To keep pace with economic demands in an increasingly competitive landscape, manufacturers must aggressively adopt strategies that address the industry’s generational skills gap and accelerate digital transformation.
Adopting These Trends Will Help Manufacturers Reach the Future of Work
Robin Fleming, Co-Founder & CEO | Anvl
Increasing worker productivity and bridging communication gaps is crucial for manufacturers to reach the future of work in 2022. To keep pace with economic demands in an increasingly competitive landscape, manufacturers must aggressively adopt strategies that address the industry’s generational skills gap and accelerate digital transformation by going mobile and capitalizing on the use of data from a productive workforce.
Engage the next generation workforce.
The manufacturing industry faces a critical skills gap in the wake of the pandemic. By 2030, the skills gap could lead to 2.1 million unfilled manufacturing jobs and a $1 trillion negative impact on the economy. Today’s manufacturers struggle to attract and retain new talent, especially Millennials and Gen-Z. Moving forward, the industry must make a concerted effort to address this skills gap and labor shortage as the “Great Resignation,” or the widespread trend of workers leaving their jobs during the COVID-19 pandemic, continues to impact the industry.
According to recent research by Jobvite, workers are demanding that their voices be heard. Organizations that implement applications that enable worker productivity and engage workers in safety and quality will emerge as leading employers and retain and recruit the best talent. Adopting mobile Connected Worker applications is one way for employers to act on real-time feedback and provide in-the-moment support that enables a safer, more engaging workplace and drives continuous improvements.
Go mobile.
More than 96% of younger workers already have smartphones, so leveraging mobile Connected Worker applications will be vital in engaging this generation. Using digital technology is an expectation for younger workers, and manufacturers that adopt new mobile applications are less likely to cause friction or require time-consuming training sessions. The right mobile applications also increase engagement, encouraging the most knowledgeable workers to be leaders in data collection and sharing best practices. Companies that use mobile applications to unlock data and discover what's happening in real-time can identify patterns and trends and act quickly on the information.
According to IDC, 70% of all organizations will have accelerated the use of digital technologies by 2022, and mobile Connected Worker applications will play an important role in transforming existing business processes to drive worker productivity and business resiliency.
Utilize data and insights from your productive workforce.
Companies still on paper and with no digital transformation plans are already behind, and those in the midst of or completing digital transformation will have the competitive advantage. As McKinsey notes, digital is no longer optional. Investing in mobile Connected Worker applications that capture data in real-time will be key for business leaders at this critical stage in industrial innovation.
Capitalizing on data from frontline workers gives businesses greater insight into operations to better track metrics and indicators. Organizations are gaining insights through mobile Connected Worker applications, unlike data trapped on paper and electronic forms. Data captured digitally provides leading indicators that support real-time visibility for decision making, workforce engagement, and continuous improvement.
Reach the future of work.
Industry and market trends will continue to catalyze organizational changes in 2022, and companies who leverage mobile Connected Worker applications will not only have a competitive edge but will be more resilient in the face of future challenges. Engaging the next generation workforce by accelerating digital transformation and proactively addressing real-time findings in safety, quality, and operations will drive the manufacturing industry toward the future of work.
About Robin Fleming
Robin Fleming is the co-founder of Anvl, an award winning software company helping companies unlock real-time data to improve product quality, safety and productivity. Anvl's easy-to-use connected worker platform has collected over 16 million leading data points and routinely sees over 90% engagement from their user base.
The content & opinions in this article are the author’s and do not necessarily represent the views of ManufacturingTomorrow
Comments (0)
This post does not have any comments. Be the first to leave a comment below.
Featured Product
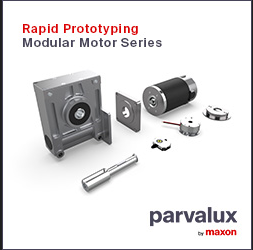