Additive Manufacturing is not intended to replace conventional or traditional manufacturing, but rather compliment it. When implemented correctly, AM offers manufacturers real flexibility and design freedom while enabling more resilient and robust value chains.
Are You Fit for 3D Printing Success?

Fabian Alefeld is the North American Manager for EOS’s Additive Minds consulting practice | EOS
As you read this sentence, there's likely a 3D printed part flying over your head. There are additively manufactured (AM) devices in human bodies and driving in our vehicles. New and amazing parts produced additively are announced seemingly every day.
AM technology is here, and its applications go well beyond the cool or futuristic.
AM is not intended to replace conventional or traditional manufacturing, but rather compliment it. When implemented correctly, AM offers manufacturers real flexibility and design freedom while enabling more resilient and robust value chains.
Industrial 3D printing is fast becoming an essential tool in the toolbox for many organizations who use it to help restructure research and development, bolster product portfolios—the list of benefits rapidly growing.
The problem is, many manufacturers aren't ready for it.
Not only is bringing on AM more difficult than companies realize, but it also entails a rewiring of how your business operates.
It’s a new advanced manufacturing process and cannot be seen as similar to other conventional methods. As such, it requires a new way of thinking on the manufacturing side and on the engineering and design sides.
One of the most common hurdles is getting stuck in pilot purgatory. An organization's first foray into AM is often through a small project and not every application or assembly is “right” for AM. Without proper planning, knowledge, and upfront investments in time and resources, these projects inevitably fail.
AM requires consideration in all areas of your organization that can lead to frustrations with different groups, exclaiming that "additive isn't quite ready yet" and "let's look at it later down the road."
Suddenly, you're in a position where just because you selected the wrong application in the beginning or focused on the wrong vertical or value, everyone decides the problem is AM, and the tech gets sidelined.
The thing is, implementations can take multiple years, and quite frankly, the longer you wait, the wider the competitive gap will get. It’s better to seek outside consulting help to get your first application off the ground than to write it off entirely because you don’t have the expertise (yet).
Getting ready for AM
Once you decide to take on 3D printing capabilities, there are some fundamental areas you must nail down before getting started.
Today we’ll focus on two. The first involves looking at the whole value chain and identifying challenges and opportunities for your business. The second is the education and knowledge in and around AM at an organizational level.
Creating added value
Getting started with 3D printing doesn't begin with digitalization or engineering. It starts with analyzing your value chain as a business and identifying specific challenges to consult with AM.
This process creates value: an essential step, whether it's in your supply chain or for your customers.
Frequently with 3D printing, if you look at the production cost alone, it might be more expensive than a casting application. But if you take into account reduced lead times, shortened innovation times, and that you now can, for example, get rid of minimum order quantities, all of those factors sum up into a net value-add of that application. Now you're creating value and contributing to the bottom line of your organization.
In the end, if you can't add value to your operations with this new technology, then you're creating a parallel stream of manufacturing that doesn't impact your business in a scalable way.
Building up internal knowledge
As mentioned, industrial 3D printing is a totally new type of technology. Yet, many manufacturers underestimate the need for educating people and cross-functional teams on the limitations and opportunities it brings.
For success, your business needs to “think additively."
In other words, you need to ingrain an AM mindset and regard it as a viable tool through education and training.
The groundwork you do in fostering your workforces' knowledge and expertise will evolve into competitive advantages, as well as opportunities to scale 3D printing throughout your organization.
Those challenges you identified? Extensive internal knowledge turns those into disruption and the disruption into opportunistic growth. Education will spark ongoing evolution within your organization, turning your first industrial 3D printing use cases into more applications.
An upfront investment into your future capabilities
Almost all conversations around AM are centered around engineering. However, it needs to be looked at as a strategic tool for bolstering competitive advantages, one that will impact your entire organization—but only under the right circumstances.
It's not easy, and it takes a commitment of time and resources to set the foundation of a scalable approach and determine where it can be most impactful to your business.
Most importantly, while this is an essential exercise for your business, you don't have to go through it alone. Look for a partner with end-to-end experience who can help you identify use cases and translate them into opportunities.
After all, when used in the right way, AM becomes an essential technology; you’ll wonder how you ever got on without it.
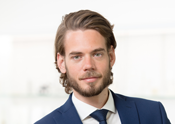
Fabian Alefeld is the North American Manager for EOS’s Additive Minds consulting practice, which works with organizations across a variety of industries to maximize their efforts at every stage of the AM journey from start to part.
The content & opinions in this article are the author’s and do not necessarily represent the views of ManufacturingTomorrow
Comments (0)
This post does not have any comments. Be the first to leave a comment below.
Featured Product
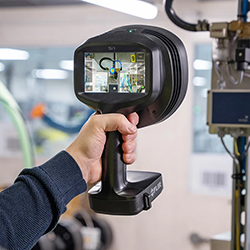