can improve their lifting technique, perhaps by using lifting aids or bending their knees and keeping their back straight when lifting.
The Importance of Regular Interventions
Regular interventions are an integral part of an effective ergonomics program. These interventions could involve ergonomic training sessions, workstation redesign, changes in work procedures, or the introduction of ergonomic tools and equipment.
Ergonomic training sessions can educate employees about the principles of ergonomics, the importance of maintaining correct postures, and the benefits of ergonomics in their everyday work. Workstation redesign can adjust workstations to better suit the worker's body size and shape, thus promoting better postures and reducing strain. Changes in work procedures can distribute tasks more evenly, preventing repetitive motion and reducing overexertion. The introduction of ergonomic tools and equipment can help workers perform their tasks more comfortably and efficiently.
Regular checks and improvements based on these interventions can help prevent MSDs, reduce the risk of injury, and improve overall worker health and well-being. Furthermore, these proactive measures demonstrate a company's commitment to workplace safety, enhancing employee morale and productivity.
Implementing an Effective Ergonomics Program
The Power of a Well-Planned Ergonomics Program
A well-planned ergonomics program has the potential to revolutionize your manufacturing process. By targeting key risk factors and implementing suitable interventions, it can significantly reduce the occurrence of ergonomic injuries, such as musculoskeletal disorders (MSDs), back pain, and carpal tunnel syndrome. The resulting improvements in employee health and well-being can, in turn, lead to increased productivity and operational efficiency. As we advance into 2024, a strong focus on ergonomics is not only desirable but critical for the future success of the manufacturing industry.
Evaluating Your Existing Ergonomics Program
If you already have an ergonomics program in place, the first step is to evaluate its current effectiveness. This involves assessing what aspects of the program are working well and which areas require improvement. Are there initiatives that have successfully reduced instances of MSDs? Are certain workstations showing lower injury rates due to effective ergonomic design?
Conversely, consider areas where issues persist. For example, are there still frequent cases of back pain from heavy lifting? Are certain workstations causing awkward postures and resulting in pain or discomfort? By identifying both the strengths and weaknesses of your existing program, you can formulate a plan for enhancements that are tailored to your specific work environment.
Starting an Ergonomics Program from Scratch
If you're building a program from scratch, the initial step is to define your needs. To do this, you must thoroughly understand the unique demands and risks associated with your manufacturing process. Are there specific areas of risk that require immediate attention? Are tasks like heavy lifting a common feature of your employees' workday? Are the workstations ergonomically designed to minimize awkward postures and repetitive motion?
Once you have a comprehensive understanding of your needs, you can begin to develop a strategy that directly addresses these areas of concern.
Implementing Ergonomic Solutions
To implement an effective ergonomics program, consider adopting various ergonomic solutions that address your identified needs. This could include ergonomic software that helps in designing more efficient workstations, consulting with ergonomic experts to gain insights into best practices, or conducting training sessions to educate employees on proper work postures.
There's also the potential for more specialized solutions. For example, if heavy lifting is a significant risk factor in your workplace, consider introducing lifting aids or automation to lighten the load on your employees.
Regular Review and Adjustments
Finally, regular reviews and adjustments are crucial to ensure the ongoing effectiveness of your ergonomics program. Ergonomics is not a 'set and forget' initiative but rather a dynamic process that evolves alongside your work environment and manufacturing processes. Regular reviews allow for the early identification of new risk factors and the opportunity to address these before they escalate into more serious issues.
Implementing a comprehensive and effective ergonomics program is a significant commitment, but its benefits in terms of increased worker safety, enhanced productivity, and improved overall well-being make it an investment worth making. As we navigate through 2024 and beyond, prioritizing ergonomics will be instrumental in paving the way for a healthier and more productive manufacturing industry.
Looking Ahead: Ergonomics in 2024 and Beyond
The future of ergonomics in manufacturing looks promising. With advancements in technology, like wearable sensors, AI, and more sophisticated automation systems, manufacturers can further improve the work environment and reduce the incidence of workplace injuries.
Incorporating ergonomics into the manufacturing process is not just about compliance or avoiding injuries—it's about fostering a culture that values employee well-being. By doing so, manufacturers can realize the many benefits of ergonomics, from enhanced productivity to improved employee morale.
Whether you're just beginning your ergonomic journey or looking to enhance your existing program, keeping these best practices in mind for 2024 can help set the stage for a more productive, safer, and healthier manufacturing environment.
The content & opinions in this article are the author’s and do not necessarily represent the views of ManufacturingTomorrow
Comments (0)
This post does not have any comments. Be the first to leave a comment below.
Featured Product
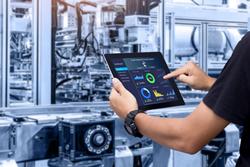