Manufacturing plant cleanliness was a hugely important topic long before the global outbreak of COVID-19. However, recent events have thrown this issue into even sharper relief.
How to Keep Your Manufacturing Plant Clean
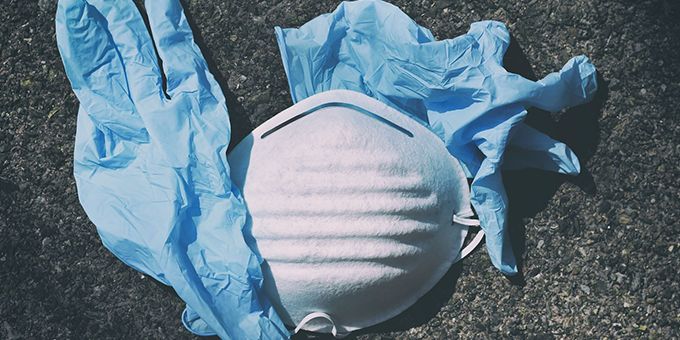
Megan Ray Nichols | Schooled by Science
Manufacturing plant cleanliness was a hugely important topic long before the global outbreak of COVID-19. However, recent events have thrown this issue into even sharper relief.
The following recommendations are relevant in a wide variety of manufacturing settings. We’ll start with some general cleanliness suggestions that apply no matter the external circumstances. The second half focuses on what manufacturers can do to keep coronavirus from impacting their work.
Keeping Manufacturing Plants Clean
Basic cleanliness and organization go a long way in keeping facilities safe for all.
1. Keep Workspaces Organized
Keeping workspaces and facilities clean and neatly ordered is one of the most important steps for manufacturers. Doing so helps workers stay safe, keeps essential parts and tools where they can be easily found, and improves overall productivity.
One of the highest-priority action items in workplace organization is designing the facility so everything has a place.
Employees should know where to find the tools, equipment and materials they need to get their work done. They should also be sufficiently trained in 5S and other protocols so they know to return items to their place once they’ve finished working with them.
5S stands for sort, straighten, shine, standardize and sustain. Think of it as an ongoing mindset and a way to cultivate pride and ownership in each employee.
2. Minimize Travel Between Workstations
Manufacturing sector employers should take the time to map out and take a fresh look at the physical layout of their plants.
Doing so may reveal opportunities to shorten the distance employees travel between steps in your manufacturing processes. Reducing cross-traffic is a good general safety measure, as it could serve to minimize collisions and other mishaps when vehicles or personnel cross paths.
It also reduces the chances of employees misplacing tools or damaging products on their way to their destination. Even something like wooden pallets benefit from reduced travel time, as they’re less likely to splinter or crack from the additional handling and leave debris scattered around the facility.
3. Train Employees to Report or Address Spills Quickly
Slip-and-fall accidents result in approximately 1 million emergency room visits each year, making them some of the most common incidents in industrial settings. Keeping your manufacturing facility clean and safe requires two things:
-
Attention to surroundings: Employees should be aware of their surroundings at all times. This helps maintain sure footing, but it also goes far in policing critical areas for spills and hazards. For facilities with maintenance staff, “see something say something” applies. Employees should report spills and other issues to relevant personnel.
-
Willingness to go the extra mile: Employees should be willing to address some types of spills themselves rather than leave it for the next person to deal with. Water pooling from a leaking cooler or dock seal is simple enough to ameliorate. Leaking cleaning supplies or other industrial chemicals should be left for professional and properly equipped staff members, however.
4. Stick to Regular Equipment Maintenance and Cleaning Schedules
Factories are home to lots of vital equipment. Keeping these machines running safely is a matter of ongoing maintenance and cleaning. Don’t assume these processes will take care of themselves. Instead, create a schedule for your trained personnel to follow.
Deep-cleaning and replacing worn parts probably won’t happen daily, but spot-cleaning equipment is still something employees can do during normal operational hours. Before beginning a shift, workers should look over their machine and wipe any dust and debris from its surfaces and any moving parts.
Involving employees in regular cleaning requires that you keep their workspaces well-stocked with basic supplies. Include mild cleansing products, paper or cotton towels, and gloves and goggles.
Tips for Maintaining Cleanliness During COVID-19
As mentioned earlier, the outbreak of COVID-19 has changed the game when it comes to keeping manufacturing facilities clean. With many essential workplaces already operating with reduced crews, it’s more important than ever to keep our workspaces clean and safe for all.
What can manufacturers do to keep their plants extra-clean while creating necessary items during the COVID-19 outbreak?
1. Don’t Take Handwashing for Granted
It’s not wise to assume everybody on your payroll holds proper handwashing techniques in equal esteem. According to the CDC, it's one of the most important steps to take to prevent the spread of illness.
It’s wise to model your own safety and cleanliness training after the CDC’s handwashing resources. Employees should visit the restroom to wash their hands:
-
After using the bathroom
-
After coughing, sneezing or blowing their nose
-
After handling or transporting garbage
Before touching sensitive materials, such as food product
2. Train Employees on Proper Use of PPE
With only a handful of exemptions, OSHA requires employers to provide personal protective equipment (PPE). Manufacturing environments contain chemicals, equipment and other potentially hazardous features at the best of times — but properly responding to COVID-19 requires even more conscientious attention to PPE training.
Distributing and wearing PPE is typically thought of as a method for keeping employees injury-free, but with a highly communicable virus on the loose, they’ve taken on an especially important role in keeping our workplaces clean. Proper use of masks, gloves, goggles and other PPE is more important than ever.
The CDC recommends businesses train their cleaning staff to report lapses in or improper use of PPE whenever they see it.
3. Use UV Lights to Sterilize Equipment and Surfaces
The most difficult part of keeping viruses and bacteria at bay is that the former does not respond to antibiotics or antibacterial products, and the latter may mutate until it resists such treatments.
Scientists rank pathogens according to how well they tolerate disinfectant efforts. The good news about COVID-19 is that it falls into Class 3 — “enveloped viruses” — which are comparatively easier to kill than other varieties.
Testing on the novel coronavirus has been limited, but Class 3 pathogens are susceptible to sterilization techniques that use UV light. In theory, that includes COVID-19.
Constant exposure to UV lights can degrade a surface over time, but brief and intermittent bursts can help fight off fungi and mold as well as bacteria and some viruses. They could be a useful cleanliness tool for manufacturers even without the threat of a deadly disease in the mix.
Factory Cleanliness Is a Shared Responsibility, Especially Now
Keeping our workplaces safe and clean has always relied on team efforts. Now, amid a global pandemic, this attention to detail and sense of community responsibility is even more critical. Keep your facility clean and your personnel safe by doubling-down on your cleaning and training. We’re all in this together.
The content & opinions in this article are the author’s and do not necessarily represent the views of ManufacturingTomorrow
Comments (0)
This post does not have any comments. Be the first to leave a comment below.
Featured Product
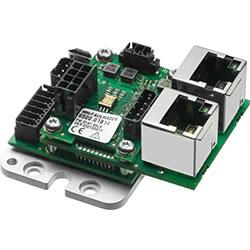