This article will address the transition to automated support removal (and finishing) solutions and consider the advantages and disadvantages of using CNC systems versus the versatility and reliability of robots.
Automated Support Removal & Finishing for Metal AM — Robots vs CNC
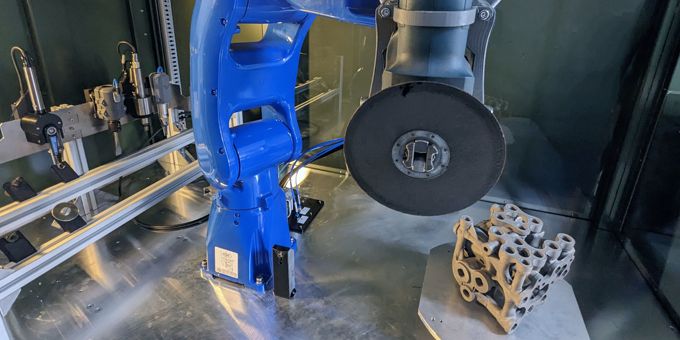
Article from | RIVELIN ROBOTICS
The use of metal additive manufacturing (AM) has revolutionized the manufacturing industry, allowing for the creation of complex and intricate parts in a faster and more cost-effective manner. However, essential post processing of these parts introduces time and financial constraints to the overall cost-per-part that can negate the benefits of AM altogether. Support removal is the critical first step of post processing metal AM parts, and it is a challenging one. Today, supports are still essential for part fidelity during the manufacturing process, but they must be removed to achieve the required finished product with the intended shape, features and tolerances.
While manual support removal is still the status quo for many applications of metal AM, this article will address the transition to automated support removal (and finishing) solutions and consider the advantages and disadvantages of using Computer Numerical Control (CNC) systems versus the versatility and reliability of robots.
TO SUPPORT OR NOT TO SUPPORT? THAT IS THE QUESTION
There is an argument that the support removal conundrum in AM will eventually be resolved by so-called support-free printing. Of course, this would be the ultimate goal, allowing complete design freedom with optimised resource efficiency, whereby raw materials and energy are only being used to make the final part and not the supports.
Unfortunately, the AM sector is not there yet, and while supports are being minimised through design, they are still — and will be for the foreseeable future – a necessity. Minimising the amount of material and energy used for supports is the right thing to do in almost every situation, but it can also compromise design freedom and have a negative impact on the desired functionality of the end-use part, which may, for example, need to be designed with filled cavities or overhangs leading to loss of light-weighting. Generative designs may also be unnecessarily constrained to get the angles needed for reduced supports.
A focus on support reduction can also affect process efficiency. For example, long parts may have to be built in a specific orientation and therefore take up more of the build plate, and stacked builds may become impractical because of the interconnecting support structures.
In short, while we should always strive for less supports, they are currently still a necessary tool for most complex AM applications.
MANUAL POST PROCESSING
Shockingly, manual support removal remains the process of choice for the majority of AM users today. It requires highly trained technicians to remove supports with all manner of traditional hand tools. Dremels come in useful too. It is tried and tested but requires skill, problem-solving and creativity. It can be well suited to high mix, low volume production environments.
However, manual support removal is also very time-consuming, labour-intensive, messy, with toxic dust requiring PPE or shielded environments. Risk of powder ignition and explosion, and repetitive strain injuries are common problems. In addition, it is not accurately repeatable with variability from person to person and even from shift to shift causing quality control problems and increases in scrap rate. It is also difficult to scale if the demand for AM parts begins to increase significantly.
AUTOMATION, AUTOMATION, AUTOMATION
There has been some progress with solutions for automating the post processing of metal AM parts. The most common has been the utilisation of CNC milling machines, a proven technology for a variety of manufacturing applications, including a hybrid approach to AM. They are undeniably accurate and repeatable. However, just because something is common and has a good track record in some areas, it does not necessarily mean that it is always the best solution.
CNC can work well if the part in question has tightly toleranced features, and where flatness, circularity, concentricity, or dimensions have to be within a few microns. It is also the preferred technology for support removal in large batch builds where geometries are simple or lend themselves to easy fixturing in only a couple of orientations. Similarly, it can be a good fit for prints where platform removal with a CNC EDM takes care of the majority of supports.
However, CNC machines are not a good solution for thin-walled components, space-saving stacked builds, and parts with lattice structures or breakaway supports. It is also fair to say that CNC programmers don’t like one-off generatively-designed organic shapes with compound curves.
This begins to clarify and strengthen the argument against CNC for support removal in the AM ecosystem.
One of the main drivers of AM is the flexibility of design that allows users to iterate, customise, and upgrade components from one batch to the next. That means it is rare for companies using AM for production to invest in rigid industrial automation. Any iteration, any change to the design would mean a new CNC trajectory for a new tool path and come at a high cost. AM needs this design flexibility to be carried to every step of the manufacturing process chain.
The problem is similar for tooling and fixturing. The kinds of high-precision fixtures required for rigid industrial automation just don’t make sense unless you are prepared to commit to a design long term.
And then there’s the problem of batch-to-batch variability. Even if you did have a perfect fixture and a perfect tool path, relying on a perfectly predictable support surface straight from the printer may not be the best idea. This is because it is expected that AM supports deflect so AM parts don’t have to. AM supports are made thin to maximise the use of powder stock. Thin connections are made to the component to minimise surface witnesses and make it easy to break away the scaffolding. Material composition is even changed between batches sometimes, all of which means supports may look and behave very differently from one batch to the next.
ROBOTS TO THE RESCUE
So, AM needs automation that can adapt to variability, especially for support and witness removal. And this challenge has been solved through the use of sophisticated software and artificial intelligence systems to help generate toolpaths and robot motions without mobilising an entire systems-engineering team. This then allows for quick iteration as well as automation of small batches.
3D scanning can be used to locate parts instead of high-precision fixtures, which means desktop FDM printers can be used to make plastic fixtures quickly without worrying about accuracy or changes to the design. In addition, force sensors can be used to feel the surface and adapt the machining accordingly, or to spend more time on high spots until the final shape is reached, or to polish to a consistent finish.
One huge advantage is that any tool can be used for support removal and finishing. If it is already known what tools work well with the materials or the types of supports printed, the same exact tools can be attached to a robot to automate with more confidence. With today’s technology, the steps to add a new custom tool are basically like adding a new type of endmill to a CNC machine, and does not require a system integrator that charges by the hour.
Rivelin Robotics, which specialises in metal AM post-processing, already has products that do this. The company specializes in the development and installation of robots for a wide range of AM post processing applications. In the context of removing supports from metal additively manufactured parts, Rivelin Robotics offers advanced robotic solutions that are specifically designed to perform this task reliably and accurately.
The company's robots provide a range of benefits over traditional CNC machines, such as improved speed, accuracy, and repeatability when applied to support removal and finishing. They are also highly flexible, which allows them to be easily adapted to different applications and processes.
Rivelin Robotics' robots are also designed with safety in mind, with protective casing and safety features that reduce the risk of accidents and injuries. Moreover, power and coolant requirements are far lower than is the case with CNC machines, which helps increase resource efficiency and energy efficiency while at the same time reducing waste.
To summarise, robots are emerging as a superior solution compared with CNC machines for the automated removal of supports from metal AM parts due to their speed, efficiency, flexibility, accuracy, repeatability, safety, cost-effectiveness, and sustainability. The use of robots in this process not only results in a better finished product, but also provides a safer, more sustainable and more cost-effective end-to end manufacturing process.
The content & opinions in this article are the author’s and do not necessarily represent the views of ManufacturingTomorrow
Comments (0)
This post does not have any comments. Be the first to leave a comment below.
Featured Product
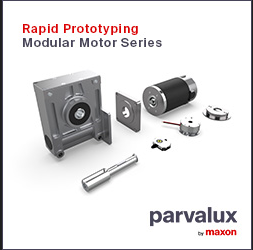