In the era of big data and corporate sustainability, industrial AI is undergoing a significant shift. It's moving from traditional use cases like predictive maintenance to more advanced solutions for predictive quality analytics.
Sustainability, AI, Industrial Dryers, and the Shift to Predictive Quality Analytics
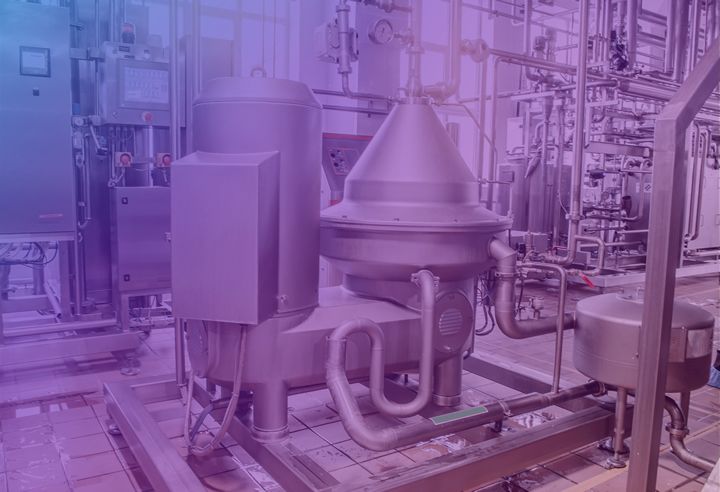
Case Study from | Canvass AI
In the era of big data and corporate sustainability, industrial AI is undergoing a significant shift. It's moving from traditional use cases like predictive maintenance to more advanced solutions for predictive quality analytics. Such solutions can predict product quality deviations early and provide real-time guidance to minimize loss. And what’s driving it is the corporate drive to sustainability.
A Commitment to Sustainability
In 2011, a leading global manufacturer of ingredient solutions for the food and beverage industry made a corporate commitment to sustainability. This commitment, coupled with aggressive goals and a vision to leverage big data, created opportunities for the company to look to reducing CO2 emissions, water usage, and waste, some key performance goals for the organization. Employees were also encouraged to work towards sustainable operations using AI.
The company operates 50 plants worldwide, and this case is about the first plant, one that processes tons of bushels of corn annually from the local region. The plant produces high-quality specialty corn starches and other derivative products for food and beverage manufacturers. The process for making corn starch is energy and water intensive. Essentially, the corn is steeped like tea, separated to get the corn starch, and then all the water needs to be properly evaporated.
Overcoming Challenges in Industrial Drying with AI
In collaboration with the company's engineers, the teams began by optimizing energy usage to produce steam at their cogeneration plant using the Canvass AI CoGen Optimization™ (CGO) solution, which I talked about here. The next step was to use the Canvass AI Dryer Moisture Optimization™ (DMO) solution to optimize the drying process, aiming to reduce energy and water usage.
Industrial drying is highly energy intensive. Reducing energy use without compromising on product quality or yield is a key challenge for engineers. Variability in feed characteristics, ambient conditions and operator actions can lead to inconsistent moisture levels in dried products. Higher moisture in the dryer can also lead to corrosion and shorten the lifespan of the equipment.
Compounding the problem is that drying control is often manual and depends on the operator's skill and experience. While experienced operators may be able to maintain the product quality at desired levels, their experience and skills are not captured and transferred to others, leading to significant differences in performance across different shifts.
Existing technologies for automated control are complex and require high upfront costs to implement, and equally high ongoing costs to maintain. In addition, skilled engineers who can develop the control models are difficult to find. As a result, most operations don’t implement automated controls for their dryer processes.
The Power of AI in Manufacturing
Canvass AI DMO™ Solution predicts moisture levels in the product at timely intervals. The predictions help operators, as well as the control system, make informed decisions on maintaining the moisture level closer to the control limit but still within specification, thereby optimizing energy use and increasing the product yield at the end of the drying process.
In the span of 8 weeks, the Canvass AI DMO solution reduced energy use at the plant by more than 10%, and increased high-quality product by 2%, which translates to millions in additional revenue when deployed for corn starch production alone.
While this customer is using the Canvass AI DMO solution for food ingredient production, industrial dryers are all over the place, and this solution can be applied to all types of dryers and drying processes in different industries.
The Shift to Predictive Quality Analytics
The use case above represents a subtle but important shift in the use cases of industrial AI. The focus is no longer just on predictive maintenance but optimizing set point controls that allow operators to control operations proactively. As companies start to see success with AI, they gain more confidence in integrating it into their daily workflow and operations. Companies are now seeking solutions that help them achieve their sustainability goals by reducing energy and water usage, while simultaneously improving product quality and increasing yields.
The shift in industrial AI towards predictive quality analytics is a testament to the power of AI in driving sustainability and efficiency in manufacturing. As companies continue to integrate AI into their operations, we can expect to see even more innovative solutions that make the superpowers of AI ever more accessible to users across industry, and not only improving product quality but contributing to a more sustainable future.
The content & opinions in this article are the author’s and do not necessarily represent the views of ManufacturingTomorrow
Comments (0)
This post does not have any comments. Be the first to leave a comment below.
Featured Product
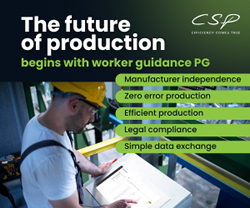