Manifolds are complex parts that require several levels of expertise to optimize. At Inkbit, we are optimizing the manufacturing of manifolds that finally unlock the geometric freedom of additive manufacturing.
Exploring Manifold Design
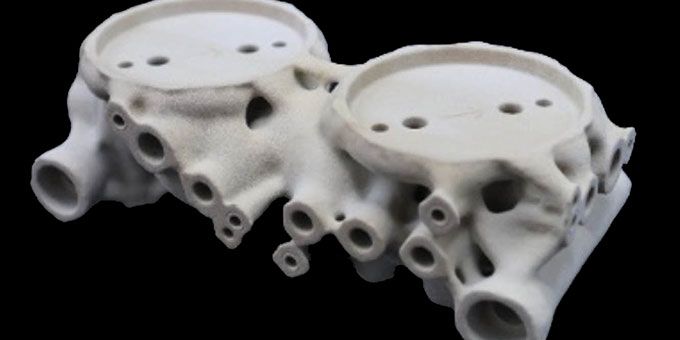
SHAI ALMAGOR, APPLICATIONS ENGINEER | inkbit
Unlocking Geometry with Inkbit Vista™
Manifolds are complex parts that require several levels of expertise to optimize. At Inkbit, we are optimizing the manufacturing of manifolds that finally unlock the geometric freedom of additive manufacturing.
Manifold Design Today
There is a problem in the industry today: engineers want to be able to design and manufacture fluid manifolds that are optimized for flow. The existing methods of manifold fabrication place major constraints on channel geometry. This makes it very difficult to optimize and places additional engineering burden on the equipment design. Additionally, the fluids used in these manifolds are frequently corrosive, requiring that the manifold material be made of a chemically resistant material. Engineers want a solution that provides geometric freedom while maintaining the excellent chemical resistance of existing fabrication methods.
Figure A: Traditional manifold design, machined out of a block of aluminum, constrained by the geometric capabilities of a 5-axis mill.
Inkbit Vista™, providing new tools for designers
While many may think Inkbit Vista™ is just for the production floor, it provides new tools for product design and development. To illustrate, let’s look at the designed manifold printed with Inkbit Vista™ (see Figure B). This is a part we made for one of our clients. The client had an elaborate aluminum fluid manifold used to pump and circulate fluids. The client was looking for a way to improve efficiency and to reduce the driving pumps’ power loss.
We were able to design a chemically resistant manifold that not only met our client’s requirements, but also improved the fluid dynamics, reduced weight, and cut down lead time by 15x. Our design takes advantage of generative design, while maintaining the production level properties that make it appropriate for its intended application.
Figure B: Optimized Fluid Manifold, designed by Inkbit Applications Team and printed on Inkbit Vista™.
Comparison to Industrial Manufacturing Shop
COMPANY |
PRICE / PART |
LEAD TIME |
WEIGHT OF PART |
POWER LOSS (%) |
Industrial Manifold Manufacturer |
>=$200 |
>=1 Month |
3870g (Aluminum) |
100% (base line) |
Inkbit Vista™ |
$42.14 |
48 hours |
<400g (Titan Tough Epoxy) |
60% (of base line) |
Unlocking Geometric Freedom with Additive Manufacturing
Using Dassault Systems “Flow Driven Topology Optimization” app, we were able to reduce the power loss by up to 40%, the cost by 75% and the weight by 90%.
But CAD design, as magnificent as it may be, is just half of the equation. Manufacturing complex geometries is challenging, even in the AM world. Luckily, The Inkbit Vista™’s wax support system allows for unparalleled design freedom that unlocks the full potential of the optimization process.
In this instance, the internal channels of the manifold have been optimized using a sophisticated algorithm. Inkbit Vista™ was able to print the design successfully on the first attempt, while trying to print this manifold on other systems might require careful and time-consuming adjustments to ensure printability and access to support removal.
Figure C: A look at the internal channels of Figure A, designed to be made with conventional manufacturing methods.
Figure D: A look at the internal channels of Figure B, the Inkbit Vista™ printed optimized part. These channels have been designed for optimal fluid dynamics.
True production quality and scale
Thanks to the Inkbit Vista™’s unique benefits as a production AM platform, we are able to achieve some demonstrable impact:
Inkbit Vista™ prints water-tight parts natively. No post-processing of any kind (save for wax removal) was needed to achieve this final result. Other printing techniques do not output water-tight parts and a secondary process may be needed to seal them. These processes can be long, expensive and might even impact dimensional accuracy – all of which was avoided by printing on the Inkbit Vista™.
Lastly, no matter how advanced the design is, it is nothing without the proper materials to back it up. Luckily, the robust material suite offered by Inkbit provided a solution in the form of the Titan Chem Epoxy, a highly chemically resistant epoxy which proved perfect for this task.
The content & opinions in this article are the author’s and do not necessarily represent the views of ManufacturingTomorrow
Comments (0)
This post does not have any comments. Be the first to leave a comment below.
Featured Product
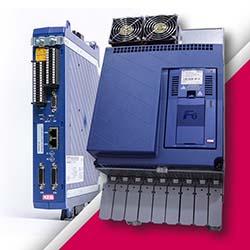