Using digital twin and digital thread technology, A&D manufacturers can conduct automated assessments to analyze the performance of aircraft components – an advancement that has significant implications for the industry.
Automating Assessments in A&D for Improved Quality
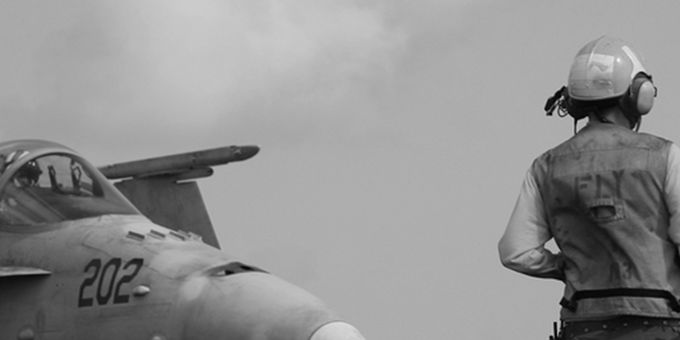
John Rassieur, Managing Partner, Digital Manufacturing Transformation | Americas Consulting, DXC Technology
Aerospace and Defense (A&D manufacturers have a powerful new tool at their disposal — one that can help them dramatically cut costs while improving the quality of the parts they build.
Using digital twin and digital thread technology, A&D manufacturers can conduct automated assessments to analyze the performance of aircraft components – an advancement that has significant implications for the industry.
Consider an airfoil, the blade of a jet engine turbine.
Airfoil blades are designed to move high volumes of air, which is heavily dependent on the blade’s shape. The blade has to be designed to meet engine thrust requirements – the manufacturer also has to live up to the design by delivering the performance required. If it doesn’t, the blade won’t create the level of thrust needed from the engine.
To assess quality, manufacturing engineers typically use a combination of manual inspections and the interpretation of process data as its produced. This approach, however, is costly and time consuming.
Alternatively, A&D manufacturers can leverage digital twin technologies in conjunction with taking the following steps to automate this tedious process:
-
Define the features and characteristics of the airfoil — the dimension points that reflect its design.
-
Connect those features and characteristics with the shop floor activities — the robotics, the computerized measuring equipment and the machine tools.
-
Measure those changes and bring the data generated by these systems into a data lake. Every machine, tool and die used in the production process can affect the resulting airfoil’s performance.
-
Ensure that the process variables are all under computerized control in order to ensure that the right airfoil design is being machined. Once the variables are under control, adjustments can be made for even the slightest changes in the process, whether it is the toolware, the environment or other factors.
-
Feed all this information into an analytics system and integrate it with the manufacturing execution system and the material requirements planning system.
Introducing the Digital Twin
This is where things get interesting.
The manufacturer now has a digital view of the entire process, with detailed knowledge of how each step will affect the dimension points of the finished product. The manufacturer is now empowered to create a digital twin of the airfoil.
In essence, a digital twin is a digital model of a physical asset, which the manufacturer can use to produce real-time visualizations of applications. The manufacturer can put the digital model into different hypothetical scenarios.
Through high-performance computing, the manufacturer can see how the asset would perform against the laws of physics baked into the visualization’s algorithm.
In the case of the airfoil, it would show how much thrust would be produced under real-life circumstances.
Manufacturers can leverage digital twins to better determine whether their products will meet specifications before they are even produced, enabling them to make changes to correct any shortcomings in advance.
In fact, the analytics engine can make those adjustments to the connected systems — all without human intervention.
Considerable Return on Investment
The development of the digital twin is significant advancement in the manufacturing process, as the cost of rejecting an airfoil blade can be as high as $200,000 – with as many as 80 blades in one engine costs can rack up quite quickly!
Consider the time savings of using a digital twin – without one, it can take as long as two weeks to manually calculate whether a change in blade geometry would affect thrust.
A leading jet engine manufacturer that DXC Technology has worked with has saved tens of millions of dollars by leveraging digital twin technologies while simultaneously resolving 80% of manufacturing issues automatically.
Similarly, the digital twin is being utilized by other A&D manufacturers to show the status of their products in each step of the production process and aftermarket.
For example, a leading airframe manufacturer is currently utilizing digital twin technologies to show individual aircraft as they are being built as a digital model; a leading ship builder is leveraging digital twins to show the actual build of each hull section as the ship is being constructed.
For added bonus, this automated process can be tied into the rest of the supply chain focused on creating a complete engine that is installed in an airplane in a structure known as a digital thread – he blade goes into an engine, the engine into an airplane, and the digital thread connects it all, providing a clear picture of the larger value chain.
Several industry leaders are applying this methodology, highlighting bottlenecks in production and discovering insights that enable them to increase throughput and reduce costs.
Digital twins and digital threads have many applications for ensuring quality manufacturing — applications that go well beyond A&D.
As data from manufacturing processes becomes better and more complete, the possibilities for more efficient manufacturing become much more encouraging.
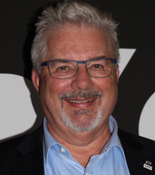
John Rassieur, partner and consulting leader in supply chain, manufacturing operations and aftermarket service management, brings exceptional industry experience in technology enabled solutions. He provides influential thought leadership and valuable guidance for clients in preparing and executing business and operational transformation.
*Title Image sourced from DXC website.
If you like this article you may like "Predictive Analytics vs Machine Learning"
The content & opinions in this article are the author’s and do not necessarily represent the views of ManufacturingTomorrow
Comments (0)
This post does not have any comments. Be the first to leave a comment below.
Featured Product
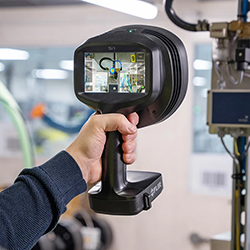