In this article, we aim to guide manufacturers who recognize the importance of this transition. We delve into the complexity of evaluating current systems, setting precise objectives, and embracing the opportunities of modern technologies available.
From Legacy to Leading-edge: Navigating the Shift to Modern Manufacturing Systems
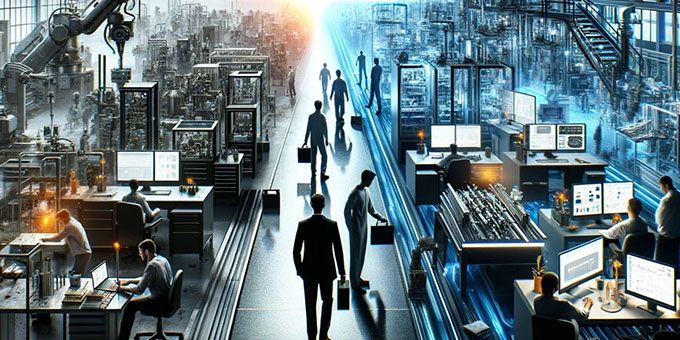
Article from | Elisa IndustrIQ
In manufacturing, legacy systems often represent a barrier to progress. These system infrastructures, once the backbone of industrial operations, now fall behind amidst a digital transformation that demands agility, efficiency, and connectivity. The transition from such legacy systems to modern manufacturing software solutions is not merely an upgrade; it is a necessary change to remain competitive and relevant in a rapidly changing market.
In this article, we aim to guide manufacturers who recognise the importance of this transition. We delve into the complexity of evaluating current systems, setting precise objectives, and embracing the opportunities of modern technologies available. Our goal is to provide an initial roadmap that navigates this transformation and showcases you can start your digitalisation journey with the profound advantages that await on the other side
ASSESSING YOUR CURRENT MANUFACTURING SYSTEMS AND INFRASTRUCTURE
Begin with a careful audit of your current systems. This should encompass hardware, software, processes, and the human elements that interact with them.
Consider the following:
- System Capabilities: Evaluate if your current systems can meet the demands of modern manufacturing practices. Are they flexible, scalable, and integrable with new technologies?
- Workflow Efficiency: Analyse the workflows that your legacy systems support. Look for bottlenecks, redundancies, or any processes that could be streamlined.
- Data Utilisation: Assess how data is collected, stored, and utilised. Is valuable data being siloed or underutilised due to system limitations?
With the audit data in hand, pinpoint the gaps and inefficiencies that are costing your business time and money. This could range from slow response times and frequent system downtimes to an inability to support remote monitoring or real-time analytics. Furthermore, consider the risks associated with your current systems. This includes vulnerability to cyber threats, compliance issues, and the potential for costly breakdowns or failures.

- Hardware age and performance levels.
- Software updates and support – are they still receiving updates from the vendor?
- Integration capabilities with other systems and potential for future integrations.
- User feedback on system performance and usability.
- Support and maintenance costs.
By the end of this assessment, you should have a good indication of where your current systems stand and a vision of what you need from modern manufacturing systems. This clarity is crucial as it sets the stage for the next steps: defining your objectives and exploring the possibilities that modern technology offers.
SETTING CLEAR OBJECTIVES
Finally, document your objectives clearly and distribute them among your team and any external partners involved in the transition. This documentation will serve as a blueprint guiding all subsequent decisions and actions. By setting clear objectives, you create a focused framework for your digital transformation journey. This clarity will guide your technology choices, inform your implementation strategy, and provide a benchmark against which to measure success.
PLANNING THE MANUFACTURING SOFTWARE TRANSITION
With a solid understanding of your current systems and clear objectives set, the next step is to plan the transition to a modern manufacturing system. This phase is critical; a well-crafted plan will serve as your roadmap, helping to navigate the complexities of the transition while minimising disruptions to your operations.
Your transition plan should be comprehensive, detailing every step from the selection of new technologies to the final switch-over. Key elements to include are:
- Timeline: Establish a realistic timeline for the transition, with milestones for significant phases such as vendor selection, training, and go-live dates.
- Budget: Outline the financial investment required, including costs for new hardware, software, training, and any potential downtime.
- Resource Allocation: Determine the human and technical resources needed to execute the transition. This includes internal teams and any external vendors or consultants.
- Stakeholders: Stakeholder buy-in is crucial for a smooth transition. Identify all stakeholders, including employees, management, and external partners. Develop a communication plan that keeps stakeholders informed and engaged throughout the process.
Choosing the right partners is vital. Look for vendors with proven expertise in the manufacturing sector and a track record of successful system implementations. Consider not only the technology but also the support and training they offer. On top of that, it is important how the vendor approaches the integration of the existing system with the new software. A phased approach can help manage the complexity and reduce risk.
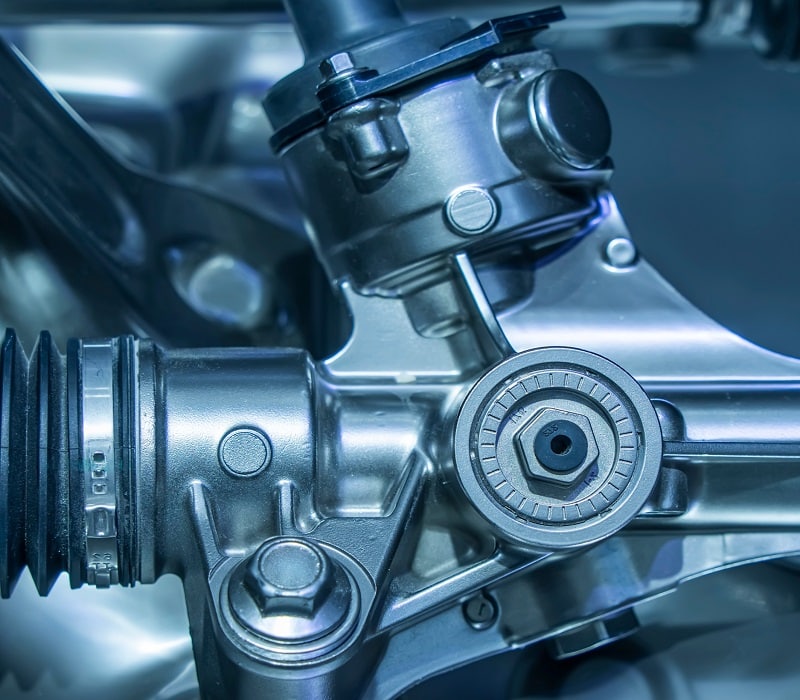
Despite the best planning, unexpected issues can arise. Have contingency plans in place to address potential problems without causing significant delays or cost overruns. Before full implementation, test your transition plan on a small scale to identify any gaps or issues. This could involve a pilot program or a trial run of certain components of the new system.
Finally, ensure that all changes are documented, and that the new system complies with industry regulations and standards. This documentation will be crucial for audits and for maintaining operational transparency.
MANAGING DATA MIGRATION AND WORKFORCE TRAINING
The transition to a modern manufacturing system is a multifaceted journey, with data migration and workforce training being two of its most critical aspects. Both require thorough planning and execution to ensure a seamless shift from old to new without data loss or significant downtime.
Data is the lifeblood of modern manufacturing, and its migration is a delicate process. Begin by identifying the data that needs to be transferred to the new system. This typically includes production data, customer information, inventory levels, and supply chain details. Prioritise data based on its importance and frequency of use.
Develop a data migration plan that includes:
- Data Cleansing: Before transferring any data, cleanse it for accuracy and completeness. Remove redundant or obsolete information to ensure that only valuable, high-quality data is migrated.
- Migration Testing: Conduct thorough testing of the migration process using a subset of your data. This helps identify potential issues before the full-scale migration.
- Data Mapping: Clearly map out how and where each piece of data will be stored in the new system. This ensures that data is accessible and usable post-migration.
- Backup Plans: Always have a full backup of your data before beginning the migration. In the event of a problem, you can restore your system to its original state.
The success of new manufacturing systems is largely dependent on the people who operate them. A well-trained workforce can maximise the benefits of new technology, while a poorly trained one can hinder its effectiveness. Make sure to develop comprehensive training programs tailored to different user groups. This should include hands-on training for users to get comfortable with the new system. Furthermore, establish support structures to assist employees during and after the transition. This could be a helpdesk, online resources, or a team of ‘super-users’ who can provide peer support.
Implement mechanisms to gather feedback from employees on the training process and the new system’s usability. Use this feedback to make continuous improvements.
Both data migration and training benefit from a phased approach. Start with less critical data and user groups to refine your processes before moving on to more critical areas. This allows you to address issues on a smaller scale and reduces the risk of widespread disruption.
POST-IMPLEMENTATION REVIEW AND CONTINUOUS IMPROVEMENT
- Performance Metrics: Compare the performance metrics of the new system against the objectives set at the beginning of the transition. Have the expected improvements in efficiency, productivity, or quality been realised?
- System Stability: Assess the stability of the new system. Are there any recurring issues or downtime that need to be addressed?
- User Adoption: Evaluate how well users have adapted to the new system. Is there resistance, and are there areas where additional training may be required?
- Feedback Collection: Gather feedback from all levels of users, from shop floor operators to management. This feedback is invaluable for identifying areas for improvement.
With the initial review complete, establish processes for continuous optimisation:
- Regular Check-Ins: Schedule regular check-ins with system users and stakeholders to discuss system performance and any challenges they’re facing.
- Update and Upgrade Policies: Technology evolves rapidly, and your new system will require regular updates and potential upgrades. Establish policies for how and when these will be implemented.
- Performance Monitoring: Continuously monitor system performance against the established KPIs. Use this data to identify trends and areas for improvement.
User feedback is a goldmine of information that can drive continuous improvement.
The post-implementation review and continuous improvement phase is where the true value of your new manufacturing system is realised. By actively seeking out and responding to feedback, monitoring performance, and staying abreast of technological advancements, you ensure that your manufacturing operations are not just up-to-date, but are also continuously pushing the boundaries of efficiency and productivity.
CONCLUSION: ADOPT TAILORED MANUFACTURING SOLUTIONS FOR A COMPETITIVE EDGE
The content & opinions in this article are the author’s and do not necessarily represent the views of ManufacturingTomorrow
Comments (0)
This post does not have any comments. Be the first to leave a comment below.
Featured Product
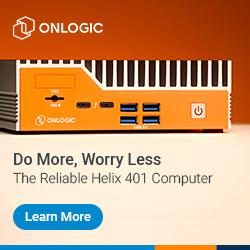