In this article, we look at hydrogen's path forward to a sustainable, clean hydrogen future, and address current industry requirements for safe and efficient production, conversion, transportation, and storage.
Heat Tracing in Hydrogen Processing, Storage & Transportation
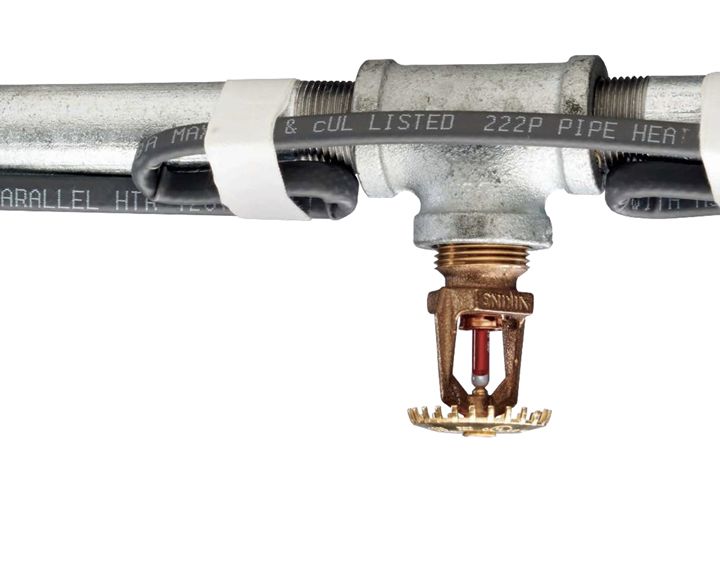
Daniel Bergeron, Applications Engineering Manager, Emerson Automation Systems | Nelson Heat Trace
While electrolyzers and methane reformers are common topics in the discussion of hydrogen, this article looks at how electric heat tracing can help solve problems that arise during different phases of hydrogen's value chain. Heat tracing, also known as heat tape or surface heating, keeps critical processes flowing by precisely maintaining required temperatures. Heat tracing also keeps instrumentation, gas and water lines, valves, and other auxiliary equipment from freezing when outside temperatures drop. This protection reduces downtime in hydrogen facilities and maintains capital investments.
Hydrogen Today
According to the International Energy Agency, hydrogen represents "the biggest innovation opportunity” to reduce global carbon dioxide (CO2) emissions. Clean hydrogen’s ability to replace fossil fuels without releasing CO2 when consumed has led to new applications being explored on numerous fronts, notably in fuel cells generating electricity.
While green innovations hold great promise, hydrogen as an alternative energy source represents only a small sliver of current overall consumption. Of the 120 million metric tons (MMT) of hydrogen consumed annually worldwide, the vast majority remains concentrated in the traditional sectors of petroleum refining and chemical processing. Each year approximately 55% of hydrogen goes into the creation of ammonia for fertilizer, another 25% into petroleum refining hydro-desulfurization and hydrocracking operations, 10% to produce methanol, and the remaining 10% in applications such as treating metals, flat glass manufacturing, chemical synthesis of plastics, and the manufacturing of semiconductors. Gaseous hydrogen is also utilized as a coolant for generators due to its high thermal conductivity.
Hydrogen Production
Hydrogen is the simplest and lightest of all Earth elements, consisting of only one proton and one electron. It is also the most abundant element in the universe, yet rarely in its pure state. Instead, hydrogen covalently bonds to other elements. Technologies enable the separating of hydrogen gas from its companion substances in purities in the order of 99.999%.
Worldwide, steam methane reforming (SMR) accounts for 95% of hydrogen produced. The SMR process is a reaction between a methane source, such as natural gas, and high-temperature steam (700°C–1,100°C). Coal gasification, a procedure combining coal with oxygen and steam at high pressures, produces another 4%, while water electrolysis yields 1%.
Although SMR is highly cost-effective, it requires fossil fuels as feedstock and to generate the electricity to produce heat. In fact, for every kilogram of hydrogen produced in SMR, approximately seven kilograms of CO2 are released into the environment. Capture and Storage techniques (CCS) seek to trap the CO2 released by SMR and store it in the ground, converting “gray” hydrogen to “blue”.
An alternative to steam refining is water electrolysis. This pathway splits hydrogen from water, effectively converting electrical energy into chemical energy. Like steam refining, electrolysis largely relies on fossil fuels. The only way the process is CO2 neutral—that is, it produces almost no greenhouse gases or other pollutants—is when renewable energy sources are employed, such as geothermal, hydro, wind or solar. Because this "green" hydrogen approach is considerably more expensive than hydrogen sourced from fossil fuels, it constitutes less than 0.04% of all hydrogen produced globally.
CHART:
Different methods of producing hydrogen are often referred to by certain colors:
- Brown hydrogen — Produced from the gasification of coal. Releases large quantities of CO2.
- Gray hydrogen – Produced by mixing fossil gas (natural gas, methane) with steam. Releases large quantities of CO2.
- Blue hydrogen – Produced using the same method as gray hydrogen, but with carbon emissions captured and stored underground.
- Green hydrogen – Produced by passing electricity generated from renewable sources through water, resulting in very low carbon emissions.
- Pink hydrogen — Like green hydrogen, this process incorporates electrolysis, but uses nuclear rather than renewable energy sources.
Heat Tracing in Hydrogen Production
Although heat trace cables do not produce enough heat for electrolysis (700° to 1000° F), the cables can be used around pipes and vessels to pre-heat water. Heat trace cables may also be installed to prevent demineralized water tanks or transported water in-plant from freezing, depending on its exposure during winter months. Another application is in the industrial deoxidizer machines that purify hydrogen stream from oxygen. Purity is especially important in achieving high efficiency of the hydrogen fuel cells powering vehicles, backup power systems, and even the electrical systems in spacecraft. In order to achieve near-100% purity, deoxidizer machines use temperature swing absorption or pressure absorption technology, often in conjunction with heat tracing cables.
Hydrogen Storage
Hydrogen may be physically stored as a gas or a liquid, yet both methods present challenges. Low energy density and the complexities of cryogenics are some of the biggest barriers. Hydrogen gas is prone to leakage. It can permeate through solid metals, as well as embrittle metals, which affects the integrity of storage and transportation infrastructure by creating cracks. Even a tiny leak can lead to the accumulation of dangerous hydrogen clouds in a confined area or within an enclosure. Another storage option is to chemically bind hydrogen with solids or liquids able to absorb it. Finally, there is the underground storage of hydrogen. Bulk storage of uncompressed hydrogen has proven viable in salt caverns, and to a lesser extent in porous media such as sandstone or shale, and in engineered cavities.
Heat Tracing in Hydrogen Storage
As a compressed gas, hydrogen is stored and transported in cylinders made of thick-walled aluminum, steel or composite materials capable of withstanding high pressures of 5000 to 10000 psi, or within vacuum insulated tanks. Removing compressed hydrogen from storage requires depressurization, which can cause problems for valves and pipes because of the sharp drop in temperature. Heat trace cables can counteract the temperature impacts of depressurization.
Condensation is a hurdle for cryogenics. It can form on the outside surface of uninsulated piping resulting in oxygen enrichment and an explosive condition. Also, air leakage into a liquid hydrogen storage vessel will bring about condensation. Its freezing can cause obstructions in piping causing malfunctions and presenting a possible fire or explosion hazard. Again, heat trace cables can combat condensation from both forming and freezing.
Hydrogen Transportation
If hydrogen isn’t consumed at its point-of-origin, known as “captive” production, bulk hydrogen must be transported to its point-of-use by railcar, barge, or over the road in gaseous tube trailers or in cryogenic liquid tanker trucks. Long-distance pipeline investments have been made by merchant producers in areas where there is a significant, steady demand for hydrogen. In the United States, there are approximately 1600 miles of active pipeline for hydrogen transportation, 90 percent of which is located along the Gulf coast of Texas, Louisiana and Alabama, serving refiners and ammonia plants. Pipelines are the least expensive method of transporting hydrogen.
Joule-Thomson Effect and Frozen Valves
It is common for hydrogen to carry some moisture, opening the possibility of a valve freezing whenever a process involves large pressure drops. According to the Joule-Thomson Effect, the gas temperature drops by 6 to 8 degrees Fahrenheit for every 100-psi cut across a valve. Once frozen, a valve will require expensive repairs and maintenance. This is even more likely when the outside temperature falls below 32 degrees Fahrenheit.
Methods to combat valve freezing can involve using methanol injection, thermal jackets, or steam. A far better alternative is wrapping vulnerable valves with heat trace cables. Unlike steam, heat trace cables will not deteriorate seals and seats in the valve, and heat trace cables are far less expensive than methanol.
Heat Tracing for Winterizing Hydrogen Operations
Malfunctions and catastrophic failures in hydrogen plants have resulted from frozen pipes, equipment, sensing lines, and instrumentation. Recent cold weather events, such as winter storms Elliott (2022) and Uri (2021) demonstrate these challenges. Frozen equipment may cause a forced outage or will prohibit a hydrogen processing plant from restarting. Burst pipes, wrecked instrumentation, and damaged processing equipment all must be repaired or replaced. A crack in a chemical line could easily become a significant environmental issue if left undetected.
As part of plant winterization procedures, any potential freeze-related risks to piping and processing equipment are to be identified and mitigated. Where insulation is not sufficient, heat trace cabling can be installed to respond to freeze threats, coupled with end-of-circuit heat trace indicator lights and remote monitoring displays in the plant control room.
Infrequently used piping and processing equipment containing liquids is especially at risk of freezing. Pipes that are part of life safety systems must be kept operational, like fire prevention systems and safety showers. Best practices call for heat tracing the water supply to these systems throughout the plant to ensure no potential freeze hazard is missed.
Hydrogen plants built in Southern states, from Florida to Texas, often feature outdoor designs that leave piping, instruments and processing equipment vulnerable to extreme cold, unlike the environmentally hardened plants in Northern climates. Following several unusually cold winter storms, regulators have recently become more proactive in plant inspections and are ordering reliability upgrades that require the installation of heat trace systems.
Hydrogen Dangers
All fuels have some degree of danger associated with them. Hydrogen is no exception.
Although the ignition temperature of hydrogen is similar to natural gas and propane, it has a wider flammability range of 4% to 74%, meaning the amount of hydrogen necessary to initiate combustion is much lower. Once ignited, hydrogen flames burn at extremely high temperatures (932° F) yet mostly outside of the visible light spectrum, making hydrogen fires both destructive and nearly impossible to initially detect. Worse still, at concentrations of 18.3% to 59%, hydrogen will explode.
These characteristics underscore the importance of Temperature Classification (T-Rating) to the safe handling of hydrogen, especially in the specification of electrical equipment. T-Ratings indicate the highest temperature allowed in an area that will not cause an ignition. What makes T-Ratings even more important is that hydrogen gas is prone to leakage. Hydrogen atoms permeate through conventional gas line infrastructure formed of steel, nickel, iron, cobalt and various alloys. Once absorbed, hydrogen gas will embrittle metals by lowering the stress it takes for cracks to form and propagate. A hydrogen leak, no matter how slight, generates a serious risk of fire.
Hydrogen has one safety advantage over other flammable fuels: hydrogen is 14 times lighter than air and rises six times faster than natural gas, which means that it disperses rapidly when released. Unless leaking hydrogen is contained by a roof or some other structure, it will quickly dissipate before it reaches a flammable concentration. The laws of physics prevent it from lingering near a leak unlike heavier propane or gasoline fumes. For that reason, hydrogen explosions and fires are most likely to occur in confined, poorly ventilated spaces where hydrogen is processed or stored in large quantities.
Heat Trace Cable Safety
The NEC Class/Division System for hazardous areas classifies hydrogen applications as being Class 1, Division 1 or Division 2, Group B, depending on the equipment’s proximity to the hazard. OSHA 1910.103(c)(1)(ix) specifies electrical wiring and equipment located within three feet of a point where connections are made must be in accordance with Class I, Division I, Group B. Those within twenty-five feet of a connection or a liquid hydrogen storage container must be in accordance with Class I, Division II, Group B.
According to the NEC, Group B refers to an area that contains a flammable gas, liquid-produced vapor or combustible liquid-produced vapor mixed with air that has the potential to catch fire and burn or explode. The elements in this Group have an MESG (Maximum Experimental Safe Gap) value equal to or less than 0.45mm or an MIC (Minimum Igniting Current) ratio equal to or less than 0.40. Some examples include hydrogen, butadiene, ethylene oxide, propylene oxide and acrolein.
Heat trace cables certified for hazardous areas feature T-Ratings well below hydrogen’s ignition point of 1085° F. For classified areas, this is achieved by limiting the watt density so sheath temperature will not exceed the required temperature. Cables may also feature a metal shield or sheath that acts as an effective return ground path as well as providing added physical protection.
Conclusion
Heat trace systems, like any other electrical device installed near hydrogen, have physical characteristics and performance features that must be incorporated before they can be safely deployed at production, storage, and distribution phases. Most important for the safe use in hydrogen service is that the equipment is rated by NEC 500 as Class I, Div. 1 and 2, Group B. Applying due diligence in the classification, design and installation per the applicable code will render hydrogen no more dangerous than any other product.
The content & opinions in this article are the author’s and do not necessarily represent the views of ManufacturingTomorrow
Comments (0)
This post does not have any comments. Be the first to leave a comment below.
Featured Product
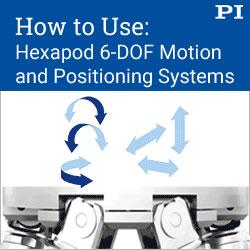