The only way to meet customer demand for speed, accuracy, and quality is to digitally transform. As our industry leverages new technologies that enable better processes, talent must evolve with it. No industry can afford to stand still, and manufacturing is no different.
Overcoming Manufacturing Challenges in 2024
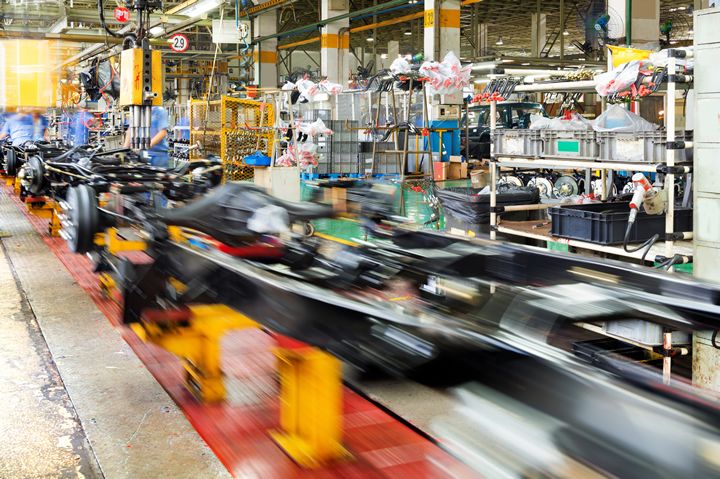
Q&A with Gustavo Sepulveda, Process Automation Business Head | Panasonic Connect North America
Tell us about yourself and Panasonic Connect.
I am the Process Automation Business Head for Panasonic Connect North America. In my role, I am responsible for leading the team that supports manufacturing businesses in North America. At Panasonic Connect, we provide manufacturers with automation capital equipment and software solutions that help them modernize their operations through automated SMT solutions, MES software systems, and welding robots. We also offer services within these three areas to keep manufacturers supported. Our solutions are purpose-built for today’s digitally enabled manufacturing environment, helping our customers deliver increased yield and higher quality products, while also transforming the employee experience.
What do you see as the top three challenges facing manufacturers?
Manufacturers have had to navigate a whirlwind of evolving challenges over the past few years. In 2024, we’ll continue to see challenges related to the persisting talent gap and lack of skilled labor. Additionally, manufacturers will have to navigate a shifting production landscape as they are challenged to optimize supply chain processes and add software technologies to their processes. Finally, material availability and cost mean that manufacturers will be challenged to produce with greater speed and accuracy and eliminate waste while optimizing and digitalizing their operations.
How can emerging technology help solve for these challenges?
Any solution we provide to customers must help them overcome a challenge. Implementing robotics and automated tools alongside upskilled talent is the key to meeting current manufacturing demands. Here’s an example: the latest in automated screen printers brings together both hardware and software to speed up printing processes with more precise changeover. In this example, production line changeover is automated, as are specific tasks within the production that machines can perform with more speed and precision than a human worker. This helps limit wasted material, promote accuracy, and frees up workers to take on important business tasks. Similarly, skills gaps can be closed with new technology as the learning curve for production is lower. This positions workers to be successful from earlier on in the process. Automation is here at the right time for manufacturers that are looking to streamline processes, boost production, and shorten training cycles.
Why is it so important for manufacturers to evaluate and update their processes in today’s environment?
The only way to meet customer demand for speed, accuracy, and quality is to digitally transform. Similarly, as our industry leverages new technologies that enable better processes, talent must evolve with it. No industry can afford to stand still, and manufacturing is no different. Our industry has traditionally been very susceptible to macroeconomic challenges. This has forced the industry to look internally to find optimizations – many of which continue to be found in manufacturing processes. In talking with manufacturers, it’s clear that a gap still remains from identifying where a process can be updated and finding the right tools and technologies to make it happen. Manufacturers should seek technology partners that speak their language, intimately understand their challenges, and offer services and support to deploy, maintain, and optimize solutions. This allows for incremental evaluation of performance, and a data-driven approach to process updates.
How much of a priority should reshoring be for a manufacturer?
Almost every manufacturer we talk with is actively discussing reshoring. With shifting consumer demand, manufacturers are looking to shorten supply chains and avoid potential disruptions from overseas. The good news for manufacturers in the Unites States is that investment from various funding acts and other incentives means that North American manufacturing hubs are undergoing a revival (or, in some cases, an emergence).
The United States has a generational opportunity to take a lead in modern manufacturing, both from a talent and technology perspective. It’s unlikely that the United States will immediately have the same robotics capacity as countries in the Asias, but that journey to align people and technology needs to accelerate. Additionally, while reshoring is important to strengthen supply chains, it’s also critical to consider broader manufacturing diversification. Whether spreading the load across multiple sites in case of disruption, or in establishing a trusted supplier network that can be called upon in time of need, it’s important for manufacturers to have options. Every business is different, and we caution against a one-size-fits-all approach to manufacturing. The right blend of reshoring, automation, robotics, MES, and talent looks different for all manufacturers. What’s consistent, however, is a desire to shorten supply chains, digitally transform processes, and make data-driven decisions.
What types of training programs do you suggest manufacturers put in place to attract and retain workers?
For training programs, mixing theory and practical learning should be encouraged. Programs that teach how advanced, automated, connected systems work while also giving employees hands-on time to experience how new machines work is important. Interestingly, we’re seeing this approach filter down to colleges and universities, as the industry prepares future generations to enter the workforce. For example, we have a partnership with a college in which we donate machines so that students can put theory to the test. For those currently in the workforce, one technique that has shown successful application is, “training the trainer.” We offer a program at Panasonic Connect in which we train certain people within an organization who will be the “trainers.” They have the chance to work with us and ask questions that they can have directly answered from the solution experts. Then, as they become familiar with the technology, they can translate it, apply it, and teach it to their peers in a way that makes sense for the organization. It helps shorten learning curves. Lastly, do not underestimate the power of mentorship programs. I, myself, have participated in several mentoring programs, and within 12-18 months, it’s rewarding to see mentees grow. This also leads to higher employee satisfaction and helps employees see a path forward for them within an organization.
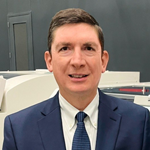
Gustavo Sepulveda is the Process Automation Business Head for Panasonic Connect North America. Panasonic Connect is a B2B company offering device hardware, software, and professional services for the connected enterprise. Gustavo leads a team that delivers automation solutions to the electronics and metal fabrication industries. He works with manufacturing customers to navigate their ever-changing and challenging environment, such as the migration of operations to North America. Gustavo is a passionate leader and mentor who is dedicated to shaping the next generation of workers.
The content & opinions in this article are the author’s and do not necessarily represent the views of ManufacturingTomorrow
Comments (0)
This post does not have any comments. Be the first to leave a comment below.
Featured Product
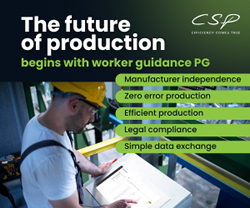