Here we will introduce you to some useful health and safety metrics your organization should be tracking both to show where you currently stand and to help you set future goals for your safety program.
8 Safety Metrics to Start Tracking Today
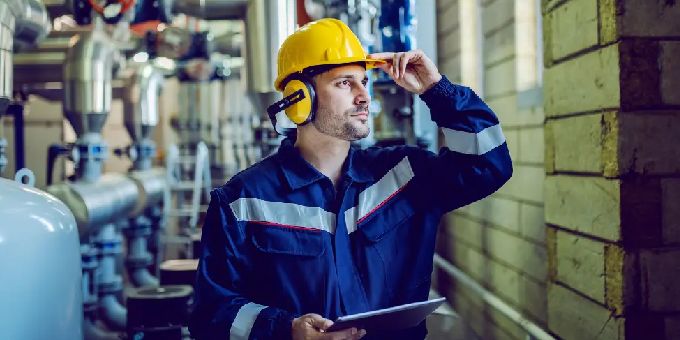
Article from | Safety Skills
As technology improves and has become the norm throughout our daily lives, companies within all different industries are relying more and more on hard data to drive business and personnel decisions. One important area where data can prove extremely helpful is health and safety.
Utilizing safety metrics in general makes sense for any company. We can all understand that it is important to know, for instance, how many on-site injuries have occurred. But what else should you be paying attention to? And how can this data help?
Here we will introduce you to some useful health and safety metrics your organization should be tracking both to show where you currently stand and to help you set future goals for your safety program.
The Safety Metrics You Need to Know
Before diving into a few of the EHS metrics that might be beneficial, we want to recognize that every team, department and organization is different, with their own needs and challenges, which means the same metrics will not help every group. Once you have decided which metrics to track, keep in mind that they don’t have to be permanent. You can always reevaluate and adjust your metrics as needed.
Below you will find eight metrics that any company can benefit from. These are all basic measures of safety and are useful both for serving as a baseline to start tracking information as well as to measure against as your safety program evolves and improves.
Company-level metrics
- Incidents and near misses. If you have done any research into safety metrics, you have probably come across the term “lagging indicators,” which are bottom-line numbers that evaluate overall safety. Both incidents and near misses are incredibly important to note no matter what other metrics you choose. You need to know where your safety stands.
- Lost workdays. Another standard lagging indicator, this will show you how many days of work were lost due to injury or illness. This can give you more insight into the severity of worksite incidents. While any incident on the job is not good, one that only requires basic first aid and no time missed is clearly less detrimental.
- Employee training. This is our first example of a “leading indicator,” which focuses on future safety performance and continuous improvement. At a company level, you might want to track the total number of training hours or what percentage of the company is trained at any given time.
- Inspections and audits. This leading indicator not only gives you insight into unsafe equipment or working conditions, but will also make note of potentially unsafe habits — intentional or otherwise — being performed by your employees.
- Corrective actions. If you are unfamiliar with this term, a corrective action simply prevents an unwanted behavior or result from occurring. For this leading indicator, it would be helpful to track actions both assigned and completed. It is just as important to know what is not being completed as to know what is.
Employee-level metrics
- Training. This will differ somewhat from the training metric noted above. At an employee level, it can be helpful to track training that has been assigned vs. training that has been completed, either at an hour or a course level. This shouldn’t be used to single out any employee, but instead can be helpful to let management know where they need to focus.
- Toolbox talk attendance. You may already be aware of the benefits of holding toolbox talks, but if you are not, it is time to learn. Whether you just start implementing them or you have been holding them for years, making note of employee attendance can show what percentage of your workforce is actively, and regularly, involved in safety.
- Closed corrective actions. This is also similar to safety training noted above and can be helpful on both a company and an employee level. At the employee level, it is crucial to know if workers are being assigned corrective actions that are not being completed. This is important both for the safety of that employee but also potentially for the safety of their coworkers.
As your organization becomes more mature in its safety program, you can always add more detailed metrics to your list to track specific health and safety behaviors. Here are a few you may want to consider.
Preventive actions, which are essentially the opposite of corrective actions in that these work to prevent unsafe actions. When employees take a preventive action, this keeps everyone safe from the get-go.
Recognitions for safe behavior not only help boost employee morale, but they make it clear that these types of behaviors are encouraged. This could be as simple as an employee shoutout or as involved as providing some sort of reward.
Repeat negative findings on audits help you to see that continued best practices are being put into place regularly. This of course is encouraging from a safety standpoint, but it also shows that employees are staying smart and safe.
Tracking Your Metrics
As mentioned, the specific safety metrics that can best help will vary from company to company, and they may also change over time. What is important is that you make yourself aware (if you aren’t already) of where your safety program is lacking and find the metrics that will help you fill those gaps. That might mean overall employee training or it might mean incorporating simple toolbox talks to your workers’ schedules. Only you can determine what is best.
Once you have decided which handful of metrics to track, the next step is to make note of where your team stands now, before you implement any changes. This will give you a baseline to start from and will show you how to adjust your focus. You will likely find that some areas need more focus than others; this is normal and getting a starting point will help you determine this.
You will need to set a goal for each EHS metric, whether that be reducing injuries by a certain percent or increasing the frequency of inspections. It might be helpful to track the metrics for a couple of months to begin with so you know you are setting goals that are both actionable and achievable. We all want to have 0 injuries each year, but that isn’t very realistic in most instances.
Finally, be sure to analyze your tracked data regularly and adjust as needed. This means both adjusting the goals you have set for your chosen metrics but also potentially adjusting the metrics you decide to track. Perhaps by increasing the number of inspections, you uncover a safety issue that needs to be addressed and leads to a new metric. No worries; you can simply add it to your list.
Partner With an Experience Provider
As we head toward the second half of the year, now is an ideal time to start considering which metrics might work best for your organization and determine how you want to keep track of all of this data.
For more than 20 years, SafetySkills has made occupational health and safety training easy, no matter your industry, job or location. Contact SafetySkills today to see how we can help you get started on improving your safety program.
The content & opinions in this article are the author’s and do not necessarily represent the views of ManufacturingTomorrow
Comments (0)
This post does not have any comments. Be the first to leave a comment below.
Featured Product
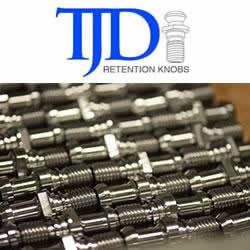