Digital weld sequencing helps companies to quickly train new welders in times of skills shortages and thereby steadily produce better welding results.
Weld Sequencing: Greater Control for Better Results
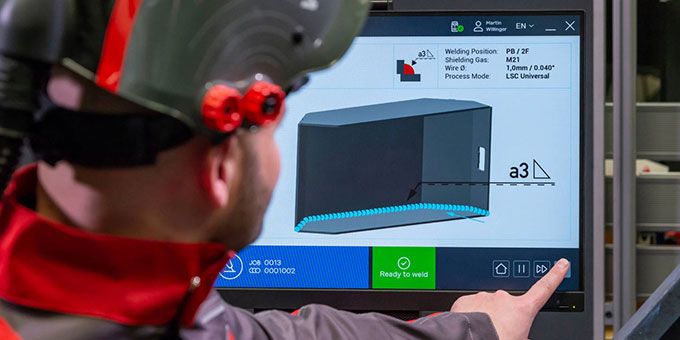
Article from | Fronius Perfect Welding
It knows what needs to be done and how. It reacts to the conditions and reliably guides welders to the desired result. It helps to quickly train welders and offers the best possible control over every weld. It supports companies in saving time and resources. It’s called weld sequencing. But what exactly is it?
Welding with sequences is hugely beneficial for welders and companies alike. “Sequences” involve individual steps or instructions which guide workers through the welding process. Digital weld sequencing helps companies to quickly train new welders in times of skills shortages and thereby steadily produce better welding results.
Weld sequencing: Achieve the desired weld quality step by step
Errors happen and we are all human. However, incorrectly welded joints can result in enormous costs and have a negative effect on overall productivity and quality, particularly during production. So it’s important to prevent them from occurring during the production process in order to save time and money. This is possible thanks to weld sequencing.
We’re not talking about a hefty, printed, physical welding plan, but a digital software which gives welders step-by-step instructions in real time, guiding them reliably through their welding tasks to the desired result.
A printed version is still common practice in many companies: “Some companies use larger design drawings or component plans with the welds indicated and detailed descriptions along with numbering for the individual steps. If these companies were to switch to digital weld sequencing, they would no longer need to print these out, saving not only time but also paper,” says Anita Beck, Product Manager Welding Data & Applications at Fronius International.
Weld sequencing: How it works
What is it like to use weld sequencing? Welders basically stand at the work station and let the software show them what to do next. An additional screen shows each production work step visually in the correct order and the parameters are automatically set on the welding system. Workers are steadily guided through their tasks and it is easy to follow the correct welding sequence and ensure that the defined parameters are also used for each weld.
Workers also receive feedback on their welds and can monitor their progress. If an error occurs, the welding system automatically locks and welding can only continue once it has been cleared by the welding coordinator. This early intervention can ultimately save companies time and money.
It means that long training sessions are no longer needed and the focus is on welding right from day one.
Why should companies use weld sequencing?
Do you want to increase production quality in manual welding cells? Do you want to standardize workflows? Do you need to counter high staff turnover? Weld sequencing is the solution for all of these questions.
Weld sequencing also makes life easier for welders. Not only does it provide welding process knowledge, it also knows a lot about individual components. It knows exactly which order to work in or which direction to weld in. It assists not only beginners but also experienced welders, with the latter in particular benefitting from weld sequencing for components that are not often encountered:
“In agricultural engineering, we know that certain products are only produced at specific times of year, then there may be a six-month pause. If a welder is working on a component again after such a gap, they generally have to spend time getting to grips with it again. With weld sequencing, there’s no need for this, as it tells them exactly what they need to do. The welding is controlled and this ensures the desired result at the end,” says Anita Beck.
Weld sequencing as a secret weapon in the fight against skills shortages
The welding industry is in the grips of a global skills shortage. According to a survey by auditor EY, 83% of companies in Austria are experiencing difficulties in recruiting skilled workers. The situation is not much different elsewhere. In the USA, for example, the American Welding Society (AWS) has predicted a shortage of around 300,000 to 400,000 welders by 2024. Solutions are urgently needed.
Digital weld sequencing won’t help you to find new skilled workers. But, once they arrive, it helps them to achieve good welding results more quickly. Weld sequencing is particularly useful for companies who are struggling to carry out efficient production with the necessary level of quality due to skills shortages or staff turnover.
From taxis to the welding shop
When people from a wide range of jobs, whether it be waiters or taxi drivers, retrain as welders, they usually take a basic course which teaches them how to hold a welding torch or at what speed they need to weld. However, beginners generally have little experience with the welding process itself. Other aspects, such as the effect of heat input on components, distortion, or material strength are often still unclear to new welders in the early days. This doesn’t matter as weld sequencing makes all this knowledge available.
“The worker doesn’t need to know how the parameters interact behind the scenes of the welding process. They just need to guide the welding torch, have good manual dexterity, and be able to read off the display where to place a weld. The weld sequencing software does the rest. This means that people who have come straight from other jobs who don’t have much welding experience yet can still produce great results, learn quicker, and are much more likely to enjoy their work,” sums up Anita Beck.
WeldCube Navigator: Easy, logical welding
An example of digital weld sequencing comes in the form of the Fronius WeldCube Navigator: a software which supports welders during production and combines all the aforementioned advantages of weld sequencing.
Two key elements of the software are the sequencer and the editor. The sequencer guides the worker through all welding tasks via an appropriate screen in the welding cell and the output is monitored in regard to the permitted number of welds. What is particularly practical is that the welder can operate the WeldCube Navigator throughout with the welding torch. Selecting instructions, switching to the next job, and confirming can all be done with ease from the torch itself!
The editor digitizes and visualizes instructions for production. It can create and save digital work instructions for manual welding production. For example, individual images for each work step can be uploaded with the necessary information for the welder. Special instructions can also be defined, such as the number of permitted welds, the welding job to be used, and the response in the event of an error. This provides maximum flexibility in terms of design and conveying information!
The WeldCube Navigator gives you full control when welding – from the first to the last weld
Want to find out more about the Fronius WeldCube Navigator? Take a look at our website! Why not also browse through our other blog posts on the topic of digitization, such as on digital welding data documentation, the effect of digitization on social development, or big data with welding, and discover what it’s all about!
The content & opinions in this article are the author’s and do not necessarily represent the views of ManufacturingTomorrow
Comments (0)
This post does not have any comments. Be the first to leave a comment below.
Featured Product
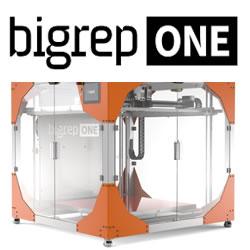