Electromechanical cylinders are one of the hidden champions in factory automation. They’re incredibly simple, versatile and energy efficient. Five trends are shaping the current development of these popular actuators.
Electromechanical Cylinders: a Standard Component or a Trendsetter in Factory Automation?
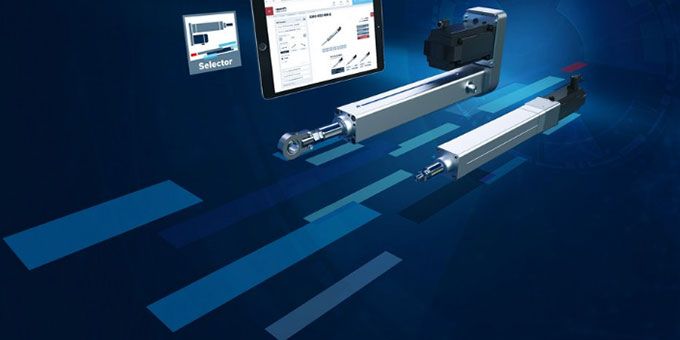
Dr. Sebastian Unsleber, Senior Manager Product Management | Bosch Rexroth AG
Electromechanical cylinders are one of the hidden champions in factory automation. They’re incredibly simple, versatile and energy efficient. Five trends are shaping the current development of these popular actuators.
It is hard to imagine production without electromechanical cylinders - they position, swivel, lift, press, join, punch, crimp, and rivet things. Because they convert motor torque directly into movement, they are particularly energy efficient and, as part of electrification, play an important role in climate protection. Naturally, the process quality and overall costs must be right. These five points show the continuation of an industrial success story:
1. The potential for standardization is increasing
Climate-friendly operation, stable processes, long service lives and great potential for standardization – these properties speak in favor of using electromechanical actuators as widely as possible. Thanks to ongoing development, applications now include pneumatic and fluid-driven solutions. If additional complex solutions are replaced, this reduces not only complexity but also overall costs. Compared to compressed air, electromechanical systems can be better controlled for accuracy. Overall, applications range from dynamic positioning tasks with forces from 0.1 kN to pressing and joining applications with up to 100 kN. The target sectors are equally broad and include semiconductor production, fast-moving consumer goods (FMCG) and battery manufacturing.
2. High process quality in every power class
At Bosch Rexroth, we refer to versatile actuators as electromechanical cylinders (EMCs). One of the keys to the EMC's efficiency lies hidden beneath its housing: the ball screw drive. In addition to the typical ball screw assembly for forces from 0.1 to about 30 kN, planetary screw drives are also used for heavy-duty applications. The "high power" EMC-HP version uses the proven PLSA planetary screw assembly, which allows speeds of up to 0.83 m/s and a high output of forces of up to 100 kN, even under harsh environmental conditions. In addition to a dynamic load rating (Cdyn) of up to 189.5 kN, output is also ensured by oil bath lubrication and, on request, optional water cooling on the screw itself.
3. Service life: 200 million revolutions without relubrication
At the heart of the standard EMCs, which often have a wide range of sizes, is the ball circulation screw, which allows not only high load capacities but also particularly long lubrication intervals. The latest product generation achieves up to 200 million revolutions with the basic factory lubrication, and the ball bearings cover a distance of around 12,800 km on the screw – the same distance as from Germany to Hawaii.
With standard lubrication, EMCs with the achieve a nominal service life of up to 15,000 km. With relubrication, they can cover over 50,000 km. This creates optimum conditions for minimizing operating costs and damage to the environment. The longer lubrication interval saves time and resources.
4. Time savings thanks to next level engineering
There are thousands of cylinder configurations, but new digital engineering tools now allow even inexperienced users to plan, detail and optimize their machine and system parts. This accelerates users speed and flexibility in the face of increasing time and cost pressures.
With a level of user-friendliness previously offered only by modern B2C (business to consumer) portals, these tools provide a glimpse into the future of online sales of complex industrial goods. The easy-to-use online tool shows the entire process on a single HTML page, including selection, ordering, and design and functionality characteristics. Often, content is dynamically reloaded depending on user actions. These new online resources can also recommend suitable products, show technical specifications and a configuration overview immediately while illustrating the current project status with a live 3D model using the actual CAD data. This enables engineering work to take minutes instead of hours.
Next level engineering: Using digital tools to build an individual cylinder in minutes
Web-based tools factor in the entire process chain: From the rough to detailed design and planning (including price and delivery information), to direct order placement with prior download of CAD data and data sheets. Time-intensive subprocesses such as preliminary meetings, approvals and quotations or recalculations with other parameters are no longer necessary or take significantly less time. The current project can also be saved and shared via a link for flexible, collaborative work.
5. Automation: Smart subsystems including software
Time is a precious commodity, not only in engineering but when preparing for production too. Electromechanical cylinders that are configured with a motor can automatically parameterize themselves. The necessary data for the drive controller is stored in the motor data memory at the factory and is loaded immediately after connection. Those who are focusing even more on the Factory of the Future will also find highly integrated and flexible subsystems for pressing and joining tasks, like the Smart Function Kit for Pressing. These complete subsystems with an electromechanical cylinder relieve the burden on the design department, and they make purchasing, assembly, commissioning, programming, quality assurance and service processes easier. The Smart Function Kit Pressing includes the EMC and the ctrlX AUTOMATION control platform with preinstalled software. The order is placed after a short digital design and configuration procedure under a single material number. Once on site, a digital wizard reduces the commissioning time to just a few minutes. Visual sequencing requires no programming knowledge. Instead, the work process is defined via Drag & Drop with function modules from the software library. Quality monitoring and exchanging data for documenting processes can also be set up easily.
The right solution for all requirements
Electromechanical cylinders are both proven standard components and trendsetters in factory automation. Due to their simple design, electromechanical cylinders have a lot to offer in factory automation. With their great versatility, they allow standardization, finely regulated processes, and resource-saving operation. New digital engineering tools and convenient selectors along with ongoing improvements to the service life reduce overall costs, while intelligent subsystems pave the way to the Factory of the Future.
Solutions with a high level of flexibility and integration allow for more efficiency during implementation. When it comes to selecting a provider, it is worth reviewing the entire portfolio. Manufacturers that offer a broad, freely configurable range from a single source have an advantage in terms of future requirements such as climate protection, the shortage of skilled workers and flexible manufacturing.
Electromechanical cylinders with optional motor attachment.
Electromechanical cylinders depending on the force range, optionally with ball screw or planetary screw. Image: Bosch Rexroth
Electromechanical cylinders with the lifetime lubrication option for many applications.
Bosch Rexroth also offers complete sub-systems for pressing and joining applications, consisting of electromechanical cylinder incl. drive, control and software.
Connect and read out - never before have parameters been transmitted so quickly and securely.
The content & opinions in this article are the author’s and do not necessarily represent the views of ManufacturingTomorrow
Comments (0)
This post does not have any comments. Be the first to leave a comment below.
Featured Product
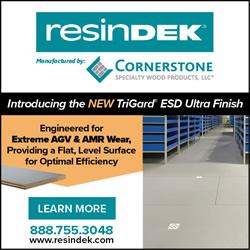