Ensuring seamless laser weld quality control and manufacturing traceability, the monitors catch weld errors as they occur in real time, instead of reacting to defects downstream. This ultimately increases yield, improves quality, saves labor, and increases savings.
New Laser Welding Process Monitoring Systems Ensure Data Traceability
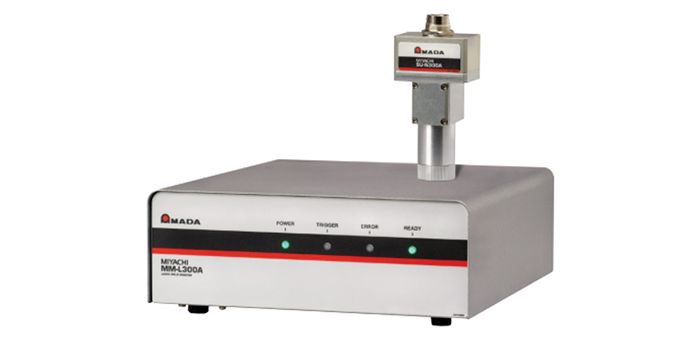
Mark Boyle, Product Manager, and Minh Si, Product Engineer | AMADA WELD TECH
In the transition towards the Internet of Things (IoT)/Industry 4.0, manufacturing facilities are rapidly moving towards technology that can help with remote monitoring of equipment health, offer process analysis and data storage, and improve overall equipment efficiency. Establishing the smart factory via the integration of equipment and devices, the ultimate goal is manufacturing traceability to analyze and interpret process trends and improve quality.
In recent years, a number of laser weld monitors have been developed that further these data analysis and storage goals. Ensuring seamless laser weld quality control and manufacturing traceability, the monitors catch weld errors as they occur in real time, instead of reacting to defects downstream. This ultimately increases yield, improves quality, saves labor, and increases savings.
One key example is high-resolution laser welding monitors like AMADA WELD TECH’s MM-L300A, which can detect production errors in spot or seam welds. In addition to detecting gaps between parts and incorrect focus, the technology detects missing parts, over-penetration, and cover gas absence to provide operators real-time feedback on laser weld quality.
The weld monitor records data and adds it to databases for future analysis and monitoring of laser welding processes. The data can be output for analysis by statistical process control program (SPC programs), including Minitab and Tableau interactive data visualization software.
Laser weld monitoring basics
A number of factors, including material and plating selection, equipment capability, and process settings, determine whether a laser welding process is likely to be successful. Measuring success is usually based on a design of experiments (DoE) study performed to determine the range of output based on the variation of input parameters. The result is then used to set boundaries around the measurable input parameters to infer whether the process is successful. After implementation, the welds are periodically checked via testing to confirm success. While this increases likelihood of success and certain inferences can be made for adjacent welds, it does not provide 100 percent certainty.
Even when weld parameters are properly dialed in, a number of things can go wrong during manufacturing that affect weld quality. The more production that occurs with faulty parameters, the greater the chance that a production recall could occur. Common examples include:
-
Damaged parts from mishandling
-
Improper loading of part(s)
-
Parts out of focus
-
Insufficient cover gas
-
Low laser power
-
Change in material composition or plating
-
Gap between materials
Using real-time laser weld monitoring to reduce production problems
Laser process monitors automatically observe the process to determine success. During the weld, the monitor records a number of measurements to provide information about the weld, including laser radiation, the heating process, and weld penetration. Radiation wavelengths and sound frequencies can be collected.
One method is to measure the thermal characteristics during the welding process. The material is locally heated and will emit radiation that is temperature dependent. This signal can be detected and recorded versus time. Each weld will have a unique temperature-time profile. Once this waveform is defined through multiple measurements, it is possible to set upper and lower limits for variation and comparative measurements can be made. Some laser welding monitors use thermal imaging to collect radiation from the weld zone. The 1300-2500 nm range corresponds to the melting point of common metal materials.
There are a number of benefits to real-time monitoring a weld, including traceability, failure detection, and increased product throughput. Real-time monitoring provides the opportunity to record measurements for 100 percent traceability.
In today’s networked world, data and data analysis are becoming increasingly essential in the manufacturing sector. Laser weld monitoring systems enable collection of data that can be stored (locally or on a network), and later accessed for tracking, tracing, and analysis. The data becomes invaluable for determining the root cause in the event of a product recall.
The laser weld monitor measures the signal and compares it to a known good reference. This is a first line of defense that can indicate whether a weld was successful or not. Laser weld monitoring can reveal weld errors as they occur, instead of after production, which increases throughput and lowers scrap. The earlier issues are caught, the greater the cost savings.
During production, samples are tested to ensure quality; any weld test failures may lead to scrapping of an entire lot of parts. By measuring the thermal time waveform as the weld occurs and comparing to a known good reference, instantaneous detection of errors can be made for each and every part. If something goes wrong, a signal can be sent, and the offending part can be separated out. Production can be held until the issue is resolved and production of good parts can continue.
In addition, knowing whether a weld is good while the welding process takes place greatly enhances production line efficiency. Relying on a high-precision monitoring system reduces the number of additional cross sections and destructive testing a manufacturer must do to ensure a weld is of good quality.
Without real-time process monitoring, users cannot see errors until after welding has completed and quality inspection has begun. The number of parts a manufacturer may have to discard depends on how often the weld is being checked. For example, if welds are only monitored at the end of the day and an inconsistency is detected, a company may have reason to suspect that all welds made that day would be compromised.
Using real time laser welding monitors like AMADA WELD TECH’s MM-L300A can prevent costly errors from becoming a reality. Determining weld success by detecting and recording a thermal signal from the area of laser interaction, the monitor provides the user an output waveform around which maximum/minimum or envelope limits can be set. Once these are in place, the unit compares a new weld waveform in real time to identify a weld whether the weld is good or not.
Customers demonstrating the equipment call it a potential step forward in welding process technology, enabling operators to analyze processes and ensure better routing of materials to different workstations. According to one customer, “This technology is enabling me to look at the welding process in different ways than in the past. It allows me to store information on each weld, so if we ever need to go back, we have a recording and traceability of that weld.”
High-precision monitoring system critically important for micro-welding applications
In the micro-welding world, because the parts are small, the heat input (laser pulses) are typically a few milliseconds or faster. In order to properly measure the weld during the laser pulse, the sampling rate must be faster, so multiple recordings can be made during the weld.
For accurately determining weld quality, precision is paramount. A high-precision monitoring system that samples the signal more quickly allows the user to see very fine distinctions in the weld that would not be otherwise observable. A monitoring system that samples every microsecond instead of every millisecond enables the user to view with precision the fine details of the weld, including any anomaly occurring between the two measured points of a slower monitor. The MM-L300A provides high temporal resolution – down to one microsecond – and enables precision monitoring, thanks to its SU-N300A dedicated thermal sensor.
Increased monitoring system precision is ideal for many micro-welding manufacturing applications, including automotive and medical device manufacturing, which requires traceability and reliable results from part to part. Knowing each and every weld is going to be successful is a key factor driving the increased implementation of monitoring systems into existing manufacturing configurations.
Implementing a monitor into a welding production line can significantly increase a manufacturer’s return on investment. High-precision monitoring systems can help customers understand and target problems to get successful welds each time, thus achieving improved yield. This is crucial for medical device manufacturing, since a great deal of processing goes into a particular part before it is welded. Each of these medical parts can cost tens of thousands of dollars or more. Having to discard welds that are not good wastes manufacturing time up to that point, as well as the value of the product itself.
Other errors that can be detected include incorrect positioning or bent pins, which might not always be observable by visual inspection alone. The smaller and thinner materials are, the more likely they are to get bent or positioned incorrectly. Thus, monitoring is a major asset to the micro-welding sector, as monitoring systems can capture very fine defects that might be too minute for visual inspection to detect.
For example, AMADA WELD TECH’s MM-L300A is easy to integrate into a laser welding workstation. The sensor can be mounted in both on-axis (through a focus head) or off axis configurations to monitor the signal. The unit offers Ethernet and RS-232 output signals that can be connected to a PLC and or a network.
Click on the link to see a short video showing a seam weld with a defect (damaged edge) introduced in the middle of the weld. The increased gap, where the part was damaged, causes the signal recorded by the monitor to go below the normal lower limit for a good signal. In the video, the weld continues until completion. However, it is also possible to immediately stop the weld and discard the part. Error handling is part of the system design.
Automation, data technologies and integration to improve quality and throughput
New computing capacity, data communication technologies, and enhanced network access are increasingly being used by plant managers and product line managers to check in on their production lines anywhere in the world. Looking at data, they can identify equipment requiring preventive maintenance and analyze statistics to find bottlenecks in the production lines. Using real time laser welding monitors like AMADA WELD TECH’s MM-L300A can prevent costly errors from becoming a reality. Operators can use the growing connective capability for data communication and data storage to enable traceability to optimize processes and equipment health. This in turn results in quality and throughput improvements.
The content & opinions in this article are the author’s and do not necessarily represent the views of ManufacturingTomorrow
Comments (0)
This post does not have any comments. Be the first to leave a comment below.
Featured Product
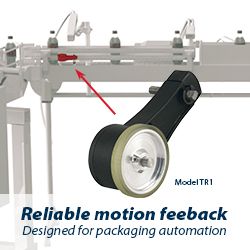