Manufacturers are in a unique position to make a real impact on the total waste that's produced in today’s market. That’s critical to understand because industrial waste is one of the most significant forms of matter dirtying up our world outside of municipal waste.
How to Handle Manufacturing Waste
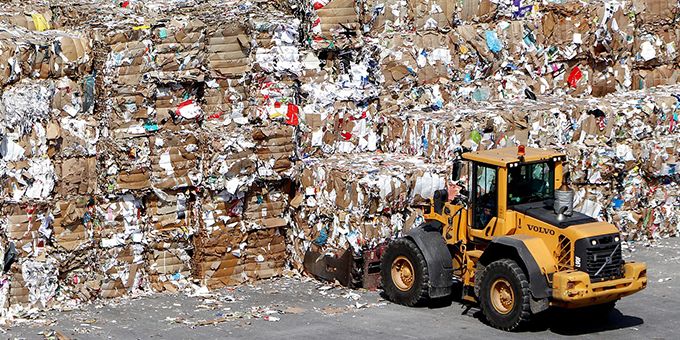
Emily Folk | Conservation Folks
Manufacturers are in a unique position to make a real impact on the total waste that's produced in today’s market. That’s critical to understand because industrial waste is one of the most significant forms of matter dirtying up our world outside of municipal waste. In 2017, the total amount of municipal solid waste (MSW) was 267.8 million tons, or a little over 4.5 pounds per person per day. Some estimates put industrial waste alone as high as 7.6 billion tons per year.
If anything, those numbers show that waste is a great concern when it comes to output and environmental impact.
From there, the next question is how to reduce waste using modern techniques and solutions. What can manufacturers do to limit the waste production of their operations?
Waste Reduction in Action
Ultimately, there’s no way to eliminate waste production, as there is always going to be some byproduct of development and industrial processes. It’s true whether you’re talking about chemicals, solid goods or another product. That said, with the right protocols and techniques in place, manufacturers can reduce waste as much as humanly possible. To achieve such a thing, organizations must implement minimal footprint goals at a foundational level. Here are some tips to make it happen:
-
Generate an accurate profile of waste generation across an operation: Which areas or departments produce the most waste? What type of waste is being produced, and at what amounts? Can fundamental revisions help reduce waste? For example, switching from paper-based goods to a green alternative like recycled stationary is a good option. Another example might be eliminating the use of conventional plastic for a more eco-friendly option.
-
Prioritize the cleanup process by focusing on the biggest producers of waste: It might seem like a good idea to overhaul the entire operation in one swoop, but doing so would likely cause more problems than it would solve. It’s best to take a slower approach to ensure waste reduction techniques not only take hold but are effective.
-
Create a committee, department or team exclusively to deal with waste reduction: Their first task should be to establish a waste inspection protocol for regularly assessing levels within the organization. Without measurement standards, there’s no way to know or even identify when things are improving or worsening. The team should also be responsible for monitoring the manufacturing floor and environment, specifically to keep everything clean and effective. Think internal waste auditors or inspectors.
-
Find an environmentally compliant disposal partner: Be sure the partner is actually following the appropriate process for removing and disposing of waste. Some organizations might claim to handle and dispose of waste using eco-friendly means, but that’s not always the case. The best way to find a suitable partner is to look for one that’s continually improving and not just settling on its current state of compliance.
-
Move to a closed-loop manufacturing (CLM) process: Doing so will offer many benefits in addition to less waste. Closed-loop systems help reduce costs, improves the quality of products and goods and allows for the use of recycled materials internally. It’s essentially a form of lean manufacturing that reduces the operational footprint and boosts profits.
-
Learn to recycle or recover and reuse: In many cases, the waste produced by an organization never gets a proper assessment, but those supplies or materials may yet serve a purpose. Many items can either be cleaned, reused or repurposed within the operation to extract further value. Furthermore, some processes can restructure materials for different purposes. Methods like filtration, electrolysis, centrifugation and reverse osmosis can help clean or modify the waste for repeated use. Consider these other processes when you're deciding what to do with waste — or more specifically identifying when it’s genuinely waste and nothing more.
-
Either curtail or tighten up the use of hazardous materials: There are times when alternative supplies may be a better option, especially when they aren't as dangerous as the conventional option. If that’s not a possibility, the use of hazardous materials should be monitored and limited as much as possible to cut down on the subsequent waste. Hazardous materials are both dangerous and difficult to properly dispose of, especially in the context of green and eco-friendly operations.
Waste Reduction Is Imperative in Today’s Market
While the concept of waste reduction can seem daunting, especially in the face of legacy operations, there are many benefits realized from its implementation. For starters, less waste means a lower footprint, or minimal impact on the environment and surrounding communities. As demonstrated above, it can also mean higher profits, better quality goods and services and even a more positive reputation for the organization — which comes with a separate series of benefits, like customer loyalty.
Any way you cut it, waste reduction is — and will continue to be — imperative for adequately sustained operations in today’s market.
If you like this article you may like "Advanced Metrology Tools Enable Reliable Engine Light-Weighting"
The content & opinions in this article are the author’s and do not necessarily represent the views of ManufacturingTomorrow
Comments (0)
This post does not have any comments. Be the first to leave a comment below.
Featured Product
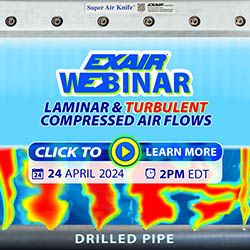